Sand Casting 101 An Overview of a Time-Honored Metalworking Technique
Sand casting is one of the oldest and most widely used metalworking techniques in manufacturing. Dating back to ancient times, this versatile method is valued for its ability to produce complex shapes in a variety of metals with relative ease. This article provides an overview of sand casting, exploring its processes, advantages, applications, and considerations.
What is Sand Casting?
At its core, sand casting involves creating a mold from a mixture of sand, clay, and water to shape molten metal into a desired form. The mold is created by packing sand around a pattern that replicates the object to be cast. Once the mold is prepared and the pattern removed, molten metal is poured into the cavity to create the final product. After the metal cools and solidifies, the mold is broken open to retrieve the casting.
The Sand Casting Process
The sand casting process can be broken down into several key steps
1. Pattern Making The first step involves creating a pattern that represents the final product. This pattern is often made from materials such as wood, metal, or plastic and is slightly larger than the final piece to account for metal shrinkage as it cools.
2. Mold Preparation The pattern is then placed in a flask, which is a container for the sand mold. Fine sand mixed with a binding agent (usually clay) and water is packed around the pattern to create the mold. The sand mixture must be tightly packed to ensure the mold maintains its shape when the pattern is removed.
3. Melting and Pouring Once the mold is prepared and the pattern has been removed, the next step is to melt the metal. This is typically done in a furnace. The molten metal is carefully poured into the mold through a designated pouring basin.
4. Cooling After the metal is poured, it needs time to cool and solidify. The cooling time varies depending on the size and type of metal used. During this stage, the casting takes on the shape of the mold.
5. Finishing Once cooled, the mold is broken open to remove the casting. Additional finishing processes, such as grinding or machining, may be required to achieve the final specifications and surface finish of the casting.
Advantages of Sand Casting
Sand casting offers several advantages that contribute to its widespread use in various industries
- Versatility It is suitable for a wide range of metals, including aluminum, iron, and bronze. Sand casting can accommodate different alloy compositions and can produce both small and large parts.
sand casting 101
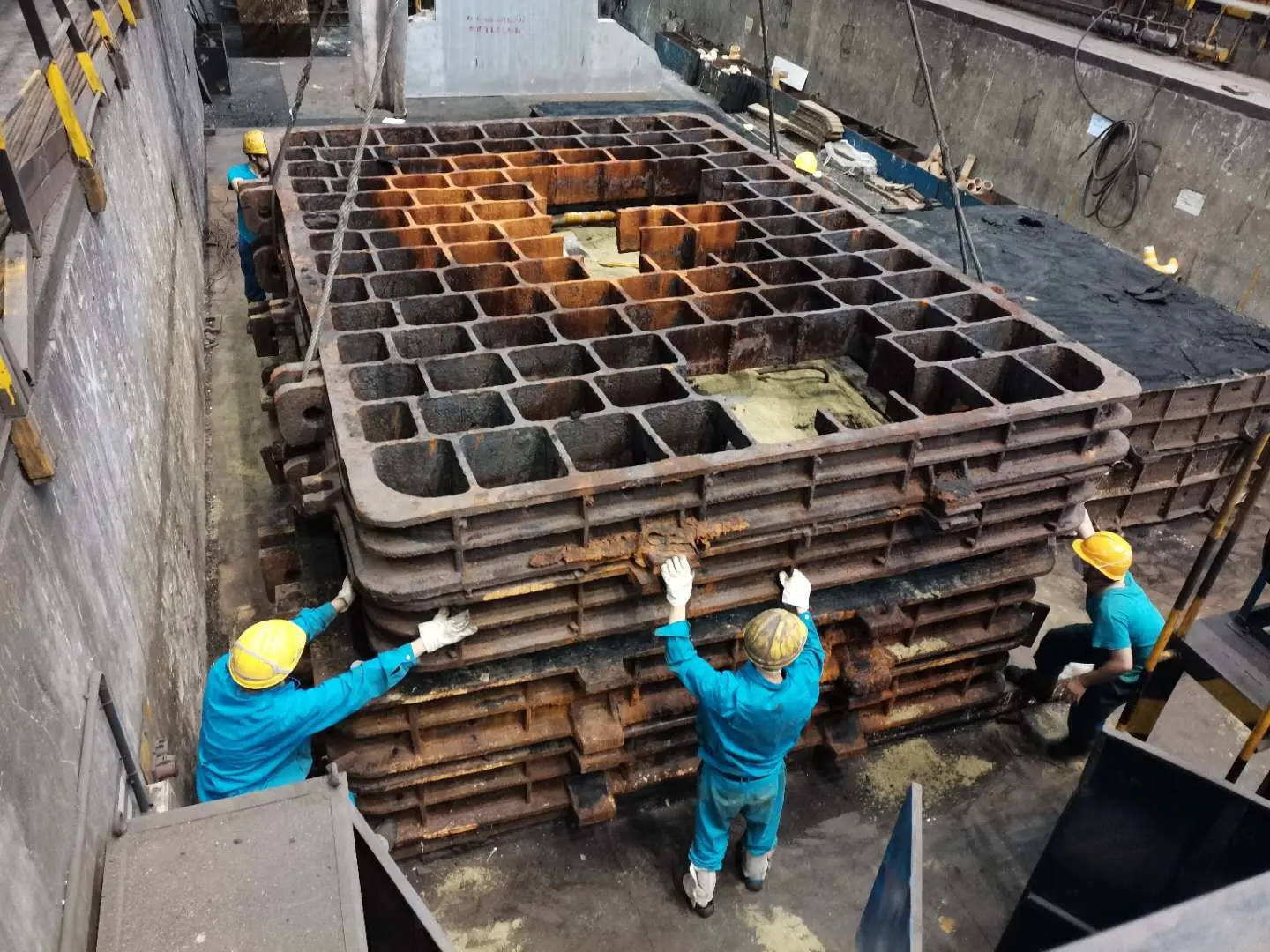
- Cost-Effective Compared to other casting methods, sand casting is relatively inexpensive. The materials used for mold-making, primarily sand and clay, are abundant and affordable.
- Complex Shapes The sand mold can easily form intricate designs and details that would be difficult to achieve with other manufacturing processes.
- Low Production Costs For low-to-medium volume production, sand casting does not require the costly tooling often necessary for high-volume manufacturing methods.
Applications of Sand Casting
The applications of sand casting are vast and diverse. It is commonly used in various industries, including
- Automotive Many automotive components, such as engine blocks and transmission housings, are produced using sand casting.
- Aerospace Sand casting is employed to create lightweight yet strong components critical for aerospace applications.
- Art and Sculpture Artists often utilize sand casting to create unique sculptures and art pieces in metal.
- Industrial Equipment Machinery parts such as gears and valves are frequently made using this casting technique.
Considerations and Challenges
While sand casting has many benefits, it is not without its challenges. The process can introduce defects, such as sand inclusions or poor surface finishes, which may require additional rework. Additionally, the eventual mechanical properties of the cast part may not always meet the specifications required for highly stressed applications.
Conclusion
In conclusion, sand casting remains an essential method of metalworking, providing a balance of flexibility, cost-effectiveness, and the ability to create complex geometries. As technology progresses, advancements in molding materials and processes are likely to enhance the capabilities of sand casting, ensuring its relevance in modern manufacturing. Whether for industrial applications or artisanal endeavors, the fundamental principles of sand casting continue to shape the world of metal production, bridging the gap between ancient techniques and contemporary needs.
Post time:Nën . 30, 2024 05:23
Next:Achieving a Smooth Finish with Wet Sanding Techniques for Resin Projects