Sand Casting The Foundation of Quality Manufacturing
Sand casting, one of the oldest and most versatile manufacturing processes, has played an integral role in the evolution of various industries. From automotive parts to intricate industrial components, the art of sand casting enables the production of intricate designs in a cost-effective and efficient manner. Companies specializing in sand casting have harnessed this age-old technique, combining traditional practices with modern technology to meet the growing demands of today's market.
The Sand Casting Process
The process of sand casting begins with creating a pattern, usually made from wood, metal, or plastic, which is a replica of the final product. This pattern is critical as it determines the final shape and dimensions of the casting. Once the pattern is ready, it is placed in a molding box, and a mixture of sand and binder is packed around it to form the mold. The sand used in this process is typically a fine-grade silica sand, which provides excellent strength and replication of detail.
After molding, the pattern is removed, leaving a cavity that matches the desired shape of the finished part. The next step involves pouring molten metal into this cavity. Crucially, the quality of the molten metal affects the final product's integrity, necessitating careful selection of materials. Once the metal cools and solidifies, the sand mold is broken away, revealing the cast part.
Advantages of Sand Casting
One of the primary advantages of sand casting is its adaptability. The process can accommodate a wide range of metals, including aluminum, iron, bronze, and steel, making it suitable for an array of applications. Furthermore, sand casting can produce both large and small parts, from hefty engine blocks to delicate artistic sculptures.
Another significant benefit is the low cost associated with creating sand molds. Unlike other casting techniques such as die casting, which require expensive metal molds, sand molds can be made quickly and at a fraction of the cost. This cost efficiency is particularly beneficial for short production runs or prototype manufacturing.
sand casting company
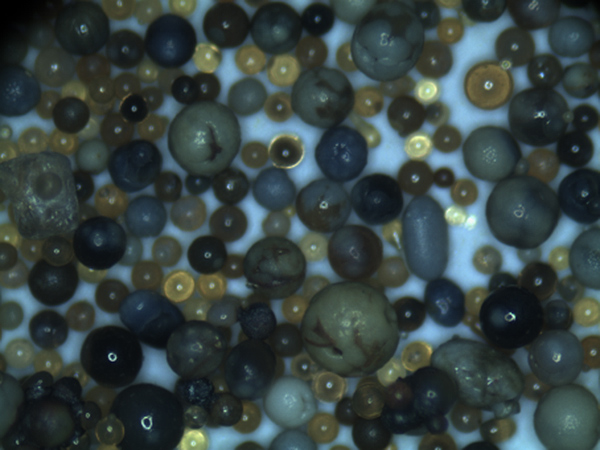
Sand casting also offers remarkable versatility in design. The use of sand allows for greater freedom in creating complex shapes and intricate details. It is not uncommon for sand-cast parts to exhibit features that would be challenging to achieve with alternative manufacturing processes. This flexibility makes sand casting an attractive option for companies aiming to innovate and diversify their product offerings.
Innovations and Technology
As industries evolve, so do the techniques used in sand casting. Advances in technology have allowed companies to enhance the casting process significantly. Computer-aided design (CAD) and simulation software are now commonly employed to optimize mold design and predict casting outcomes. This technological integration helps manufacturers identify potential defects and refine their processes before physical production begins.
Moreover, the introduction of automation and robotics has revolutionized sand casting operations. Automated systems can streamline the molding process, reduce labor costs, and increase production rates while maintaining high levels of precision. These innovations contribute to improved consistency in product quality and enhanced operational efficiency.
Environmental Considerations
Modern sand casting companies are also increasingly focusing on sustainability. The sand used in the process is often recyclable, and advancements in pollution control technologies have minimized the environmental impact of foundries. Companies are actively seeking ways to reduce waste and emissions, reflecting a growing commitment to environmentally responsible practices.
Conclusion
In conclusion, sand casting remains a cornerstone of manufacturing due to its flexibility, cost-effectiveness, and ability to produce complex designs. As companies continue to innovate and embrace new technologies, the sand casting process is poised to meet the needs of a rapidly changing market. Whether producing small prototype parts or large-scale industrial components, sand casting companies play a vital role in enabling manufacturers to bring their ideas to life, ensuring that this traditional technique remains relevant in the modern world.
Post time:Dhj . 15, 2024 11:18
Next:sand cast metal