Understanding the Sand Casting Foundry Process
Sand casting, a widely used metal casting process, has become a cornerstone in the manufacturing industry due to its versatility, cost-effectiveness, and capability to produce complex geometries. The process involves creating a mold from a mixture of sand, a bonding agent, and water, into which molten metal is poured to form desired shapes. This article delves into the intricacies of the sand casting foundry process, including its components, steps, and applications.
Components of Sand Casting
The sand casting process primarily involves three key components the pattern, the mold, and the core.
1. Pattern The pattern is a replica of the final product, usually made from materials such as wood, metal, or plastic. It must account for the shrinkage of the metal as it cools, thus it is often made slightly larger than the final dimensions of the casting. Patterns can be single-use or reusable, depending on the production requirements.
2. Mold The mold consists of two halves, known as the cope (top half) and the drag (bottom half). Sand is compacted around the pattern to create the mold cavity. The sand mixture generally consists of about 90% sand and 10% clay, which binds the particles together, allowing the mold to maintain its shape under the pressure of the molten metal.
3. Core For castings with internal cavities, a core is utilized. Cores are made from sand and serve to create voids within the final casting. They are placed in the mold before the molten metal is poured.
Steps in the Sand Casting Process
The sand casting foundry process typically involves several steps
1. Pattern Making The first step involves creating an accurate pattern that represents the desired product. This involves detailed design work to ensure that all dimensions adhere to specifications.
2. Mold Preparation The next step is preparing the mold. Sand is mixed with a bonding agent and water and is then packed around the pattern. Once the mold is formed, the pattern is removed, leaving a cavity that mirrors the pattern's shape. The two halves of the mold are then assembled, and any cores are positioned appropriately.
sand casting foundry process
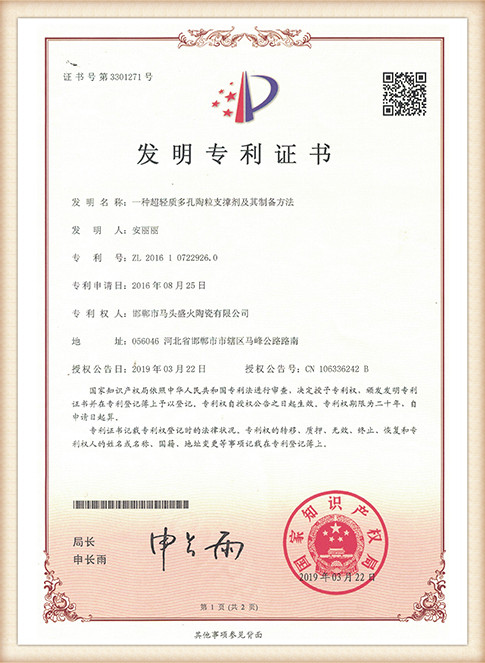
3. Melting the Metal Subsequently, the required metal is melted in a furnace. The type of metal can vary widely, including aluminum, iron, and steel, each chosen based on the properties required in the final product.
4. Pouring After the metal reaches the desired temperature, it is poured into the mold cavity. This step must be carefully controlled to avoid defects such as air pockets or premature solidification of the metal.
5. Cooling The molten metal is left to cool and solidify within the mold. The cooling time can vary based on factors such as the size and thickness of the casting, as well as the type of metal used.
6. Mold Removal Once the metal has cooled sufficiently, the mold is broken apart to reveal the casting. The sand can be reclaimed for future use in the process.
7. Finishing The final step involves finishing the casting. This can include cleaning to remove residual sand, machining to achieve precise dimensions, and surface treatment to enhance appearance and protect against corrosion.
Applications of Sand Casting
Sand casting is used across various industries, making it a vital aspect of modern manufacturing. Its ability to produce large and complex parts makes it ideal for sectors such as automotive, aerospace, and construction. Components like engine blocks, cylinder heads, and intricate machine parts often originate from sand casting processes.
Advantages and Limitations
The advantages of sand casting include its cost-effectiveness, flexibility in design, and the ability to cast large components. However, it also has limitations, such as a lower dimensional accuracy compared to other casting methods and a rough surface finish that may require additional machining.
Conclusion
The sand casting foundry process is a crucial manufacturing technique that enables the production of complex metal parts. Understanding the intricacies of its components and steps can enhance its application in various industries, driving innovation and efficiency in product development. As technology advances, the integration of sand casting with modern manufacturing techniques promises to expand its capabilities even further, solidifying its position as a key player in the world of metallurgy and manufacturing.
Post time:нов . 07, 2024 19:33
Next:Sanding Techniques for Smoother Finishes in Resin 3D Prints