3D Sand Casting Revolutionizing the Foundry Industry
In recent years, traditional manufacturing techniques have faced an existential challenge as industries strive for efficiency, precision, and sustainability. One such technique that has gained significant traction is 3D sand casting, a transformative approach that blends traditional foundry practices with modern technology. This innovative method not only streamlines the production process but also enhances design capabilities and reduces waste.
What is 3D Sand Casting? 3D sand casting is a manufacturing technique that utilizes 3D printing technology to create molds for metal casting. In the traditional sand casting process, molds are constructed by hand, requiring significant time and labor. In contrast, 3D sand casting employs a 3D printer to produce sand molds directly from digital designs. This method allows for the rapid production of complex geometries that would be challenging, if not impossible, to achieve through conventional methods.
3D Sand Casting Revolutionizing the Foundry Industry
Additionally, 3D sand casting results in reduced lead times. Traditional sand mold production can take days or even weeks, depending on the complexity of the design. With 3D sand casting, molds can be printed in a matter of hours, significantly accelerating the time from concept to production. This speed is crucial in today’s fast-paced manufacturing environment, where time-to-market can determine the success of a product.
3d sand casting
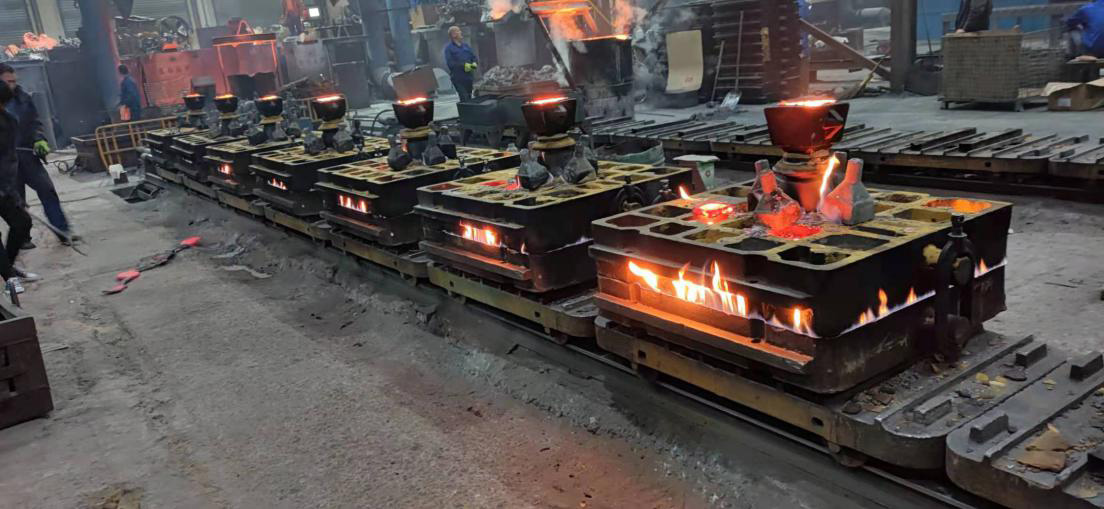
Moreover, sustainability is a growing concern in manufacturing, and 3D sand casting contributes positively in this regard. Traditional sand casting generates a considerable amount of waste material, as old molds must often be discarded after use. However, with 3D sand casting, the sand used in the molds can be reused after the casting is complete, leading to a reduction in overall material waste. Furthermore, the precision of 3D sand casting minimizes the need for extensive post-processing, further conserving resources.
Applications of 3D Sand Casting The applications of 3D sand casting are vast and varied. In the automotive industry, for instance, complex engine components and customized parts can be produced efficiently, allowing for lightweight designs that enhance fuel efficiency. The aerospace sector benefits from 3D sand casting by producing intricate parts that comply with stringent safety standards, all while reducing weight and improving performance.
Additionally, 3D sand casting is making waves in the world of art and sculpture. Artists and designers are exploring the possibilities of creating unique, custom pieces that push the boundaries of traditional casting techniques. This fusion of art and technology showcases the versatility of 3D sand casting, allowing for an unprecedented level of creativity.
Conclusion As the manufacturing landscape continues to evolve, 3D sand casting emerges as a significant player in the foundry industry. Combining the best of traditional techniques with cutting-edge technology, it offers unparalleled design flexibility, reduced lead times, and sustainability benefits. With its expanding range of applications, 3D sand casting is not just a trend; it represents a paradigm shift in how we approach manufacturing.
In conclusion, as industries seek innovative solutions to meet modern demands, 3D sand casting stands at the forefront, paving the way for the future of metal casting. Its ability to adapt and innovate will undoubtedly leave an indelible mark on the manufacturing industry, shaping the products and technologies of tomorrow.
Post time:окт . 02, 2024 02:10
Next:Golden Sands Progress Shaping a Vibrant Future for Coastal Development and Community Growth