Lost Foam Metal Casting An Innovative Approach to Precision Manufacturing
Lost foam metal casting is a unique and highly effective manufacturing process that has gained significant traction in various industries, including automotive, aerospace, and machinery. This method is prized for its ability to produce complex shapes and intricate details, which are often challenging to achieve with traditional casting techniques. With the increasing demand for lightweight, high-strength components, lost foam casting presents an innovative solution that aligns perfectly with modern engineering needs.
The Lost Foam Process
At the core of the lost foam casting process lies a simple yet ingenious idea creating a foam pattern that is then encased in a sand mold. The journey begins with the fabrication of a polystyrene or phenolic foam pattern, meticulously designed to mirror the final cast piece. This foam pattern is coated with a thin layer of ceramic or refractory material to provide stability during casting. Following this, the foam pattern is placed within a sand mold, which is then compacted to hold its shape.
What sets lost foam casting apart is the subsequent process when molten metal is poured into the mold. The heat from the molten metal causes the foam to vaporize almost instantly, leaving behind a cavity that exactly matches the pattern of the original foam. This vaporization not only eliminates the need for core removal but also reduces the possibility of any defects associated with conventional mold making. The result is a casting that is highly accurate and features excellent surface finish.
Advantages of Lost Foam Casting
Lost foam casting boasts several advantages that contribute to its growing popularity within manufacturing sectors. Firstly, it allows for the production of highly complex shapes without the need for complex tooling. This capability decreases lead times and cuts costs significantly, making it a desirable option for companies aiming to enhance efficiency.
Moreover, the precision of lost foam casting means that it can produce parts that require minimal machining, if any at all. This reduces waste and material costs, contributing to sustainability within manufacturing practices. Additionally, the method accommodates a variety of metals, including aluminum, iron, and various alloys, making it versatile for diverse applications.
Another significant benefit is the ability to achieve excellent surface finishes and fine details. The foam patterns can capture intricate features and allow for smoother contours, thus enhancing the end product’s visual appeal and reducing the need for secondary processing.
lost foam metal casting
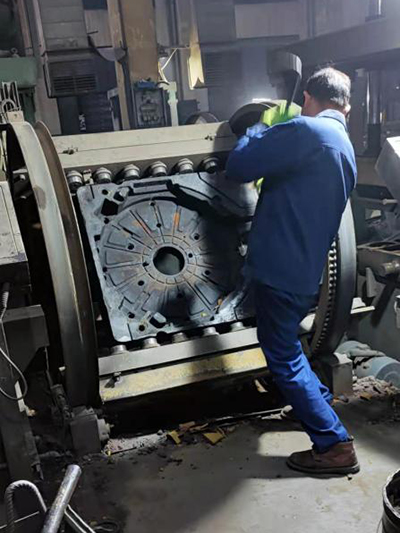
Applications of Lost Foam Casting
Lost foam casting is a preferred technique in several industries due to its benefits. In the automotive sector, it is utilized for producing engine blocks, transmission cases, and other critical components, often sought for their combination of strength and lightweight characteristics. This is particularly important as manufacturers strive to improve fuel efficiency and reduce emissions.
In the aerospace industry, lost foam casting is employed to create intricate components that must meet stringent weight and performance standards. The capability to produce complex geometries allows for innovative designs that were previously impractical with traditional casting methods.
Furthermore, the energy sector is increasingly recognizing the potential of lost foam casting for producing parts in turbines, pumps, and valves—where reliability and precision are paramount.
Challenges and Future Prospects
Despite its many advantages, lost foam casting is not without challenges. One of the main hurdles is the initial investment in the lost foam process and the required technology. Additionally, achieving consistency in foam quality and managing the intricacies involved in pattern design can pose difficulties. However, ongoing advancements in materials science and fabrication technologies are addressing these challenges, making the process more accessible to manufacturers.
Looking ahead, the future of lost foam metal casting appears promising. With the ongoing demand for complex, lightweight, and high-strength components across various sectors, this innovative casting method is likely to grow in importance. As industries continue to shift towards advanced manufacturing techniques, lost foam casting stands as a testament to how creativity and innovation can revolutionize established practices, paving the way for enhancing product performance and sustainability.
Conclusion
In conclusion, lost foam metal casting is transforming the landscape of manufacturing with its ability to produce highly complex components with exceptional precision and surface quality. As industries evolve, the adoption of this innovative process will undoubtedly increase, further solidifying its role in modern manufacturing solutions. The continued exploration and refinement of lost foam casting techniques promise to unlock new opportunities for engineers and manufacturers alike, driving advancements in design and production efficiency.
Post time:нов . 24, 2024 06:27
Next:resin coated silica sand