Types of Sand in Foundry
In the foundry industry, sand is an essential material used in the casting process to create molds. The choice of sand can significantly influence the quality of the final product, making it imperative for foundry professionals to carefully select the right type for their specific applications. This article delves into the various types of sand used in foundries, their properties, and their applications.
1. Silica Sand
Silica sand, primarily composed of silicon dioxide (SiO2), is the most commonly used sand in foundries. Its excellent thermal stability and ability to withstand high temperatures make it ideal for metal casting. Silica sand provides a good surface finish and minimizes the occurrence of defects like mold cracking. Its availability and low cost further contribute to its popularity in foundries. However, the fine particulates in silica sand can pose respiratory hazards, necessitating appropriate safety measures for workers.
2. Resin-Coated Sand
Resin-coated sand is a mixture of silica sand and a thermosetting resin binder. This type of sand allows for a higher degree of precision in mold production, leading to better surface finishes and dimensional accuracy. When heated, the resin bonds the sand grains together, creating a strong mold with excellent strength and durability. Resin-coated sand is often employed in specialty applications where high casting quality is required, such as in the aerospace and automotive industries. However, it comes with a higher cost compared to natural sand, which may limit its usage in larger foundries.
3. Green Sand
Green sand is a mixture of sand, clay, water, and moisture, and is one of the most traditional materials used in casting processes. The clay binds the sand grains together while the water helps with the molding process. Green sand is easy to work with, cost-effective, and capable of producing intricate designs with good surface finishes. It is particularly favored for ferrous metal casting due to its ability to retain heat. Despite its advantages, green sand molds can occasionally lead to defects like permeability issues, which may affect the final casting quality.
types of sand in foundry
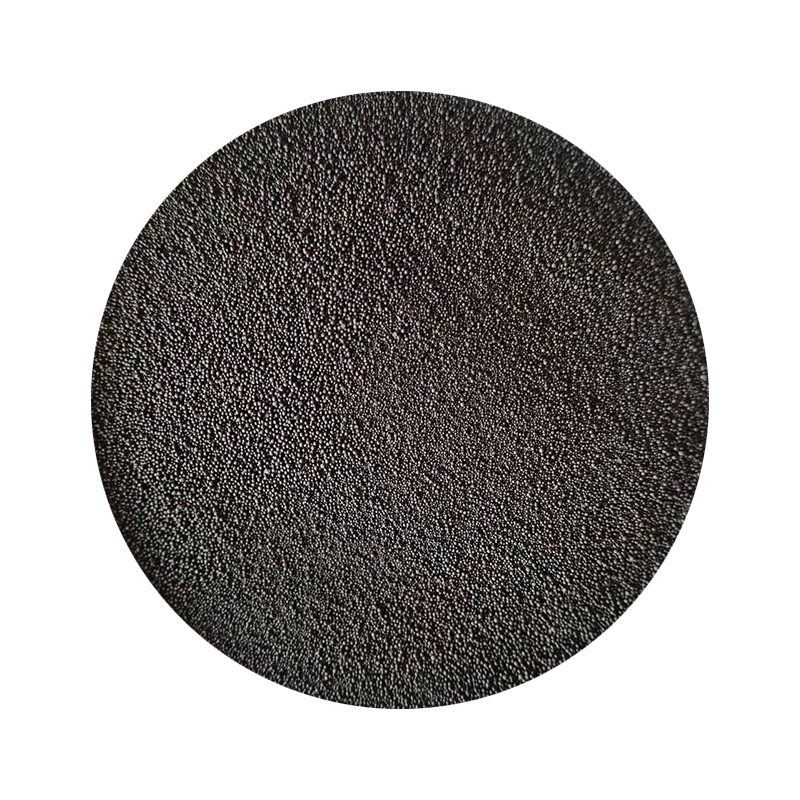
4. Dry Sand
Unlike green sand, dry sand is a mixture of sand and a binding agent (such as resin) without water. Dry sand molds are created using cores and patterns, offering a more stable and rigid mold structure. This type of sand is less prone to mold swelling, which can be beneficial when producing high-precision parts. Dry sand can also withstand higher temperatures, making it suitable for casting metals like aluminum and copper. However, the processing and handling of dry sand can be more challenging than traditional green sand.
5. No-Bake Sand
No-bake sand, or chemically bonded sand, is a mixture of sand and a chemical binder that hardens at room temperature. It eliminates the need for water in the mixture, leading to fewer environmental concerns and greater dimensional stability in the final casting. No-bake sand provides excellent detail reproduction and surface finish quality, making it ideal for complex shapes and intricate designs. While it offers many benefits, the chemical binders can be more expensive and may require specialized handling procedures.
6. Lost Foam Sand
Lost foam sand is a unique molding method that involves the use of a foam pattern, which is surrounded by sand. When molten metal is poured into the mold, it vaporizes the foam pattern, allowing the metal to take its shape. This type of sand is advantageous for creating complex geometries and eliminating the need for draft angles and tapered patterns typically required in traditional sand casting methods. However, the process can be more expensive and requires precise control over temperature and timing.
Conclusion
The selection of sand in foundry processes plays a crucial role in determining the quality and efficiency of metal casting. Whether it's silica sand for its widespread usability or resin-coated sand for high-precision applications, each type of sand offers unique properties that cater to specific needs in the foundry industry. By understanding these differences, foundry professionals can make informed decisions that optimize their casting processes, enhance product quality, and improve overall operational efficiency. As technological advancements continue to evolve, the exploration of new sand types will remain pivotal in shaping the future of metal casting.
Post time:Nën . 15, 2024 12:36
Next:บริษัท หล่อทราย