Understanding Sand Casting Components
Sand casting is one of the oldest and most versatile manufacturing processes, used to create a wide variety of components in various industries. The procedure involves pouring molten metal into a mold made of sand, which is packed around a pattern to create a hollow space that defines the shape of the final product. Understanding the components involved in sand casting is crucial for optimizing the process and ensuring high-quality outputs.
Key Components of Sand Casting
1. Pattern The pattern is a replica of the final product and is typically made from materials like wood, metal, or plastic. It serves as a template for creating the mold. Patterns can be made in different types, such as solid, split, or match plate patterns, depending on the complexity of the component being cast.
2. Mold The mold is created by packing sand around the pattern. The sand mixture, often a combination of silica sand, clay, and water, allows for excellent detail reproduction while providing strength to withstand the pouring of molten metal. The two main types of molds are green sand molds and resin-bonded molds, each offering different characteristics and benefits.
3. Core Cores are used to create internal cavities or features that cannot be formed by the pattern alone. They are made from a mixture of sand and a binding agent and are placed in the mold before molten metal is poured. Cores can be removable or permanent, depending on the design of the component being cast.
sand casting components
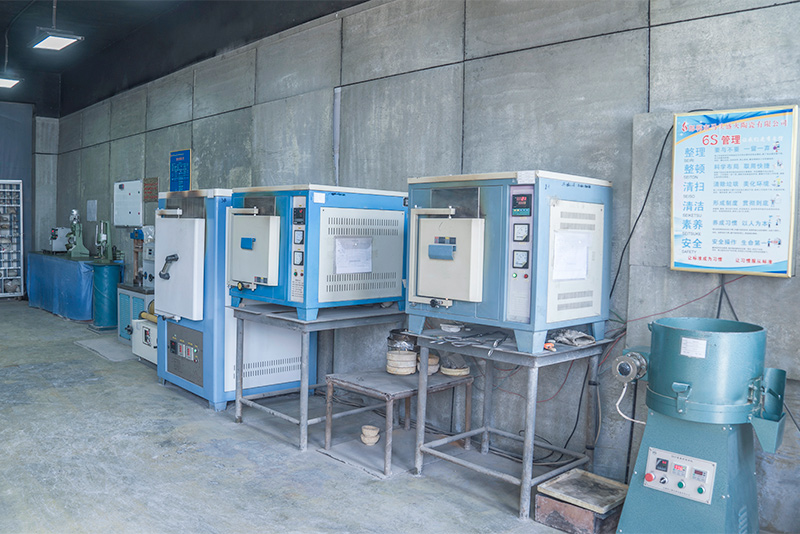
4. Mold Box The mold box, also known as a flask, is the container in which the mold is formed. It holds the sand and ensures the mold maintains its shape during the pouring process. Mold boxes can be simple or complex, depending on the size and intricacy of the mold.
5. Molten Metal The choice of metal is critical in the sand casting process. Commonly used metals include aluminum, iron, and bronze. The metal is heated to its melting point and poured into the mold, filling the cavity formed by the pattern.
6. Gates and Risers Gates are channels that allow molten metal to flow into the mold cavity, while risers are reservoirs that feed metal to compensate for shrinkage as the metal solidifies. Proper design of gates and risers is essential to avoid defects in the final casting.
7. Ventilation Effective ventilation is key to allowing gases to escape during the pouring process. Poor ventilation can lead to defects such as gas porosity, where trapped gas forms bubbles in the cast component, compromising its integrity.
Conclusion
Understanding the components of sand casting is essential for engineers and manufacturers aiming to produce high-quality castings. Each element, from the pattern to the molten metal, plays a vital role in shaping the final product. By optimizing these components, manufacturers can enhance efficiency, reduce costs, and improve the overall quality of their cast products, making sand casting a favored method in a variety of industries, including automotive, aerospace, and machinery. As technology advances, innovations in sand casting processes and materials continue to evolve, further expanding its application and efficiency.
Post time:сеп . 22, 2024 08:24
Next:parts of sand casting