The Importance of Sand Casting
Sand casting, one of the oldest and most versatile metal casting methods, has been a cornerstone in the manufacturing industry for centuries. This technique involves creating a mold from a sand mixture that can be shaped to form various objects, ranging from small components to large machinery parts. Understanding the significance of sand casting can shed light on its continued relevance and application in modern manufacturing processes.
Cost-Effective Production
One of the primary reasons for the enduring popularity of sand casting is its cost-effectiveness. The materials required for sand casting – primarily sand, a bonding agent, and water – are readily available and inexpensive, making this method highly economical for both small-scale and large-scale production. This affordability enables manufacturers to produce complex shapes and designs without the need for expensive machinery or extensive setup costs, making it an attractive option especially for smaller businesses or startups.
Versatility in Material Use
Sand casting is not limited to just one type of metal; it can accommodate a wide variety of materials including aluminum, magnesium, copper, and iron. This versatility allows manufacturers to choose the metal that best suits their requirements, whether for strength, ductility, or corrosion resistance. Additionally, sand casting can be used to create intricate designs, which makes it suitable for a range of industries including automotive, aerospace, construction, and art.
Ability to Create Complex Geometries
importance of sand casting
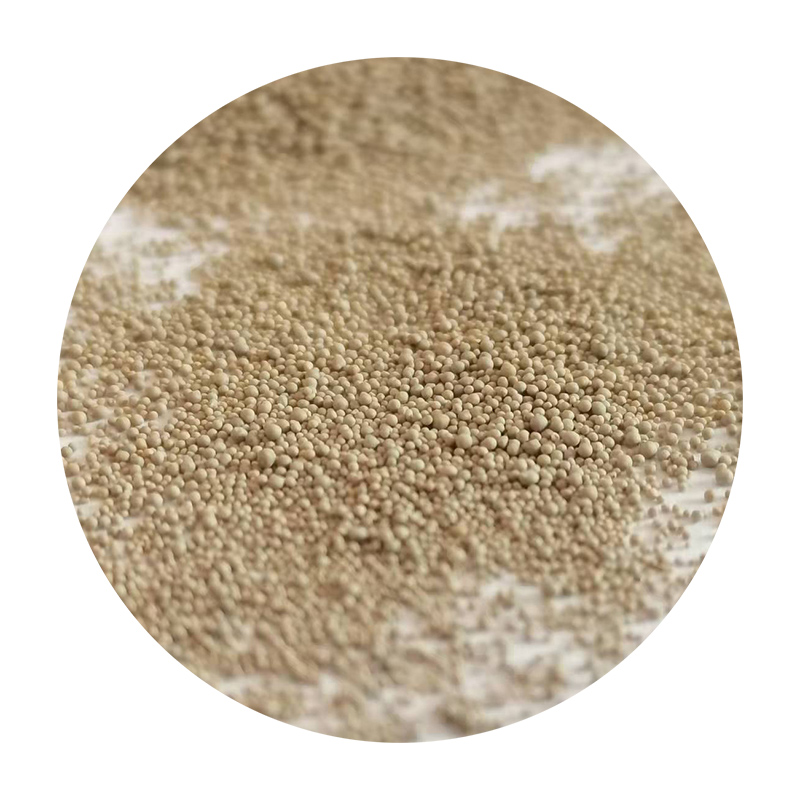
The capability to produce complex geometries is another critical advantage of sand casting. The malleability of sand as a molding material enables it to capture detailed designs and intricate features, making it possible to create detailed components that might be difficult or impossible to produce with other methods, such as die casting or forging. This feature not only enhances the aesthetic appeal of the final product but also contributes to the functional performance of the components, making sand casting an integral part of design engineering.
Ease of Modification and Flexibility
Another significant aspect of sand casting is the ease of making modifications. If a design needs adjustments, altering the sand mold is often simpler and more cost-effective than changing a permanent mold used in other casting methods. This flexibility allows manufacturers to respond quickly to changes in demand or specifications without incurring high costs associated with redesigning and fabricating new molds.
Contribution to Innovation
As technology advances, so does the application of sand casting. With the advent of 3D printing, creating sand molds has become more efficient, leading to shorter lead times in producing components. This synergy between traditional sand casting and modern technology not only enhances productivity but also drives innovation in product development. Companies are now able to experiment with designs and materials at a fraction of the previous cost and time.
In conclusion, the importance of sand casting lies in its adaptability, cost-effectiveness, and ability to produce intricate designs. As industries continue to demand precision and innovation, sand casting remains a crucial method in the manufacturing landscape. Its contributions to various sectors underline its enduring legacy and potential for future developments. As the industry evolves, sand casting will likely maintain its relevance, adapting to new technologies and challenges, ensuring its place in modern manufacturing processes.
Post time:Tet . 07, 2024 03:46
Next:metal sand casting