Understanding Sand Casting for Iron
Sand casting is one of the oldest and most widely used manufacturing processes in the metalworking industry. It involves pouring molten metal into a mold made from sand to create various components with complex shapes. In the realm of iron casting, this process offers distinct advantages that make it an ideal choice for producing a myriad of iron products, from intricate sculptures to heavy machinery parts.
The Sand Casting Process
The sand casting process begins with creating a mold. A pattern, usually made of a material like metal or plastic, is shaped to the desired dimensions of the final product and coated with a release agent to prevent the sand from sticking. The mold itself is typically made from a mixture of sand and a binder, which helps the sand grains stick together. The patterns are pressed or packed into the sand to create a cavity in the mold. After this, the pattern is removed, leaving a hollow shape that will determine the final product’s design.
Once the mold is prepared, molten iron is poured into the cavity of the mold. The temperature of molten iron typically exceeds 1,500 degrees Celsius, making careful handling essential. As the iron fills the mold, it cools and solidifies over time. The cooling process can vary, affecting the mechanical properties of the iron, such as its strength and brittleness. After the iron has cooled sufficiently, the sand mold is broken away to reveal the finished cast iron component.
Advantages of Sand Casting Iron
One of the primary advantages of sand casting iron is its versatility. This technique accommodates a wide range of iron alloys, including gray iron, ductile iron, and white iron, each having unique characteristics that are suitable for different applications. For instance, ductile iron offers excellent tensile strength and ductility, making it ideal for automotive parts and construction equipment.
sand casting iron
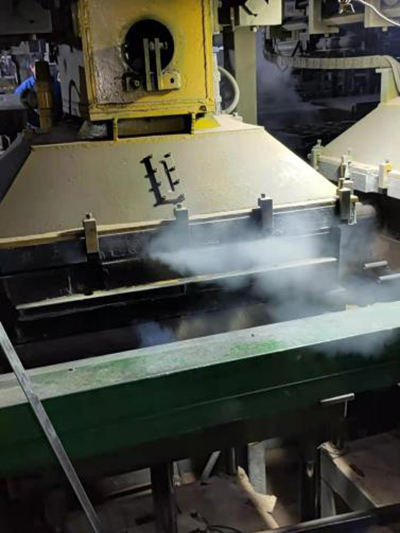
Another significant advantage is the cost-effectiveness of sand casting. The materials used, primarily sand and binders, are inexpensive compared to other types of molds, such as those made from metal or ceramic. Furthermore, the sand mold can be reused multiple times, which reduces production costs over long runs.
The sand casting process is also relatively simple, allowing for the rapid production of complex shapes. It is especially beneficial for low to medium production volumes where traditional methods, like die casting, might not be economically feasible.
The Application of Sand Cast Iron
Sand casting plays a crucial role in numerous industries. In the automotive sector, it is used to create engine blocks, cylinder heads, and other structural components that require durability and performance. The construction industry benefits from sand cast iron products such as pipes, fittings, and manhole covers, which are essential for urban infrastructure. Additionally, decorative items, art pieces, and sculptures can be produced with remarkable detail using sand casting techniques.
Conclusion
In conclusion, sand casting iron remains a vital process in modern manufacturing due to its versatility, economic viability, and ability to produce complex designs. The continued advancement in technology and materials will likely enhance its capabilities and applications in the future. As industries strive for efficiency and cost-effectiveness, sand casting will undoubtedly remain a cornerstone technique in the world of metalworking, enabling the production of high-quality iron components tailored to meet the specific needs of various markets.
Post time:Dhj . 25, 2024 14:15
Next:Advancements in Sand Casting Technology for Modern Manufacturing Processes and Applications