Differences Between Sand Casting and Permanent Mold Casting
Casting is a pivotal manufacturing process, used extensively to create complex metal parts. Among various casting methods, sand casting and permanent mold casting stand out due to their unique characteristics and applications. Understanding the differences between these two methods is crucial for selecting the appropriate process for a given project.
1. Materials Used Sand casting utilizes a mixture of sand, clay, and water to form molds. The sand used is typically silica sand, which can withstand high temperatures. In contrast, permanent mold casting employs reusable metal molds, usually made from iron, steel, or aluminum. These molds can endure multiple cycles, making them ideal for high-volume production.
2. Production Volume One of the most significant differences lies in the volume of production that each method is suited for. Sand casting is highly flexible and cost-effective for small to medium production runs. It allows for quick changes and can accommodate intricate designs. On the other hand, permanent mold casting is better suited for larger production runs. The initial investment in metal molds can be high, but they are cost-effective over time due to their reusability.
difference between sand casting and permanent mold casting
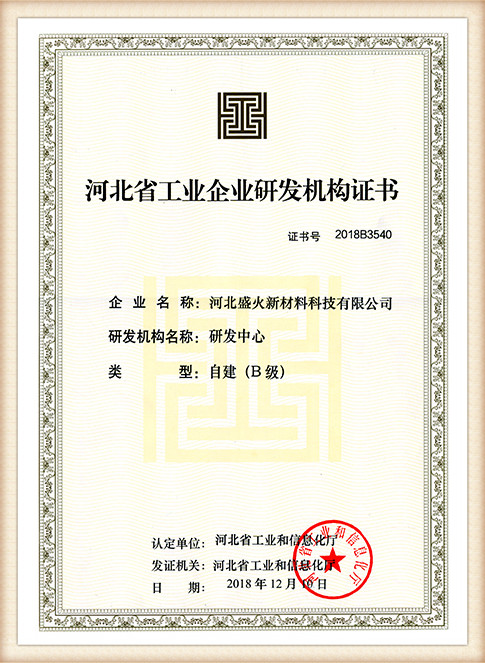
3. Surface Finish and Accuracy Permanent mold casting generally results in superior surface finishes and dimensional accuracy compared to sand casting. The metal molds in permanent mold casting provide a smoother surface, which reduces the need for extensive post-processing. Sand casting, while versatile, often requires additional finishing processes to achieve desired surface quality, as it can produce a rougher finish and less precise dimensions.
4. Heat Treatment and Strength When comparing the mechanical properties of the final products, castings made from permanent molds often exhibit higher strength and better mechanical properties due to the rapid cooling and solidification process that occurs in metal molds. This results in fine-grained structures. Conversely, sand-cast products may have a coarser grain structure, which can affect mechanical performance.
5. Applications Sand casting is widely used in industries that produce complex, large, or heavy parts, such as automotive and aerospace, where flexibility in design is essential. Permanent mold casting is preferred for high-volume production of simpler designs, such as automotive parts and household items, where consistency and high quality are paramount.
Conclusion In summary, the choice between sand casting and permanent mold casting largely depends on the specific requirements of the project, including production volume, complexity of design, surface finish, and mechanical properties. Each method has its inherent advantages and is suitable for different applications, making it essential for engineers and manufacturers to understand these differences when deciding on the best casting process for their needs.
Post time:нов . 05, 2024 05:44
Next:using sand in resin