Lost Foam Casting An Innovative Metal Casting Technique
Lost foam casting is a cutting-edge metal casting process that has gained popularity due to its ability to produce complex and precision-engineered components. This technique combines the simplicity of traditional sand casting with the advantages of modern materials, making it suitable for a wide range of applications, from automotive parts to artistic sculptures.
The process begins with a foam pattern, typically made from expanded polystyrene (EPS), which is created to match the desired shape of the final metal component. Unlike traditional casting methods that use metal patterns, lost foam casting uses a foam model that is coated with a refractory material to create a mold. Once the mold is prepared, the foam pattern is placed into a container filled with fine sand. The sand’s tight packing ensures that the shape is preserved when the foam is subsequently melted away.
One of the main advantages of lost foam casting is its ability to capture intricate details and complex geometries that might be challenging or impossible to achieve with traditional methods. Additionally, because the foam pattern vaporizes during the pouring of the molten metal, there is no need for additional core or parting lines. This not only reduces the overall weight of the component but also minimizes finishing work, allowing for a more streamlined manufacturing process.
lost foam casting
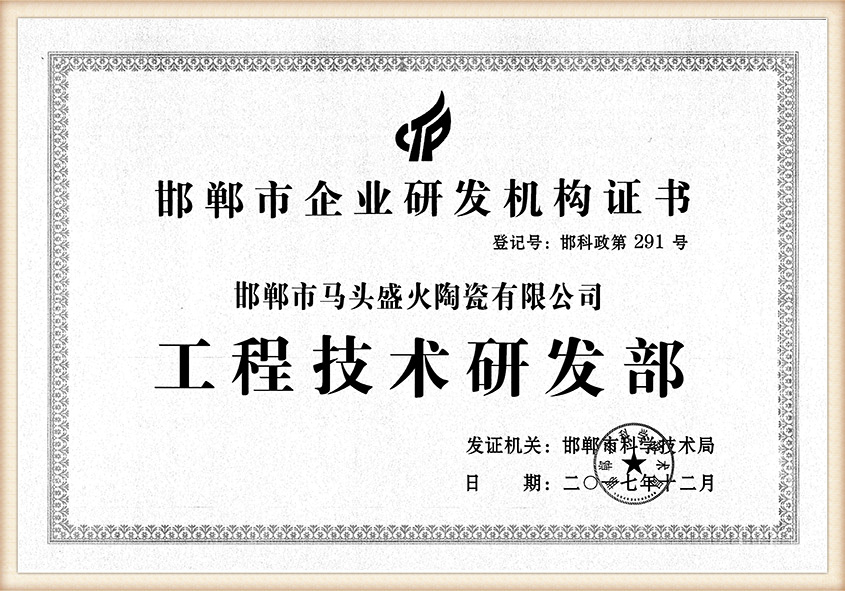
Environmental benefits also accompany this innovative technique. Traditional casting methods can generate considerable waste and may require extensive setup for each new pattern. In contrast, lost foam casting utilizes EPS, which can be recycled, thus reducing material waste. Furthermore, since the foam pattern is vaporized rather than removed, the process eliminates the need for additional materials typically used in core making.
Lost foam casting is particularly advantageous in industries where precision and efficiency are paramount. For instance, the automotive industry utilizes this technique to create lightweight yet sturdy components that enhance fuel efficiency and reduce emissions. Moreover, as manufacturers continue to seek ways to innovate and cut costs, lost foam casting serves as a viable alternative to more conventional metalworking processes.
In conclusion, lost foam casting represents a significant advancement in manufacturing technology. Its capacity for producing detailed and lightweight components, along with its environmental advantages, makes it a preferred choice for many industries looking to maintain competitiveness in a fast-evolving market. As this technique continues to evolve and improve, it is likely to play a pivotal role in shaping the future of metal casting.
Post time:Sht . 23, 2024 03:49
Next:cerabeads sand