The Synergy of 3D Printing and Sand Casting Revolutionizing Manufacturing
In recent years, the world of manufacturing has experienced a seismic shift in practices and technologies, with one of the most significant changes being the introduction of 3D printing. Among its many applications, the intersection of 3D printing and sand casting has emerged as a particularly noteworthy advancement. This synergy not only enhances the efficiency and precision of traditional sand casting but also opens new avenues for innovation in design and production.
Understanding Sand Casting
Sand casting is one of the oldest manufacturing processes, dating back thousands of years. It involves creating a mold by packing sand around a pattern that reflects the shape of the desired part. Once the mold is formed, molten metal is poured into it, and after cooling, the mold is removed to reveal the final product. This method is particularly favored for its versatility in producing complex geometries and large parts.
Despite its advantages, traditional sand casting has its limitations, including lengthy lead times, labor-intensive processes, and difficulties in achieving intricate designs. This is where 3D printing comes into play, providing solutions that address these challenges.
The Role of 3D Printing in Sand Casting
The integration of 3D printing into the sand casting process primarily revolves around the creation of patterns and molds. Instead of carving patterns out of wood or metal, manufacturers can use 3D printing to produce highly accurate and complex patterns directly from digital designs. This results in several benefits
1. Reduced Lead Time 3D printing significantly cuts down the time needed to create patterns. Traditional methods can take days or even weeks, whereas 3D printed patterns can be completed in a matter of hours. This rapid prototyping accelerates the overall production process.
2. Enhanced Design Flexibility The complexity that 3D printing offers allows engineers to design intricate patterns that may be too complex or costly to achieve with traditional methods. This opens up opportunities for innovation, enabling the production of lightweight structures and optimized geometries that enhance performance.
3d printing sand casting
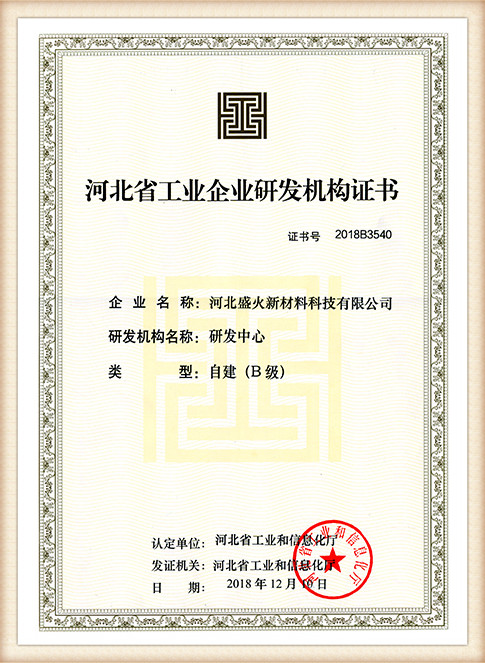
3. Cost Efficiency While the initial investment in 3D printing technology can be high, the long-term savings are substantial. Reduced material waste and decreased labor costs contribute to overall cost efficiency, especially in short production runs or highly customized parts.
4. Improved Accuracy and Consistency 3D printing provides a higher level of precision in pattern creation, resulting in more consistent mold quality. This directly translates to improved dimensional accuracy in the final cast parts, reducing the need for post-processing.
Applications in Various Industries
The combination of 3D printing and sand casting is especially beneficial across various industries such as automotive, aerospace, and industrial machinery. In the automotive sector, manufacturers are able to produce lightweight components that enhance fuel efficiency and performance. Aerospace companies utilize this technology to fabricate complex components with strict weight and strength requirements, all the while minimizing the risk of defects.
Moreover, the ability to rapidly prototype and test new designs leads to more innovative products hitting the market faster. Customization is also a significant advantage; manufacturers can respond to market demands with tailored solutions without incurring prohibitive costs.
Future Trends
Looking forward, the continued evolution of materials for 3D printing—such as ceramics and metal composites—will further enhance the capabilities of this combined manufacturing method. As technology progresses, the possibilities for greater integration between 3D printing and traditional techniques like sand casting will likely expand. Research into sustainable materials and processes will also play a crucial role in shaping the future of manufacturing, aligning with global trends towards sustainability and eco-friendliness.
Conclusion
The integration of 3D printing technology with sand casting is paving the way for a new era in manufacturing. This powerful combination not only streamlines the production process but also fosters innovation and customization, enabling industries to meet the ever-increasing demands of the market. As both technologies continue to evolve, their synergy will undoubtedly contribute to more efficient, precise, and sustainable manufacturing practices, transforming the way we design and produce parts into the future.
Post time:окт . 19, 2024 11:17
Next:Can You Smooth Resin Surfaces Effectively with Sanding Techniques?