A Comprehensive Guide to Sand Casting Sand Types
Sand casting is a widely used manufacturing process that involves pouring molten metal into a sand mold to create various components. The quality of the final product heavily relies on the type of sand used in the casting process. Understanding the various sand types can help manufacturers choose the best fit for their specific needs. This article explores the most common sand types used in sand casting and their unique properties.
1. Green Sand
Green sand is a mixture of silica sand, clay, and water. It is the most commonly used type of sand in sand casting. The green refers to the moisture content, not the color. Green sand molds are prepared by mixing the sand and clay with water to achieve a uniform consistency. This type of sand allows for excellent mold strength and collapsibility, making it easy to remove castings once they have cooled. Additionally, green sand is cost-effective and can be reused multiple times, which makes it a popular choice in foundries.
2. Dry Sand
As the name suggests, dry sand is not mixed with water and has a lower moisture content than green sand. It is typically used for large castings where fine detail and surface finish are paramount. Dry sand molds provide better surface detail because they can maintain their shape more rigidly than moist sands. However, dry sand is generally more challenging to handle, and the molds need to be coated with a release agent to prevent the metal from sticking.
3. No-Bake Sand
sand casting sand types
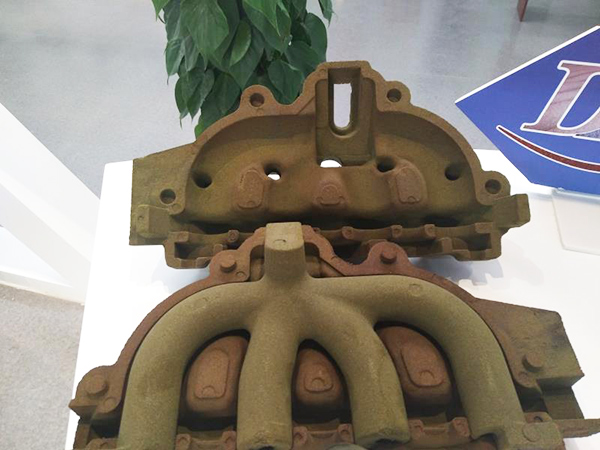
No-bake sand (or chemically bonded sand) is a mixture of sand and a chemical binder that hardens at room temperature. This sand type is particularly advantageous for creating intricate designs and high-precision castings. The no-bake process offers superior dimensional accuracy and a smoother surface finish. However, it often comes at a higher cost and requires more handling due to its chemical components.
4. Silica Sand
Silica sand is one of the most commonly used sands in the casting industry. It has a high melting point and excellent thermal stability, making it suitable for casting high-temperature metals. Silica sand is characterized by its fine grain size, which aids in producing detailed molds with excellent surface finishes. However, it's important to ensure that the silica content is high to prevent the sand from breaking down during the casting process.
5. Chrome Sand
Chrome sand is a type of high-quality sand that contains chromite. It boasts excellent thermal properties, making it effective for casting ferrous and non-ferrous alloys. Chrome sand is particularly valued for its ability to withstand high temperatures without deforming. This makes it ideal for heavy-duty applications, such as large engine blocks or heat-resistant components.
Conclusion
Selecting the right type of sand for sand casting is crucial for achieving optimal results in the manufacturing process. Each sand type offers distinct advantages and is suited for different applications. By understanding the properties and characteristics of green sand, dry sand, no-bake sand, silica sand, and chrome sand, manufacturers can make informed decisions that enhance the quality and efficiency of their casting operations. Whether seeking to produce high-precision components or reliable heavy-duty parts, the choice of sand will play a significant role in the success of any casting project.
Post time:Tet . 30, 2024 14:46
Next:foundry sand suppliers