Materials Used for Sand Casting
Sand casting, also known as sand mold casting, is one of the most widely used manufacturing processes for metal parts. It is particularly favored for its versatility, cost-effectiveness, and ability to produce intricate shapes. The materials utilized in sand casting play a critical role in determining the quality and performance of the final product. This article explores the various materials involved in sand casting, highlighting their functions and significance.
1. Sand
The primary material in sand casting is, unsurprisingly, sand. Silica sand is the most common type used, due to its excellent properties, such as high melting point, thermal stability, and ability to retain strength at elevated temperatures. The sand is mixed with a binder to create a mold that can hold its shape when the molten metal is poured. Two popular types of binders used are clay and resin. Clay is often used in traditional sand casting methods due to its natural adhesive properties, while resin systems tend to offer better surface finish and dimensional accuracy.
2. Binders
Binders are essential for maintaining the integrity of the sand mold. Clay, specifically bentonite clay, is used in green sand casting, where water is added to the sand mixture to activate the binding properties. In contrast, chemically bonded sands, which utilize phenolic resins or other organic binders, provide superior strength and can cater to more complex geometries. The choice of binder directly impacts the mold’s ability to withstand the heat from molten metal and the ease of mold removal after casting.
3. Metals
materials used for sand casting
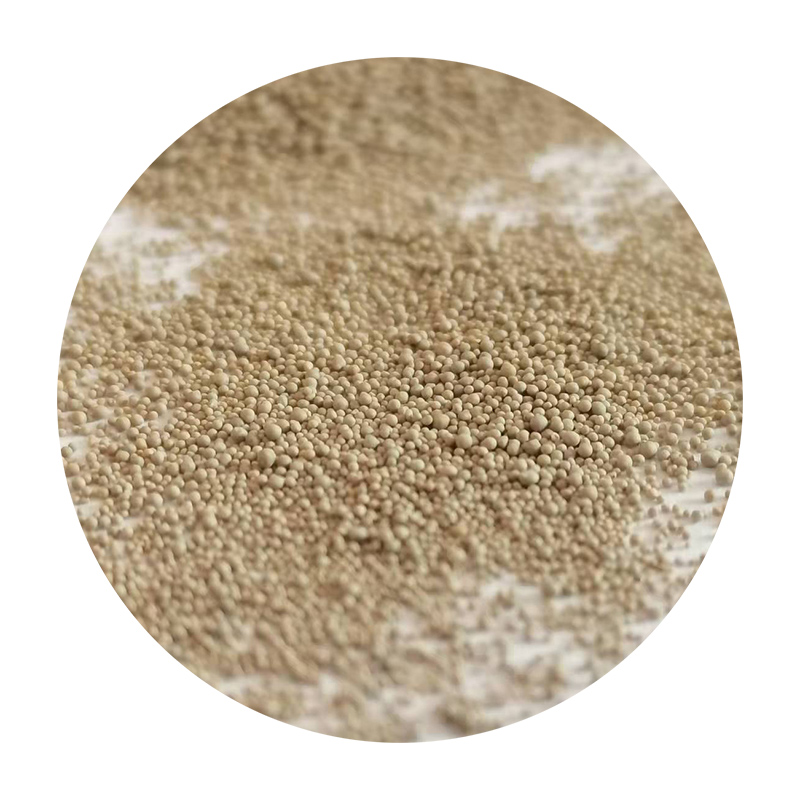
A variety of metals can be cast using the sand casting process, with some of the most commonly used being aluminum, iron, steel, and bronze. Aluminum alloys are particularly popular due to their lightweight and corrosion-resistant properties. Iron castings, especially those made from gray iron, are known for their excellent wear resistance and machinability. The selection of metal is dictated by the application's requirements, including strength, ductility, and thermal conductivity.
4. Additives
To enhance the performance of the sand and improve the casting process, various additives are also utilized. These may include fire clay, which helps increase the mold's strength and thermal resistance, or graphite, which improves the surface finish of the final product. Other additives may be employed for specific applications, such as anti-oxidants or agents that prevent sand from sticking to the mold.
5. Coatings
Mold coatings are added to the interior of the mold to produce a better surface finish and to minimize the likelihood of defects. Typically made from fine refractory materials, coatings create a barrier between the molten metal and the sand, reducing the risk of sand fusion and improving the surface quality of the castings.
In conclusion, the materials used in sand casting—from silica sand and binders to various metals and additives—are fundamental to the efficiency and effectiveness of the casting process. Each component contributes to the overall properties of the final product, making it essential for manufacturers to carefully select the right materials according to the specifications of their projects. By understanding the role of each material, foundries can optimize their processes and produce high-quality castings that meet the demands of modern applications.
Post time:Sht . 03, 2024 11:03
Next:Types of Sand Used in Foundry - Comprehensive Guide