Advantages of Lost Foam Casting A Comprehensive Overview
Lost foam casting (LFC) is a revolutionary metal casting process that has gained traction in various industries due to its unique advantages over traditional casting methods. This technique involves creating a foam pattern of the desired object, which is subsequently coated with a sand mixture and then subjected to molten metal. As the metal is poured into the mold, the foam evaporates, leaving behind a near-net-shape casting. Here, we will explore the numerous advantages of lost foam casting, highlighting why many manufacturers are adopting this innovative approach.
One of the foremost advantages of lost foam casting is its ability to produce complex shapes with intricate details. Traditional casting methods often require multiple steps and additional tooling to achieve complex geometries, which can be both time-consuming and expensive. In contrast, the lost foam method allows for the creation of complex contours without the need for machining or additional processes. This not only speeds up production but also reduces material waste, making it a more efficient option for manufacturers.
Another significant benefit of lost foam casting is its capability to achieve excellent surface finishes. The smooth surface of the foam pattern translates directly into the final casting, often eliminating the need for extensive finishing work. This leads to a reduction in post-processing time and costs, making it an attractive option for industries where surface quality is paramount, such as automotive and aerospace. By minimizing the need for additional machining, lost foam casting enhances overall productivity.
The process also excels in flexibility when it comes to materials. Lost foam casting can be employed with a range of metals, including aluminum, bronze, and iron, allowing manufacturers to select the best material for their specific application. This versatility makes lost foam casting suitable for both small and large scale productions, catering to diverse industries such as manufacturing, construction, and consumer goods.
advantages of lost foam casting
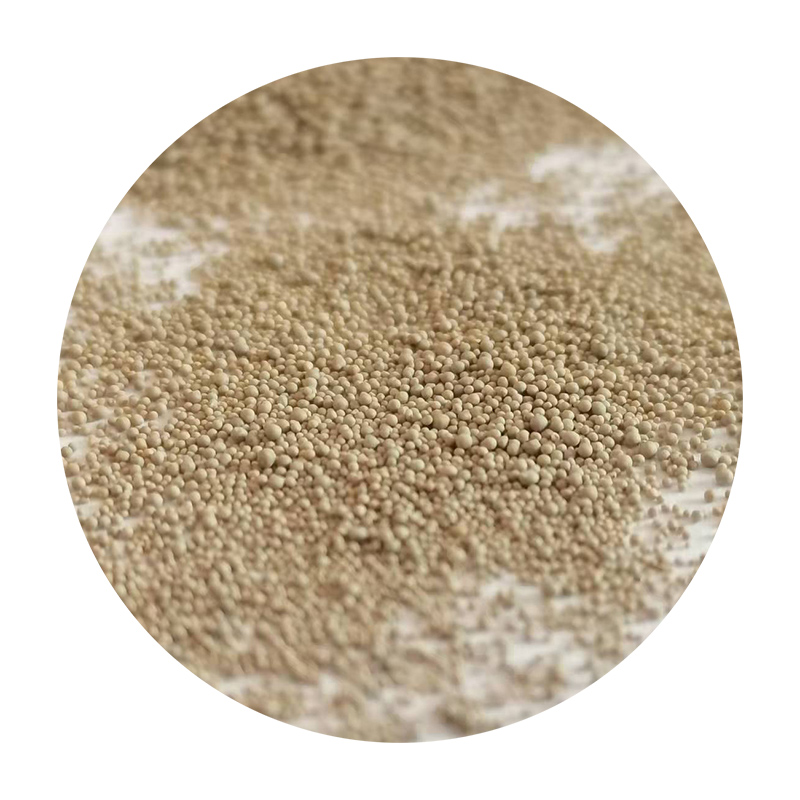
Cost efficiency is another major advantage of lost foam casting. The elimination of traditional mold-making processes reduces both time and labor costs significantly. Additionally, the ability to use less material—thanks to near-net-shape production—can lead to substantial savings. These cost efficiencies contribute to a lower overall production cost, making lost foam casting a compelling choice for businesses aiming to maximize profit margins.
Lost foam casting is also recognized for its environmental benefits. The process generates less waste compared to conventional casting methods, as the foam pattern is used entirely without leaving behind scraps. Furthermore, the reduction in energy consumption during production, combined with the ability to recycle materials, positions this casting method as an environmentally friendly option. This aspect aligns with the increasing industry shift towards sustainable practices, appealing to eco-conscious companies and consumers alike.
Moreover, the speed of the lost foam casting process greatly enhances production capabilities. The method allows for rapid prototyping and quick turnaround times, which are essential for industries where speed to market is critical. The ability to produce multiple castings in quick succession further enhances efficiency, catering to the fast-paced demands of modern manufacturing environments.
Finally, lost foam casting supports innovation in product design. Engineers and designers are encouraged to create more daring and complex designs without the fear of prohibitive costs typically associated with traditional casting. This freedom fosters creativity and can lead to the development of groundbreaking products that push the boundaries of what is possible.
In conclusion, lost foam casting presents a multitude of advantages that position it as a leading choice for metal casting. From producing intricate shapes and superior surface finishes to achieving cost efficiency and environmental sustainability, this innovative method is transforming the casting landscape. As industries continue to seek advanced manufacturing solutions, lost foam casting is set to play an increasingly vital role in shaping the future of production.
Post time:дец . 31, 2024 10:45
Next:Where to Purchase Quality Foundry Sand for Your Casting Needs