Steps of Sand Casting A Comprehensive Guide
Sand casting is one of the oldest and most versatile metal casting processes used to create a wide variety of metal parts and components. This method utilizes sand as the primary mold material due to its ability to withstand high temperatures and its unique properties that allow for detailed shaping. Below, we will delve into the fundamental steps of the sand casting process, providing insights into the essential techniques and considerations involved.
Step 1 Designing the Patterns
The sand casting process begins with the creation of a pattern. A pattern is a replica of the final product and usually crafted from materials such as metal, wood, or plastic. The design must account for factors such as shrinkage, draft angles, and any necessary allowances to ensure that the final casting accurately reflects the intended dimensions. This step is crucial as the quality of the pattern directly influences the quality of the final cast product.
Step 2 Preparing the Mold
Once the pattern is ready, the next step involves preparing the mold. This is typically done by mixing sand with a binder, which may be clay or a chemical agent, to create a moldable mixture. The mixture is then compressed around the pattern to form a mold cavity. Two halves of the mold are often created, known as the cope (top half) and the drag (bottom half). The pattern is removed after the sand has been compacted, leaving a negative impression of the desired shape.
Step 3 Making the Core
For complex shapes, cores may be required to create internal cavities in the cast piece. Cores are usually made from sand mixed with binders, similar to the molds, but often have different characteristics to achieve specific results. They are placed in the mold before the metal is poured in, allowing for intricate designs that cannot be formed with the mold alone.
Step 4 Melting the Metal
The next crucial step is melting the metal that will be poured into the mold. Typically, metals like aluminum, brass, and iron are used in sand casting. The metal is melted in a furnace, achieving temperatures high enough to liquefy the material. The molten metal must be handled with extreme care due to its high temperatures and potential hazards. Once melted, the molten metal is usually poured into a ladle, ready for transfer to the mold.
steps of sand casting
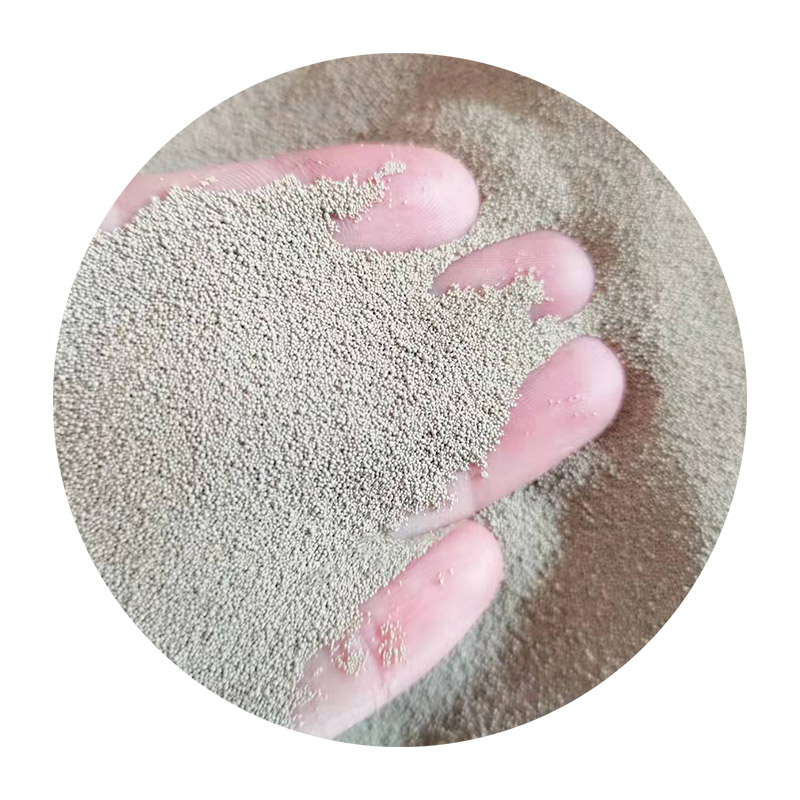
Step 5 Pouring the Metal
After the mold and core preparation, the molten metal is carefully poured into the mold cavity. This step requires precision as any mistakes can lead to defects such as air pockets, misfillings, or unwanted inclusions. The pouring rate and temperature must be controlled to ensure that the mold is completely filled without creating turbulence that could affect the mold structure.
Step 6 Cooling
Once the mold is filled, the metal is left to cool and solidify. The cooling time can vary depending on the thickness of the casting and the type of metal used. During this phase, the metal undergoes a transformation from liquid to solid, and it is critical to avoid rapid cooling, which can lead to internal stresses and cracks.
Step 7 Removing the Casting
After sufficient cooling, the mold is carefully broken apart to remove the cast piece. This process, known as shakeout, can entail various methods, including mechanical shaking or manual breaking. At this stage, it is also common to remove any cores that were used in the casting process.
Step 8 Finishing the Casting
The final step in the sand casting process involves cleaning and finishing the casting. This includes processes such as sand blasting, grinding, and machining to achieve the desired surface finish and dimensional accuracy. Additionally, removing any excess material, known as gates and risers, is necessary to ensure the final product meets specifications.
Conclusion
Sand casting is a highly effective method for producing intricate and durable metal components. Each step of the process, from pattern design to finishing, plays a significant role in determining the quality of the final product. By following these steps diligently, manufacturers can ensure the production of reliable and high-quality castings suitable for various applications across multiple industries.
Post time:Nën . 19, 2024 16:25
Next:High-Quality Metal Casting Sand Available for Purchase Online