Different Types of Sand Casting
Sand casting is one of the oldest and most widely used metal casting processes. It involves creating a mold from sand to shape molten metal into the desired form. Due to its versatility and cost-effectiveness, sand casting is employed in various industries, including automotive, aerospace, and art. This article explores the different types of sand casting processes, highlighting their unique features and applications.
1. Green Sand Casting
Green sand casting, the most common form of sand casting, uses a mixture of sand, clay, and water to form the mold. The term green refers to the moisture content of the sand mixture and not the color of the sand. The process begins with shaping the mixture into two halves of a mold—one for the pattern and another for the cope. The pattern is then removed, and the two halves are assembled, followed by pouring the molten metal into the cavity.
One of the key advantages of green sand casting is its ability to produce complex geometries and fine surface finishes. The process is also relatively inexpensive and allows for quick mold production. However, it does have limitations, such as maintaining mold strength and dimensional accuracy over multiple pours.
2. Dry Sand Casting
Dry sand casting utilizes a sand mixture cured with a binding agent, which hardens when exposed to heat. The result is a more durable mold compared to green sand molds. This process is particularly advantageous for casting large, heavy components that require high dimensional accuracy and surface finish.
The dry sand casting method minimizes the risk of mold collapse during the metal pouring phase, which can lead to better yield and reduced waste. However, the initial setup costs can be higher compared to green sand casting, making it less economical for small-scale production or simple parts.
3
. Shell Mold Castingdifferent types of sand casting
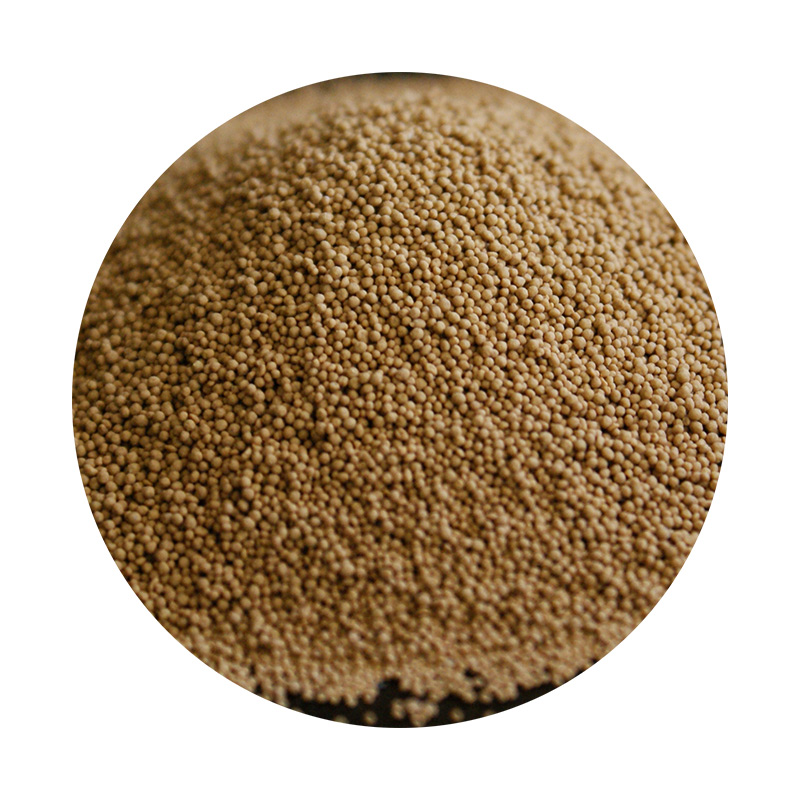
Shell mold casting involves creating a thin shell of sand and resin around a pattern. The pattern is heated, causing the resin-bonded sand to adhere and solidify into a mold. Once the shell has formed, it is separated from the pattern, and the two halves are assembled.
This casting method allows for excellent surface finishes and high dimensional accuracy, making it suitable for producing intricate components such as engine blocks and intricate machine parts. However, the process can be more expensive due to the need for specialized equipment and additional steps in mold preparation.
4. Expendable Pattern Casting
Expendable pattern casting employs patterns made from materials like wax or polystyrene that are melted away or vaporized during the casting process. This technique, often referred to as lost-foam casting or investment casting, allows for a high degree of precision and the ability to create complex geometries without the need for traditional molds.
While this method yields superior surface finish and dimensional accuracy, it also tends to be more costly, making it more suitable for specialized applications or low-volume production rather than mass manufacturing.
5. Vacuum Casting
Vacuum casting is a variation of sand casting that uses reduced atmospheric pressure to draw molten metal into the mold. The vacuum allows for the detection of minute holes and defects in the mold, resulting in high-quality castings. This method is most applicable for small-batch production runs or high-performance components requiring minimal porosity.
Conclusion
Each type of sand casting offers its unique advantages and disadvantages, making them suitable for different applications. When selecting the appropriate sand casting process, considerations such as the complexity of the design, required surface finish, production volume, and cost constraints must be taken into account. Understanding these different methods allows manufacturers to choose the most effective casting technique for their specific needs, ensuring quality and efficiency in metal casting production.
Post time:Dhj . 25, 2024 20:03
Next:Exploring the Benefits of Resin Coated Frac Sand in Hydraulic Fracturing Operations