Types of Foundry Sands and Their Applications in Metal Casting
Foundry sand plays a pivotal role in the metal casting process, serving as a critical component in the production of mold and core elements. The effectiveness of a foundry is largely determined by the quality and type of sand used, which impacts the final product's dimensional accuracy, surface finish, and mechanical properties. Here, we will delve into different types of foundry sands, their characteristics, and their applications in metal casting.
1. Silica Sand
Silica sand is the most commonly used type of foundry sand due to its availability and desirable properties. Comprising primarily of silicon dioxide (SiO2), silica sand exhibits excellent thermal stability, which allows it to withstand high temperatures during metal casting. It has a fine grain structure that facilitates good mold surface finish and excellent permeability, enabling air to escape during the pouring of molten metal. Silica sand is often used in the casting of iron and non-ferrous metals.
2. Resin-coated Sand
Resin-coated sand combines the benefits of traditional silica sand with the advantages of resin binders, typically phenolic or furan resins. This type of sand is characterized by its strength, superior dimensional accuracy, and the ability to produce highly detailed molds. The resin coating offers excellent mechanical properties and eliminates the need for additional binders in certain applications. Furthermore, resin-coated sand is highly resistant to thermal deformation, making it suitable for both ferrous and non-ferrous metal castings, particularly in high-volume production.
3. Green Sand
Green sand is a mixture of sand, clay, and water, creating a malleable medium that can be formed into molds. The clay acts as a binder, providing cohesion and allowing the sand to retain its shape. Green sand is easy to work with and can be reused after drying, making it cost-effective. It is particularly favored in the casting of iron, aluminum, and bronze, as it allows for effective heat transfer and good surface finish. The moisture content in green sand provides additional benefits, reducing dust and improving mold integrity.
foundry sand types
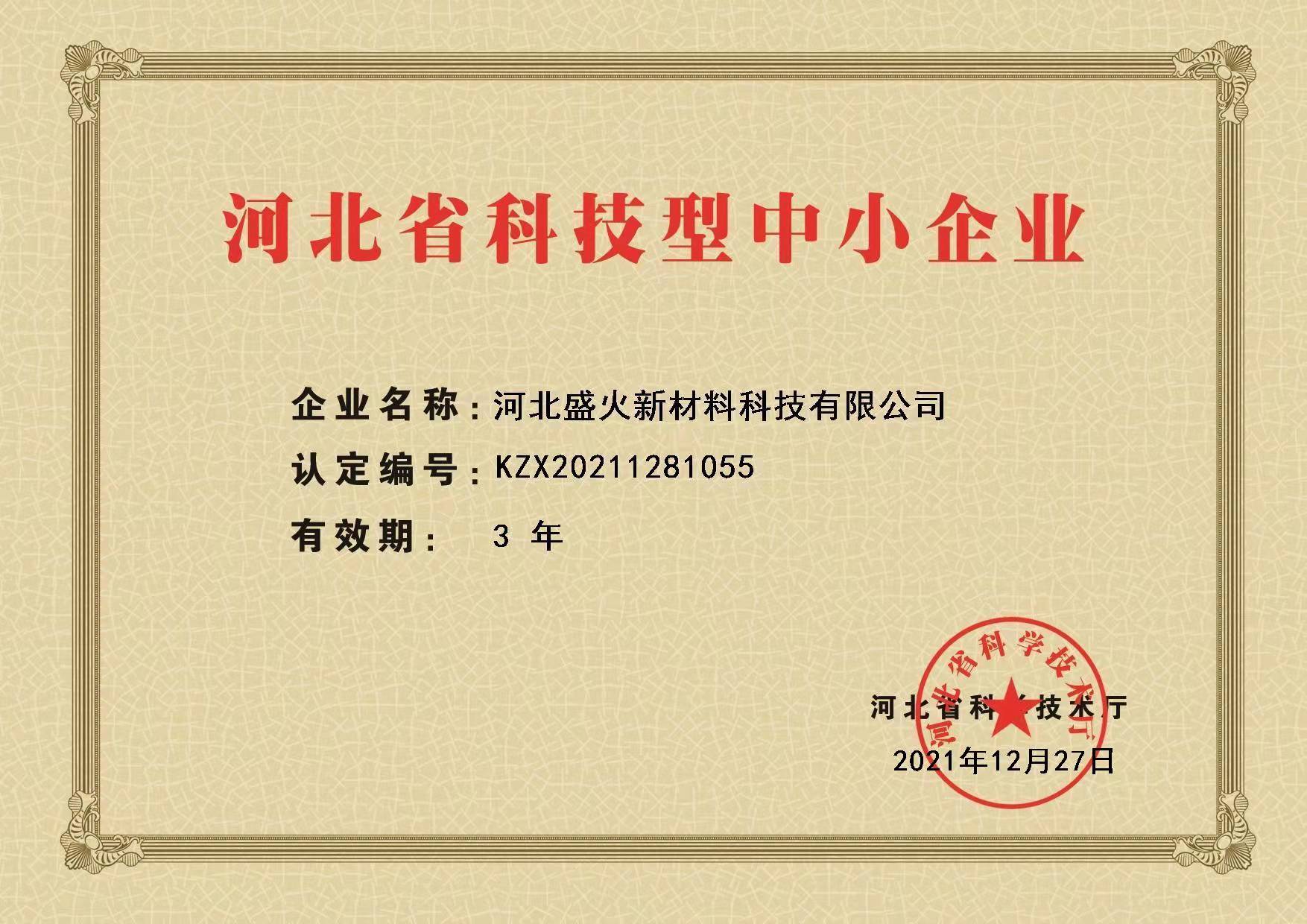
4. Zircon Sand
Zircon sand is a premium foundry sand that offers distinct advantages, particularly in high-temperature applications. Its high melting point and thermal stability make it ideal for casting processes involving steel and non-ferrous metals. Zircon sand minimizes the possibilities of casting defects such as burn-on and scabbing, promoting the production of clean, high-quality castings. However, its higher cost compared to silica sand can limit its widespread adoption, often being reserved for specialized applications requiring superior performance.
5. Chromite Sand
Chromite sand, composed of chromium oxide, is known for its refractory properties and high thermal conductivity. It is often used in the casting of steel and high-alloy components due to its ability to withstand extreme temperatures and reduce the risk of mold distortion. Chromite sand is especially advantageous for producing complex shapes and intricate designs, making it popular in aerospace and automotive industries. Additionally, its non-toxic nature makes it an environmentally friendly alternative to other sands.
6. Coal Dust and Other Additives
In some applications, additives such as coal dust may be mixed with standard foundry sands to enhance certain properties. Coal dust, for instance, can improve the surface finish and reduce shrinkage in molds. This type of innovation allows foundry operators to customize their sand mixtures to meet specific requirements based on the metal being cast and the complexities of the design.
Conclusion
In summary, the choice of foundry sand is crucial for achieving desired casting qualities. Each type of sand—from silica to zircon, and green sand to chromite—offers unique properties and advantages tailored to specific applications. Understanding these types can help foundries optimize their processes, improve casting quality, and ultimately contribute to the production of high-performance metal components. As industries evolve, the exploration of new sand types and innovative mixtures will continue to shape the future of metal casting.
Post time:нов . 30, 2024 03:00
Next:Key Distinctions Between Sand Casting and Die Casting Methods Explained