Understanding the Sand Casting Manufacturing Process
Sand casting is one of the oldest and most widely used metal casting processes in manufacturing. It utilizes the versatility of sand as a mold material to create complex shapes and components for various industrial applications. This article provides an overview of the sand casting process, its advantages, limitations, and key considerations.
The fundamental principle of sand casting involves creating a mold from a mixture of sand and a binding agent. The process begins with pattern making, where a model of the desired object (the pattern) is created, usually from metal, plastic, or wood. The pattern is then placed in a molding box, and sand is packed around it to create a mold. The sand mixture is typically composed of silica sand, clay, and water, which provide the necessary strength and cohesiveness.
Once the sand has been packed tightly around the pattern, the mold is removed from the box, and the pattern is extracted, leaving a hollow cavity that replicates the shape of the object to be cast. An important step involves creating a gating system, which allows the molten metal to flow into the mold and air to escape. The mold halves are then reassembled, and the gating system is securely attached.
With the mold prepared, the next phase is melting the metal. Common materials used in sand casting include aluminum, iron, bronze, and magnesium. The metal is heated until it reaches a liquid state and is then poured into the mold through the gating system. The temperature and pouring technique must be carefully controlled to minimize defects such as porosity or oxidation.
sand casting manufacturing process
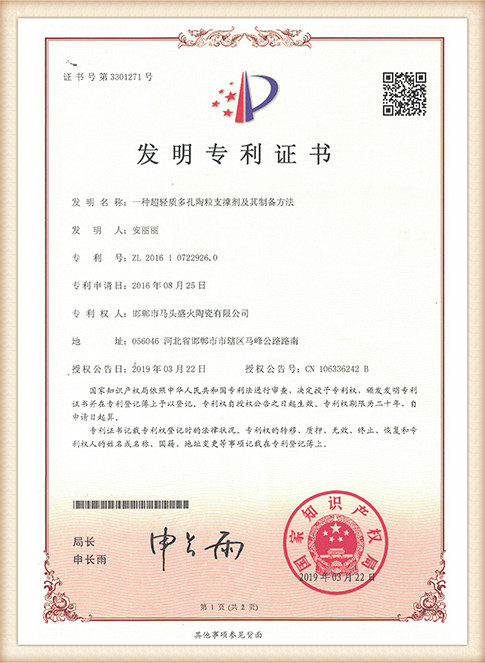
After the metal has cooled and solidified, the casting is removed from the mold. This process, known as shakeout, involves breaking the sand mold, which can be a labor-intensive step since sand molds are typically not reusable. The cast piece is then cleaned and inspected for any imperfections. Subsequent processes such as machining or surface finishing may be required to achieve the final specifications.
The advantages of sand casting are numerous. It can accommodate large parts, intricate designs, and a wide variety of metals. The flexibility of sand casting also makes it cost-effective for both short-run productions and high-volume applications. Additionally, the use of sand as a mold material is economical and readily available.
However, sand casting does come with its limitations. The surface finish of the cast components is generally rough, often requiring additional machining to obtain the desired quality. Furthermore, the dimensional accuracy can vary, so precise tolerances may not be achievable without post-processing. Additionally, the process can be time-consuming, particularly for large or complex parts.
In conclusion, sand casting remains a cornerstone of metal manufacturing due to its adaptability and efficiency. By understanding the intricacies of the sand casting process, manufacturers can leverage its strengths while mitigating its weaknesses, paving the way for innovative product development and optimized production techniques. Whether for prototypes or mass production, sand casting continues to play a vital role in the evolution of manufacturing processes.
Post time:Tet . 31, 2024 08:49
Next:how to sand ceramic