What is Sand Casting in Engineering?
Sand casting, also known as sand mold casting, is a metal casting process characterized by the use of sand as the primary mold material. This method is one of the oldest and most widely used casting techniques in the manufacturing industry, mainly due to its versatility, cost-effectiveness, and ability to create complex shapes. In this article, we delve into the intricacies of sand casting, its processes, advantages, limitations, and applications in engineering.
The Process of Sand Casting
The sand casting process involves several critical steps pattern making, mold preparation, pouring, cooling, and finishing.
1. Pattern Making The first step in sand casting is the creation of a pattern, which is a replica of the item to be cast. Patterns can be made from various materials, including wood, metal, or plastic, and are designed to be slightly larger than the final product to account for material shrinkage during cooling.
2. Mold Preparation Once the pattern is ready, it is used to create a mold in a mixture of sand and a binding agent, often clay. The pattern is pressed into the sand mixture to form a cavity that mirrors the shape of the pattern. The mold consists of two halves (the cope and the drag) that are assembled together.
3. Pouring After the mold is prepared, the metal to be cast—typically aluminum, iron, or steel—is melted and poured into the mold through a pouring basin or sprue. The molten metal fills the cavity and takes on the shape of the pattern.
4. Cooling Following pouring, the metal needs time to cool and solidify. The cooling time varies based on the size and type of metal. Once the metal has completely cooled and solidified, the mold can be dismantled.
5. Finishing After removal from the mold, the casting may require machining, grinding, or other finishing processes to achieve the desired surface finish and dimensional accuracy.
Advantages of Sand Casting
what is sand casting in engineering
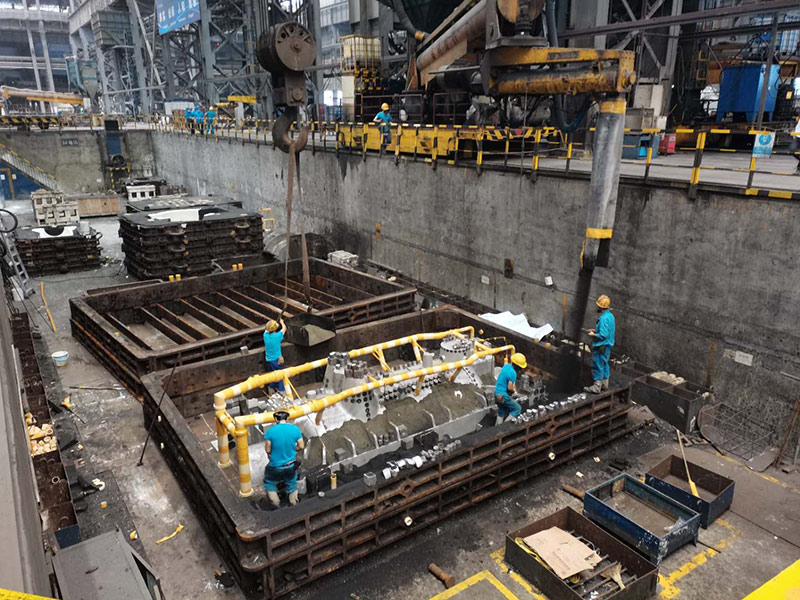
Sand casting offers numerous benefits, making it a popular choice in engineering applications
- Versatility Sand casting can accommodate a variety of metals, including ferrous and non-ferrous alloys, enabling its use in diverse industries. - Cost-Effective The materials used, mainly sand, are relatively inexpensive. Additionally, the process allows for the casting of both small and large quantities, making it economical for different scales of production. - Complex Shapes Sand casting is particularly adept at creating intricate designs and geometries that would be challenging to achieve with other casting methods. - Size Range This method can produce components ranging from very small to extremely large sizes, accommodating a wide spectrum of engineering requirements.
Limitations of Sand Casting
Despite its many advantages, sand casting also has its drawbacks
- Surface Finish Castings produced through sand casting typically have a rough surface finish compared to investment casting or die casting. Additional machining can be necessary to achieve smoother surfaces. - Dimensional Tolerance The dimensional tolerances in sand casting are generally less precise than those obtainable through other casting methods, which may necessitate additional machining or adjustments in some applications. - Labor-Intensive The process can be labor-intensive, particularly in the pattern-making and mold preparation stages, which can increase lead times.
Applications of Sand Casting
Sand casting is widely utilized across various fields, including automotive, aerospace, heavy machinery, and general manufacturing. Common applications range from engine blocks, transmission cases, and pump housings to intricate components used in turbines and valves. The method’s adaptability to both small runs and mass production makes it essential in meeting the demands of different engineering projects.
Conclusion
In summary, sand casting is a fundamental yet highly effective metal casting process in engineering, celebrated for its ability to produce complex shapes at a reasonable cost. While it has some limitations in terms of surface finish and tolerance, its advantages make it a preferred choice for many applications in various industries. By understanding the intricacies of sand casting, engineers can leverage its capabilities to create high-quality metal parts that meet rigorous design and performance standards.
Post time:Dhj . 16, 2024 03:11
Next:Innovative Applications of Spherical Sand in Modern Industries and Environmental Solutions