Why Sand Casting is Preferred An In-depth Analysis
When it comes to manufacturing metal parts, various methods are available, each with its unique advantages and drawbacks. Among these techniques, sand casting stands out as one of the most widely used and preferred methods across various industries. This article explores the reasons why sand casting is favored, highlighting its cost-effectiveness, versatility, ease of use, and ability to produce complex shapes.
Cost-Effectiveness
One of the most compelling reasons why sand casting is preferred is its cost-effectiveness. The materials used in sand casting, primarily sand and metal, are relatively inexpensive compared to other casting methods. The sand can be reused multiple times, which further decreases material costs. Additionally, the initial set-up costs for sand casting are generally lower because it requires less specialized equipment and tooling compared to methods like die casting or investment casting. This makes sand casting an attractive option for both small-scale operations and large industrial manufacturers, particularly in applications where large volumes of parts are not required.
Versatility in Material Use
Another significant advantage of sand casting is the versatility in the types of materials that can be utilized. Sand casting can accommodate a wide range of metals, including aluminum, iron, and bronze, making it suitable for various applications across industries such as automotive, aerospace, and construction. This adaptability means that manufacturers can choose the most appropriate metal for their specific needs without worrying about compatibility constraints inherent in other casting methods.
Complex Shapes and Designs
Sand casting is particularly effective in producing complex shapes and intricate designs. The sand molds, which are made by compacting sand around a pattern, can easily create detailed features, including undercuts and thin walls. This capability allows engineers and designers to push the boundaries of creativity and functionality in their designs. Unlike other methods that may have strict limitations on the complexity of shapes, sand casting provides the freedom to explore innovative designs without the risk of production issues.
why sand casting is preferred
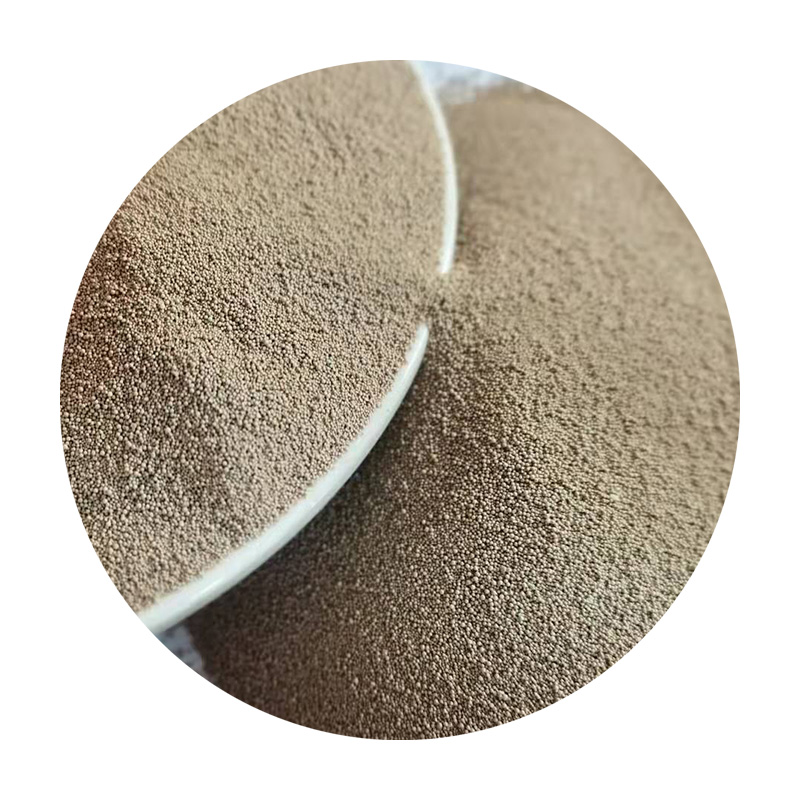
Ease of Use
The sand casting process is straightforward and user-friendly, making it accessible to a wide range of manufacturers. The procedure involves creating a mold from a pattern, pouring molten metal into the mold, and allowing it to solidify before removing the casting. This simplicity means that even smaller workshops can adopt sand casting without needing extensive training or specialized skills. Moreover, the process is relatively quick, enabling shorter lead times from design to production compared to other casting methods.
Tolerance and Finish
While sand casting may not always achieve the tight tolerances and surface finish quality of processes like investment casting, advancements in technology have significantly improved the outcomes. Modern sand casting techniques, including the use of resin-bonded sand and advances in mold design, have enhanced the precision and surface quality of cast parts. For many applications, the tolerances achievable with sand casting are sufficient, making it a practical choice for a broad spectrum of components.
Environmental Considerations
Lastly, sand casting is often seen as more environmentally friendly compared to other casting techniques. The primary material, sand, is abundant and can be recycled repeatedly with minimal waste. Additionally, the energy required to produce sand castings is typically less than that for other methods, contributing to a lower carbon footprint for manufacturers.
Conclusion
Sand casting has established itself as a preferred method for metal casting due to its cost-effectiveness, material versatility, capability for complex designs, ease of use, tolerances, and environmental benefits. As industries continue to evolve and demand for specialized components grows, sand casting remains a powerful and reliable technique that meets a diverse range of manufacturing needs. Whether for prototype development or high-volume production, sand casting offers a compelling solution that continues to stand the test of time.
Post time:Tet . 22, 2024 03:59
Next:heath ceramics sand