Lost Foam Casting An Innovative Approach to Metal Fabrication
Lost foam casting is an advanced manufacturing process that has gained recognition for its ability to create intricate metal components with high precision. This technique draws inspiration from traditional sand casting but incorporates unique methods that streamline production and enhance versatility. In this article, we will explore the principles of lost foam casting, its advantages, typical applications, and examples to showcase its effectiveness.
Understanding Lost Foam Casting
At its core, lost foam casting involves the creation of a foam pattern that is coated with a thin layer of sand. Once the sand is prepared, the foam pattern is placed into the mold, and molten metal is poured onto it. As the metal flows, it vaporizes the foam, leaving behind a cavity in the exact shape of the original pattern. This process allows manufacturers to create complex parts without the need for traditional tooling or molds, reducing both time and costs.
Advantages of Lost Foam Casting
1. Complexity and Detail One of the primary benefits of lost foam casting lies in its ability to produce complex geometries that are often difficult or impossible to achieve with conventional casting methods. This includes intricate internal structures, fine details, and undercuts, which can help improve the performance of the final product.
2. Cost-Effective Production The reduction of tooling requirements allows companies to save significantly on production costs. The foam patterns can be produced using inexpensive materials, and the process can be integrated into existing production lines with minimal disruption.
3. Environmental Considerations Lost foam casting is considered more environmentally friendly than traditional methods. The foam used in the pattern is often made from recyclable materials, and the process generates less waste. Additionally, the lack of a need for core boxes and other tooling further reduces environmental impact.
4. Superior Surface Finish The smooth finish of the foam patterns translates into the final castings, often resulting in a reduced requirement for secondary machining operations. This can enhance the aesthetic appearance and surface characteristics of components.
Applications of Lost Foam Casting
Lost foam casting is broadly used in various industries due to its flexibility and precision. Some common applications include
lost foam casting examples
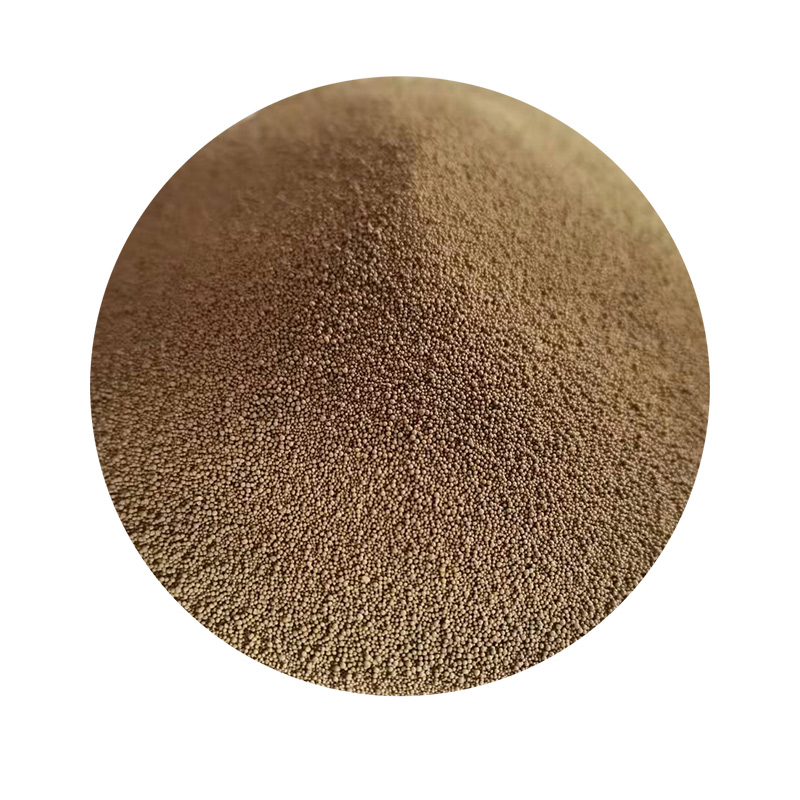
- Automotive Components Manufacturers utilize lost foam casting to produce engine blocks, cylinder heads, and transmission housings
. These components benefit from the technique’s ability to create lightweight, high-strength parts.- Aerospace Industry Complex parts required in aerospace applications, such as turbine housings and brackets, can be effectively manufactured using lost foam casting, owing to its dimensional accuracy and material properties.
- Industrial Equipment Equipment such as pump housings and valve bodies can be fabricated with enhanced performance characteristics, ensuring reliability and longevity.
- Artistic and Architectural Applications Beyond industrial uses, lost foam casting has found a niche in art and architecture where unique designs and sculptures can be realized with remarkable detail.
Examples of Lost Foam Casting in Action
1. Engine Blocks A prominent example can be seen in the production of aluminum engine blocks. The lost foam method allows manufacturers to create lightweight yet durable blocks that meet the rigorous demands of modern vehicles, resulting in improved fuel efficiency and torque.
2. Turbine Components In the energy sector, lost foam casting has been employed to manufacture parts for gas turbines. The ability to produce intricate internal cooling passages helps optimize performance and efficiency in high-temperature environments.
3. Customized Art Pieces Artists have also harnessed the technique to create custom sculptures and installations. By utilizing lost foam casting, they can produce unique pieces that maintain fine details, allowing for creative expression in metalwork.
Conclusion
Lost foam casting has emerged as a transformative technology in the field of metal fabrication, offering numerous advantages from design flexibility to cost savings. Its applications span across various industries, demonstrating its versatility and effectiveness in producing complex geometries. As technology continues to advance, it is likely that lost foam casting will play an increasingly prominent role in manufacturing practices around the globe, pushing the boundaries of what is possible in metal casting.
Post time:дец . 15, 2024 13:08
Next:difference between sand casting and investment casting