Types of Sand Casting
Sand casting, one of the oldest and most widely used metal casting processes, involves pouring molten metal into a sand mold to create intricate shapes and components. The versatility, cost-effectiveness, and ability to produce complex geometries make sand casting a popular choice in industries ranging from automotive to aerospace. There are several types of sand casting methods, each with its own unique characteristics and applications.
Types of Sand Casting
Another popular technique is dry sand casting, which uses silica sand mixed with a binder that is cured with heat. This results in a stronger mold compared to green sand casting. Dry sand molds can withstand higher temperatures and can be reused for multiple castings, making them more efficient for certain applications. The downside, however, is that the initial setup and process can be more time-consuming and expensive.
types of sand casting
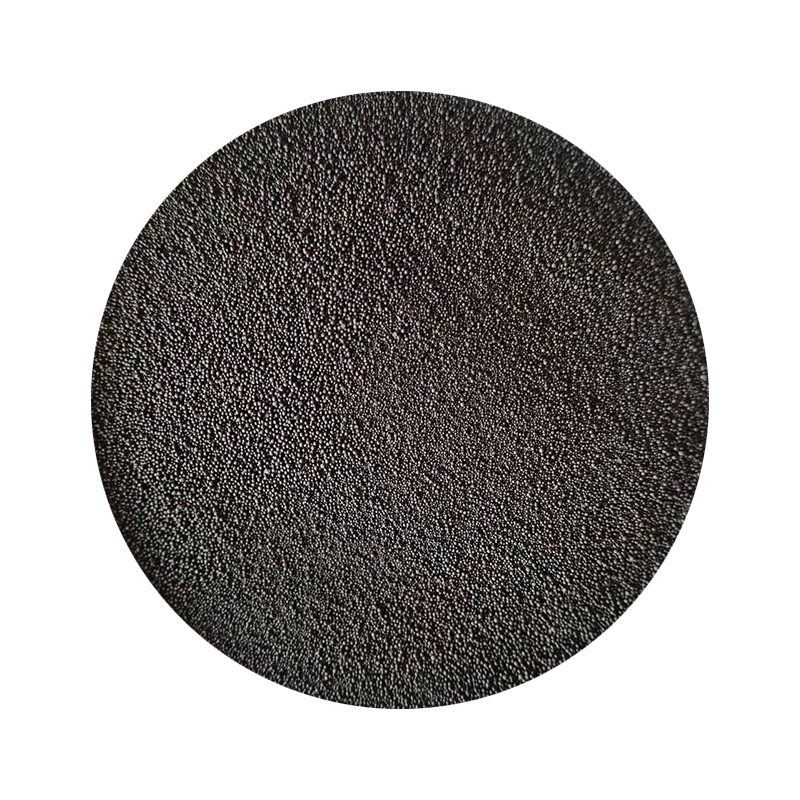
Resin sand casting involves the use of sand that is coated with a resin binder, reducing the permeability of the mold and allowing for finer details to be captured. This method is particularly beneficial for creating complex shapes with high dimensional accuracy. Although resin sand casting produces excellent surface finishes, the cost of resin can increase production expenses, making it less ideal for large-scale operations.
No-bake casting, another variant, involves mixing sand with a chemical binder that sets at room temperature. This technique allows for the rapid production of molds without the need for baking. While it provides good surface finish and dimensional accuracy, the cost of binders can make it less economical compared to traditional methods.
Finally, lost foam casting is a modern technique that uses a foam pattern which evaporates when molten metal is poured, creating a mold in the process. This method is particularly effective for complex parts and offers an exceptional surface finish. However, the pattern creation can be costly and intricate.
In conclusion, the choice of sand casting type largely depends on the specific requirements of the casting project, including design complexity, production volume, and cost considerations. Each method presents unique advantages and challenges that cater to different industrial needs, solidifying sand casting's role as a vital manufacturing technique in today’s engineering landscape.
Post time:окт . 31, 2024 10:41
Next:lost foam casting method