Introduction to Sand Casting Components
Sand casting, also known as sand mold casting, is one of the oldest and most versatile manufacturing processes used to create metal components. This method involves pouring molten metal into a sand mold, where it solidifies and takes the shape of the desired part. Due to its cost-effectiveness and ability to produce complex shapes, sand casting is widely used in various industries, including automotive, aerospace, and general manufacturing.
Components of Sand Casting
1. Pattern The pattern is a replica of the final product and is often made from materials like wood, metal, or plastic. Patterns are designed slightly larger than the final component to account for the shrinkage of metal as it cools. The shape and complexity of the pattern significantly influence the mold and, consequently, the quality of the final product.
2. Mold The mold is created by packing sand around the pattern. The sand used is generally a mixture of silica, clay, and water, which gives it the required binding properties. The mold must have sufficient strength and permeability to allow gases to escape without compromising the mold's integrity. There are two types of molds two-part molds (cope and drag) and one-part molds, depending on the complexity of the shape.
sand casting components
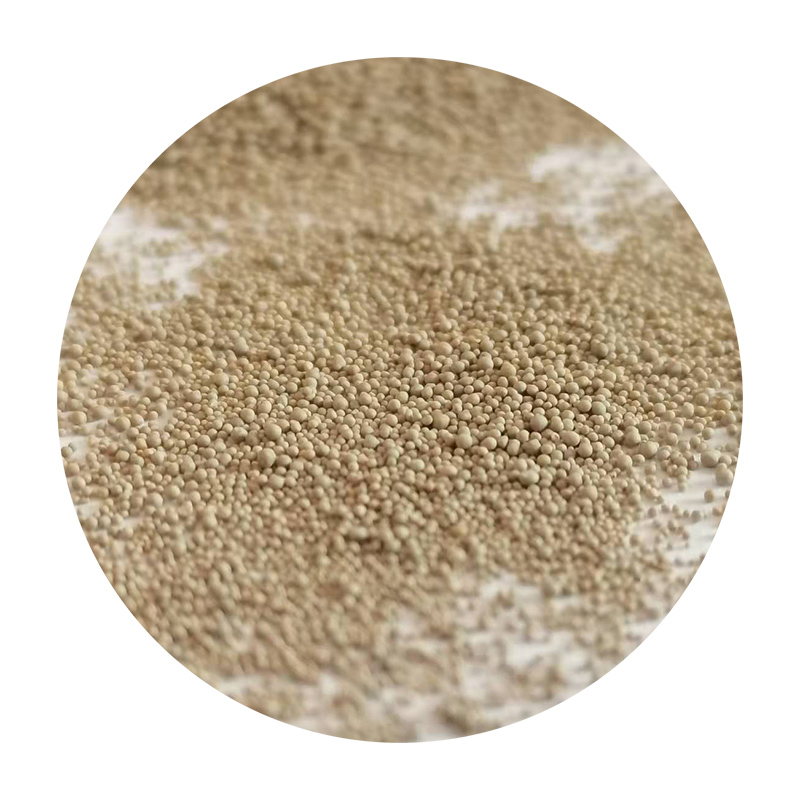
3. Core Cores are additional components used to create internal features or cavities in the casting. They are often made from sand mixtures and placed inside the mold before pouring the metal. Cores can be intricate, allowing for more complex designs and enhancing the functionality of the final part.
4. Melting Furnace The melting furnace is essential for heating the metal to its melting point. Varying types of furnaces, such as induction, electric arc, or cupola furnaces, can be used depending on the metal being cast. The choice of furnace impacts the quality of the molten metal and the overall efficiency of the casting process.
5. Pouring Equipment Once the metal is melted, it needs to be poured into the mold. Pouring ladles or automated pouring systems are typically used to ensure a consistent and controlled flow. Adequate pouring techniques are crucial to prevent defects such as inclusions or air pockets in the final product.
Conclusion
Sand casting is a fundamental technique in manufacturing, and understanding its components is essential for anyone involved in the industry. From the patterns and molds to the furnaces and pouring equipment, each element plays a critical role in the successful production of high-quality metal components. With advancements in technology, the sand casting process continues to evolve, offering even more potential for innovation and efficiency in metal production.
Post time:окт . 22, 2024 11:58
Next:Enhanced Performance Ceramic Sanding Discs for Superior Surface Finishing and Material Removal