Sand Casting 101 An Introduction to the Foundry Process
Sand casting, one of the oldest and most widely used manufacturing processes in the world, is a robust method for producing metal parts. This versatile technique has emerged as a favored choice for metalworking due to its cost-effectiveness, adaptability, and ability to create complex geometries. In this article, we will delve into the fundamentals of sand casting, exploring its process, materials, applications, and advantages.
Understanding the Sand Casting Process
At its core, sand casting involves creating a mold from sand, into which molten metal is poured to create a desired part. The process can be broken down into several key steps
1. Pattern Creation The first step of sand casting involves creating a pattern, which is a replica of the final product. This pattern is usually made of metal, plastic or wood and is designed slightly larger than the finished part, accounting for shrinkage that occurs during cooling.
2. Mold Making Once the pattern is ready, it is pressed into a sand mixture to form a mold. The sand used in this process is typically a silica-based material that is mixed with a binding agent to help it retain shape. The pattern is removed, leaving a cavity that reflects the shape of the object to be cast.
3. Melting and Pouring The next step involves melting the required metal, which often varies depending on the application—common metals include aluminum, iron, and bronze. Once the metal reaches a suitable temperature, it is carefully poured into the mold cavity.
4. Cooling After pouring, the molten metal cools and solidifies within the mold. Cooling times can vary based on the size of the part and the metal used.
5. Mold Removal Once the metal is solidified, the sand mold is broken away to reveal the cast object. This step may involve shaking, hammering, or other methods to ensure the mold is completely removed.
6. Finishing The last step often includes various finishing processes to enhance the surface quality and achieve the desired tolerances. This can involve grinding, machining, or polishing.
Materials Used in Sand Casting
The primary material used in sand casting is the sand itself. High-quality molding sand consists of grainy silica, which provides the mold with strength while allowing for the necessary flexibility to remove the final cast part. In addition, various binders, such as clay or resin, are added to ensure the sand holds its shape during the casting process.
sand casting 101
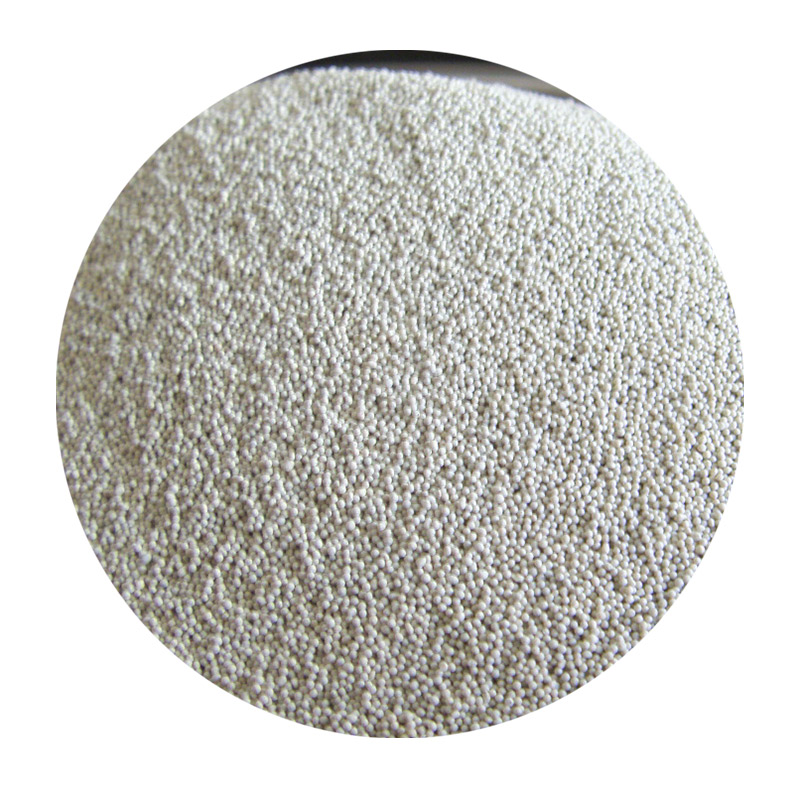
The choice of metal is crucial too; different metals have different properties that make them suitable for particular applications. Aluminum is lightweight and corrosion-resistant; cast iron offers good wear resistance; while steel provides strength and durability.
Applications of Sand Casting
The versatility of sand casting allows it to be employed across a wide range of industries
. Common applications include- Automotive Industry Many engine components, housings, and brackets are manufactured using sand casting due to its ability to produce complex shapes at a lower cost. - Aerospace Sand casting is used for making parts that require high strength-to-weight ratios, including brackets and housings.
- Marine Applications Sand casting can produce components exposed to harsh marine environments, such as propellers and hull fittings.
- Art and Sculpture Many artists and sculptors use sand casting to create intricate designs and forms, showcasing the method's aesthetic potential.
Advantages of Sand Casting
Sand casting offers numerous advantages, making it a popular choice among manufacturers
- Cost-Effective The process requires low initial investment and is ideal for both small and large production runs. - Flexibility Sand molds can be easily modified or adapted to create different shapes and sizes. - Complex Shapes The method can produce intricate designs that would be challenging to achieve with other manufacturing techniques.
- Material Variety A wide range of metal materials can be satisfactorily cast using this method.
In conclusion, sand casting remains a fundamental manufacturing process, widely used for its adaptability and efficiency. As industries continue to innovate and the need for customized components grows, sand casting is likely to maintain its critical role in the foundry world. Understanding this age-old technique paves the way for advancements and innovations in the art of metal casting.
Post time:Dhj . 15, 2024 18:35
Next:Understanding the Definition and Importance of Foundry Sand in Casting Processes