The Type of Sand Used for Sand Casting
Sand casting is one of the oldest and most versatile methods of metal casting, widely utilized in manufacturing processes to create complex shapes and components. Central to this technique is the type of sand used, which plays a critical role in determining the quality and characteristics of the final product. The most commonly used sand in sand casting is silica sand, but there are several other types that can be employed depending on the specific requirements of the casting process.
Silica Sand
Silica sand, composed predominantly of silicon dioxide (SiO2), is the primary choice for sand casting. Its high melting point and excellent thermal properties make it ideal for withstanding the intense heat generated during the casting process. Silica sand grains are typically angular and have a high degree of permeability, which allows gases to escape during pouring, reducing the risk of defects in the final cast.
Green Sand
Another popular option is green sand, which is a mixture of silica sand, clay, water, and various additives. The clay content serves to bind the sand grains together, creating a mold that retains its shape during the casting process. Green sand molds can be easily packed and shaped, making them suitable for a wide range of applications. This type of sand is especially favored in large-scale foundries due to its reusability.
what type of sand is used for sand casting
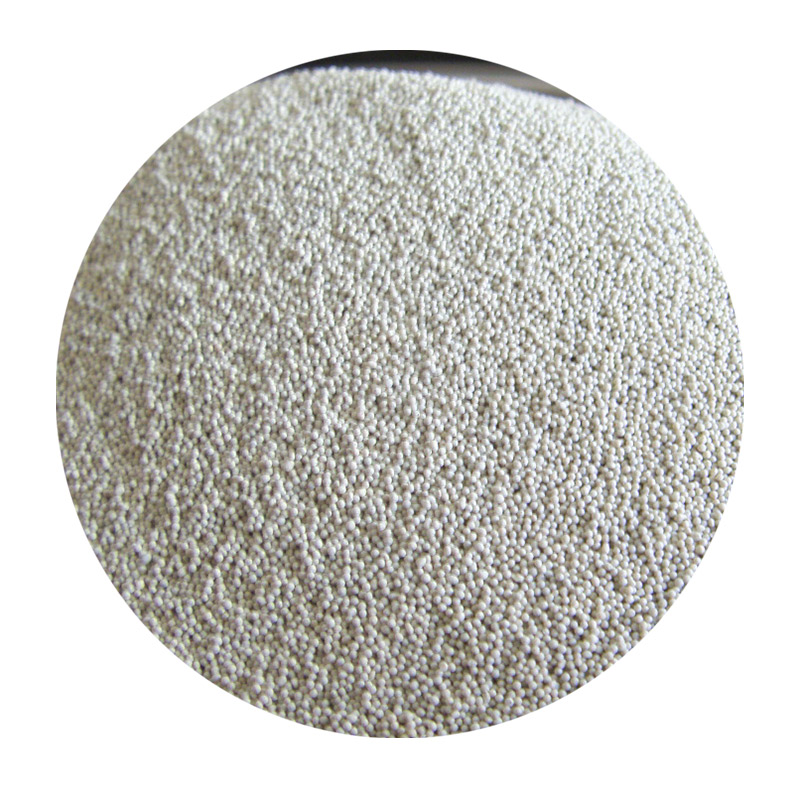
Resin-Sand
Resin-sand is a modern alternative to traditional molding sands and is often used when a higher degree of precision and finer details are required in castings. This mixture combines silica sand with a resin binder that hardens upon heating. The use of resin allows for more intricate designs and smoother surface finishes, making it a choice for industries that demand high-quality components.
Miscellaneous Sands
In addition to silica and green sands, there are other specialty sands that may be used for specific applications. For instance, zircon sand offers excellent thermal stability and is often used in applications where high resistance to thermal shock is essential. Similarly, chromite sand is utilized for its ability to withstand higher temperatures, making it suitable for casting ferrous metals.
Conclusion
In conclusion, the choice of sand for sand casting is pivotal in influencing the quality, detail, and overall success of the cast product. While silica sand and green sand are the most commonly used types, various other sands may be chosen based on specific casting requirements. Understanding the properties and applications of these sands allows manufacturers to optimize their production processes and achieve superior casting results.
Post time:Tet . 10, 2024 04:21
Next:Innovative Techniques in Lost Foam Casting for Enhanced Metal Fabrication and Design Efficiency