How Accurate is Sand Casting?
Sand casting is one of the oldest and most versatile metal casting processes used in manufacturing today. Known for its ability to produce large, complex parts, this method has remained popular in a variety of industries, from automotive to aerospace. However, a question often arises regarding the accuracy of sand casting. How precise is this method, and what factors influence its dimensional fidelity?
To understand the accuracy of sand casting, it's essential to look at the process itself. Sand casting involves creating a mold from a mixture of sand and a binder, typically clay. Once the mold is prepared, molten metal is poured into it to create the desired shape. After the metal cools and solidifies, the mold is broken away, revealing the cast part.
How Accurate is Sand Casting?
The design of the part also plays a crucial role in the accuracy of sand casting. Features such as draft angles, wall thickness, and the complexity of geometry can impact how well the mold holds the shape during the casting process. Parts with intricate designs may require more sophisticated mold-making techniques, such as the use of cores, to achieve the desired accuracy. Engineers often need to consider these factors during the design phase to ensure that the final part will meet tolerances.
how accurate is sand casting
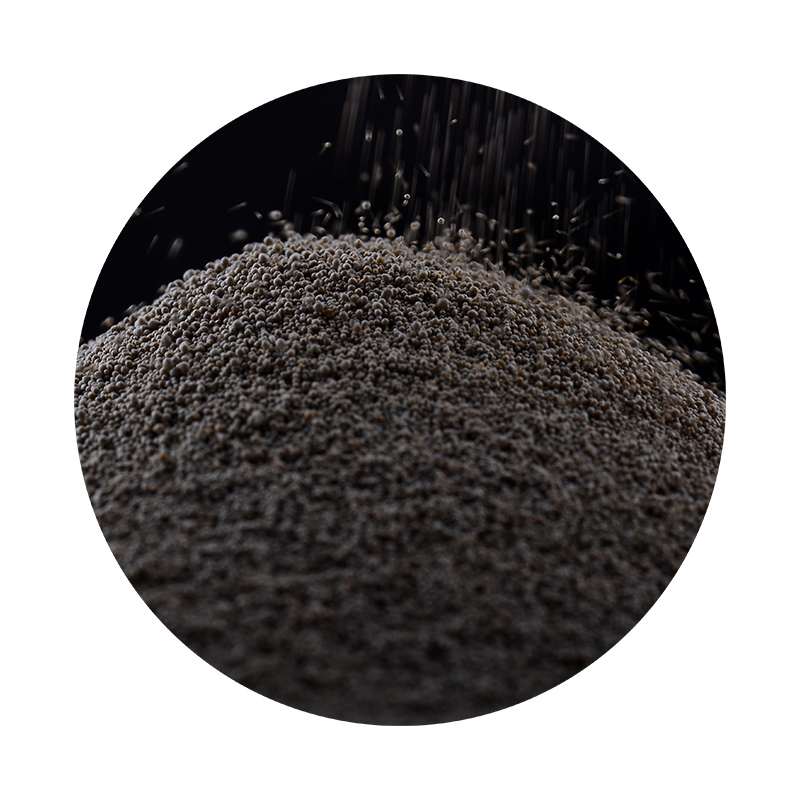
Furthermore, the temperature of the molten metal and the cooling rate significantly influence accuracy. If the metal is poured at too high a temperature, it may lead to defects such as warping or shrinkage. Conversely, a slower cooling rate can result in improved dimensional stability, but it may also increase the likelihood of defects such as porosity. Finding the optimal balance in pouring temperature and cooling rate is crucial for minimizing deviations from the intended specifications.
Dimensional tolerances for sand cast parts typically range from ±0.5% to ±1%, depending on the size and complexity of the part. Larger parts may have larger tolerances, while smaller, more intricate components can achieve tighter tolerances. Modern advancements in technology, including 3D printing and computer-aided design (CAD), have further enhanced the accuracy of sand casting. These technologies enable manufacturers to create more precise molds and optimize the entire casting process.
Another consideration is the use of post-casting processes, such as machining or finishing techniques. These operations can often correct inaccuracies resulting from the casting process, allowing manufacturers to meet stringent specifications. For high-precision applications, post-processing may be necessary to ensure that parts meet required tolerances, adding to the overall cost and lead time.
Sand casting also excels in producing low to medium volumes of parts. It is particularly advantageous for prototypes or custom components that require flexibility in design. While the initial setup can be labor-intensive, once a mold is made, subsequent casts are relatively rapid and economical. This makes sand casting an attractive option for industries looking to balance cost, speed, and accuracy.
In summary, while sand casting may not achieve the same level of accuracy as some other casting methods, such as investment casting, it offers a balance of versatility and cost-effectiveness. Achieving the desired accuracy depends on numerous factors, including mold quality, part design, and process control. By paying careful attention to these variables, manufacturers can optimize their sand casting processes to produce components that meet demanding specifications. Overall, when executed properly, sand casting remains a robust option in the realm of metal manufacturing.
Post time:Nën . 11, 2024 05:47
Next:Exploring the Benefits and Applications of Coated Sand in Various Industries