Dry Sand Casting An Overview
Dry sand casting is a traditional metal casting process that has been widely used in the manufacturing industry for decades. This method offers several advantages, including versatility, cost-effectiveness, and the ability to produce complex shapes with high precision. In this article, we will explore the principles of dry sand casting, its process, materials, and applications, along with its advantages and disadvantages.
Principles of Dry Sand Casting
At its core, dry sand casting involves creating a mold from dry sand mixed with a bonding agent, typically sodium silicate. This mixture is packed around a pattern, which represents the final product. Once the mold is formed, it is baked to harden the sand and create a stable negative impression of the pattern. This method is distinct from green sand casting, where the mold retains moisture, making it less stable under high temperatures.
The Process
The dry sand casting process can be broken down into several key steps
1. Pattern Creation The first step is to create a pattern of the part to be cast. This pattern is usually made from metal, wood, or plastic and must be slightly larger than the desired final product to account for shrinkage during solidification.
2. Mold Preparation The dry sand mixture is prepared by blending dry sand with a bonding agent. The combination is then packed around the pattern to form the mold. The dry nature of the sand allows for a finer finish on the cast part.
3. Baking the Mold After the sand has been shaped around the pattern, the mold is baked in an oven to harden the bonding agent. This step is crucial for providing the mold with strength and durability, allowing it to withstand the molten metal's high temperatures.
dry sand casting
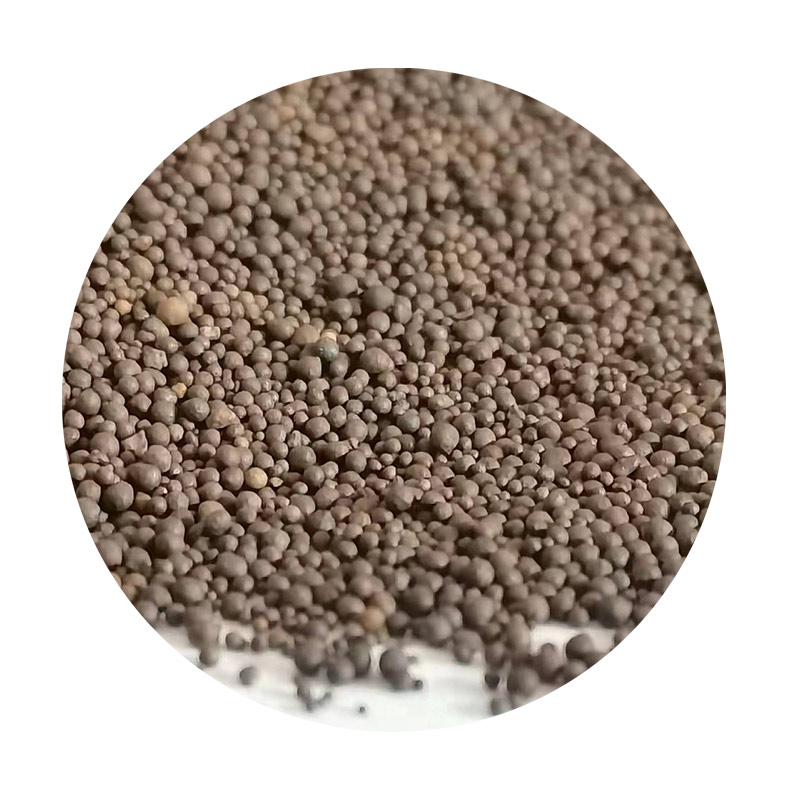
4. Metal Pouring Once the mold has cooled and hardened, it is ready for metal pouring. The chosen metal, often aluminum or iron, is melted in a furnace and poured into the mold cavity through a sprue.
5. Cooling and Finishing After the metal has been poured, it is allowed to cool and solidify. Once solidified, the mold is broken apart to reveal the cast part. The final step involves cleaning and finishing the cast piece to meet specifications.
Materials Used
The primary material for dry sand casting is, of course, sand. The sand used is usually high-quality silica sand, which is finely grained and uniform in shape. The bonding agent, sodium silicate, plays a crucial role in ensuring the sand grains adhere together securely during the baking process. The choice of metal varies based on the desired properties of the final product, with aluminum alloys being popular for their lightweight and corrosion resistance.
Applications
Dry sand casting is utilized across various industries, including automotive, aerospace, and machinery. It is particularly useful for producing intricate components such as engine blocks, pump housings, and other heavy machinery parts that require a high degree of accuracy and durability.
Advantages and Disadvantages
One of the primary advantages of dry sand casting is its ability to produce complex shapes with excellent surface finish quality. The dry sand method allows for reusable molds and faster production times. However, there are also limitations. The process can be more expensive than other molding methods, and the molds can be less durable if not properly baked.
In conclusion, dry sand casting is a valuable metal casting technique, combining tradition with modern applications. Its ability to produce detailed and robust components makes it a preferred choice for many manufacturing applications. As industries continue to evolve, dry sand casting will likely remain a critical process in the production of high-quality metal parts.
Post time:Nën . 12, 2024 06:03
Next:sanding resin 3d prints