Lost Foam Casting An Innovative Casting Technique
Lost foam casting (LFC) is a sophisticated and efficient metal casting process that has gained significant traction in various manufacturing sectors. This method is known for its ability to produce complex shapes with high precision and minimal waste, making it an attractive option in today’s resource-conscious environment. In this article, we will explore the fundamentals of lost foam casting, its advantages, applications, and future prospects.
Fundamentals of Lost Foam Casting
The lost foam casting process is a method in which a foam pattern, typically made of expanded polystyrene (EPS), is used to create a mold for metal casting. The process begins with the fabrication of a foam model of the part to be cast. This foam pattern is then coated with a ceramic or sand mixture that forms the mold shell. Once the coating is applied, the foam is heated, causing it to vaporize and leave behind a cavity that closely resembles the original foam pattern. The molten metal is then poured into this cavity, filling the space left by the vanished foam.
One of the key features of lost foam casting is its ability to produce intricate designs without the need for complex tooling. The process allows for the incorporation of undercuts and other geometrical features, which are often challenging to achieve with traditional casting methods.
Advantages of Lost Foam Casting
Lost foam casting offers several advantages that appeal to manufacturers and engineers alike. One of the most significant benefits is the reduction of material waste. Traditional sand casting processes often produce excess material that must be trimmed away, whereas lost foam casting eliminates this issue by directly using foam patterns that are vaporized during pouring.
Additionally, LFC provides high-dimensional accuracy, which is crucial for industries requiring tight tolerances, such as aerospace and automotive manufacturing. The surface finish of parts produced through this method is typically superior to that obtained from other casting techniques, resulting in lower machining costs and shorter lead times.
lost-foam casting
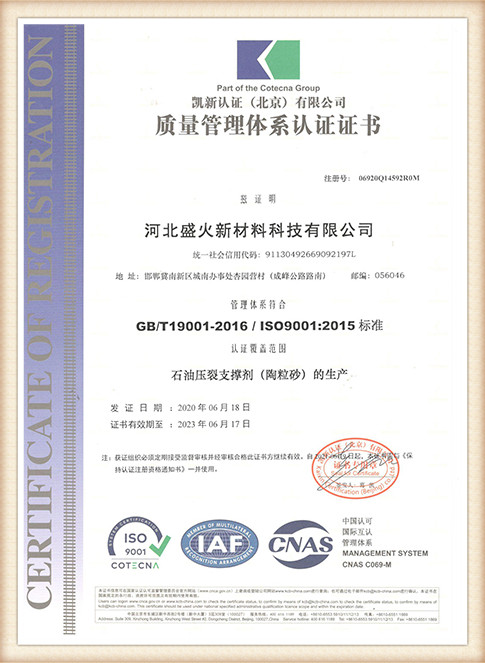
The process is also energy-efficient, as the foam vaporizes at a relatively low temperature, leading to reduced energy consumption during the casting process. This efficiency, coupled with lower material costs, makes LFC a financially viable option for many manufacturing companies.
Applications of Lost Foam Casting
Lost foam casting is versatile and is applied across various industries. In the automotive sector, it is used to produce engine components, transmission cases, and other critical parts that require precision and durability. Its ability to accommodate lightweight designs makes LFC particularly appealing for manufacturers focused on enhancing fuel efficiency.
The aerospace industry benefits from LFC's capability to produce complex shapes with high surface quality, making it suitable for components such as landing gear and structural parts. Additionally, many industrial and agricultural equipment manufacturers utilize lost foam casting for parts that demand high strength-to-weight ratios.
Moreover, the method is gaining popularity in artistic applications, such as sculptures and decorative items, where detail and finish are paramount. The flexibility offered by lost foam casting allows artists to explore new designs that would be cumbersome to create using traditional methods.
Future Prospects of Lost Foam Casting
As industries increasingly emphasize sustainability and efficiency, the future of lost foam casting looks promising. Continued advancements in materials, such as biodegradable or recyclable foam patterns, could further enhance the environmental benefits of this casting method. Innovations in automation and process control are expected to streamline production and improve quality assurance in LFC applications.
In conclusion, lost foam casting is an innovative metal casting technique that offers significant advantages in terms of precision, material efficiency, and versatility. With its growing acceptance across various industries, LFC is poised to remain a vital player in the landscape of modern manufacturing. As technology advances and sustainability becomes a priority, lost foam casting will likely evolve to meet the challenges and demands of the future.
Post time:Nën . 19, 2024 03:31
Next:Top Sand Casting Manufacturers for Quality and Precision in Metal Casting Solutions