The Importance of Molding Sand in Metal Casting
Molding sand plays a crucial role in the metal casting process, which is a manufacturing technique that involves pouring molten metal into a mold to create specific shapes and forms. This process is integral to various industries, from automotive to aerospace, due to its ability to produce complex geometries with high precision. The choice of molding sand can significantly affect the quality of the final product, making it essential to understand its properties and types.
Types of Molding Sand
There are several different types of molding sand, each with unique characteristics suitable for various applications. The most commonly used types are
1. Green Sand This is a mixture of silica sand, clay, and water. It is termed green because it is used in its natural, moist state. Green sand is favored for its excellent mold-making capabilities and its ability to retain moisture, which is crucial for achieving fine details in the casting.
2. Dry Sand Unlike green sand, dry sand is a mixture of silica sand and a binding agent, usually resin or a similar synthetic additive. This type of sand is used when higher strength and a more durable mold are required, making it suitable for large and complex castings.
3. Shell Mold Sand This sand is used to create shell molds, which are formed by heating a mixture of sand and thermosetting resin. Shell molds provide superior surface finishes and dimensional accuracy, making them ideal for high-precision applications.
4. Investment Sand This type of sand is used for making investment casts, commonly employed in jewelry and intricate components. The process involves coating a pattern in fine sand, which is then heated to create a mold cavity.
molding sand for metal casting
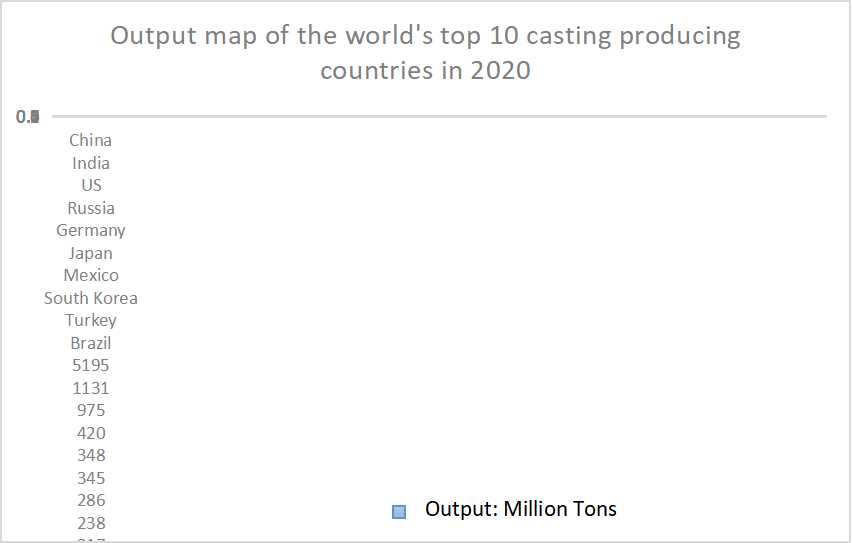
Properties of Molding Sand
When selecting molding sand, several properties must be taken into account to ensure optimal casting results
- Permeability This refers to the ability of the sand to allow gases to escape during the casting process. Good permeability prevents gas entrapment, which can lead to defects in the final product.
- Strength The strength of the molding sand is essential in maintaining the integrity of the mold during metal pouring. It must withstand the weight and temperature of the molten metal without collapsing or deforming.
- Reusability Many molding sands can be reused multiple times, making them cost-effective and environmentally friendly. The ability to recycle sand reduces raw material costs and waste.
- Thermal Stability The sand must possess the ability to withstand high temperatures without breaking down or altering its properties. This is critical, as the molten metal can exceed temperatures of 1,500 degrees Celsius (2,732 degrees Fahrenheit).
Conclusion
In summary, molding sand is an indispensable element of the metal casting process, with various types and properties that cater to different casting needs. The right selection of molding sand can enhance mold performance and improve the quality of the final products, leading to higher customer satisfaction and lower production costs. As industries increasingly demand precision and efficiency, ongoing research into advanced molding sand formulations and additives is likely to continue, driving innovations in casting technologies. Understanding and properly utilizing molding sand is, therefore, essential for manufacturers looking to optimize their production processes and deliver high-quality metal castings.
Post time:Nën . 08, 2024 02:22
Next:Golden Shores Exploring the Beauty of Sun-Kissed Beaches and Serene Landscapes