Custom Sand Casting A Versatile Manufacturing Process
Custom sand casting is a versatile and widely used manufacturing process that allows for the creation of complex metal parts and components with various shapes and sizes. It is a method that has been employed for centuries, evolving over time to meet the demands of modern industry. In this article, we will explore the fundamentals of custom sand casting, its advantages, applications, and the steps involved in the process.
What is Custom Sand Casting?
At its core, sand casting is a process that involves creating a mold from sand to produce a metal cast. The process begins with the creation of a pattern, which is a replica of the final product. This pattern is typically made from wood, metal, or plastic. Once the pattern is ready, it is used to form a mold in the sand.
The sand used in this process is typically mixed with a binder to hold the sand grains together, providing enough strength to withstand the molten metal. When the mold is ready, the next step is to pour the molten metal into it, allowing it to solidify and take the shape of the pattern. After cooling, the mold is broken away to reveal the final casting.
Advantages of Custom Sand Casting
Custom sand casting offers several advantages that make it an attractive choice for manufacturing
1. Flexibility in Design One of the most significant advantages of sand casting is its ability to produce intricate and complex shapes that would be difficult to achieve with other manufacturing techniques. This flexibility allows designers to create customized parts tailored to specific requirements.
2. Cost-Effective for Low to Medium Volumes While sand casting may not be the most cost-effective solution for large-scale production, it is highly economical for low to medium volume manufacturing. The investment required for pattern-making can be offset by the reduced costs associated with the actual casting process.
3. Material Variety Sand casting can accommodate a wide range of metals, including aluminum, iron, and steel. This versatility in material choice allows manufacturers to select the best metal for the desired application, whether it be for strength, weight, or corrosion resistance.
4. Short Lead Times The sand casting process can often be executed quickly, particularly when using existing patterns. This enables manufacturers to respond rapidly to market demands, making it ideal for custom and urgent orders.
5. Post-Casting Modifications Unlike some other manufacturing processes, sand casting allows for post-casting modifications. This means that additional machining or finishing processes can be applied after the initial casting, resulting in high-precision parts.
Applications of Custom Sand Casting
Custom sand casting is utilized across various industries due to its adaptability. Some common applications include
custom sand casting
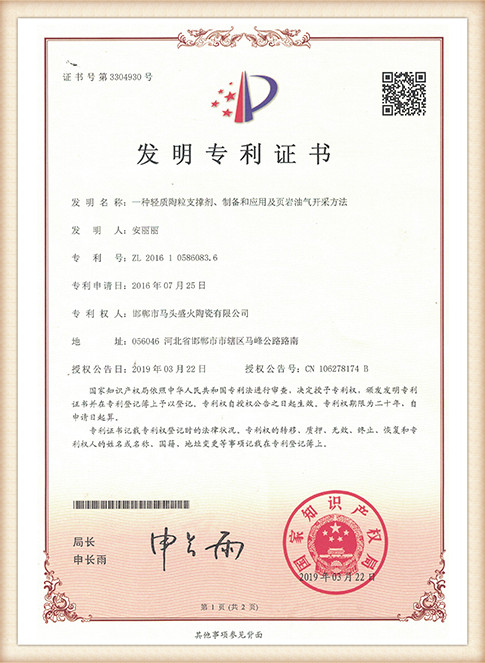
- Automotive Industry Many components of vehicles, such as engine blocks, transmission cases, and brackets, are produced using sand casting. The process allows for the production of robust and lightweight parts necessary for automotive performance.
- Aerospace Sector The aerospace industry demands high precision and reliability in its components
. Sand casting is frequently used to create parts that meet stringent specifications and quality standards.- Construction Equipment Custom sand casting is employed to manufacture parts for construction machinery, including hydraulic components, frames, and gears, ensuring they can withstand harsh operating conditions.
- Art and Sculpture Beyond industrial applications, artists and sculptors often utilize sand casting for creating unique and custom-designed pieces, showcasing its artistic potential.
The Sand Casting Process
The sand casting process can be broken down into several key steps
1. Pattern Creation The initial step involves creating a pattern of the desired object, which serves as the basis for the mold.
2. Mold Making The pattern is then placed in a sand mixture to create the mold. The sand is compacted around the pattern, and once set, the pattern is removed, leaving a cavity.
3. Melting Metal The chosen metal alloy is melted in a furnace, reaching temperatures that vary depending on the material.
4. Pouring The molten metal is poured into the mold cavity, filling it entirely.
5. Cooling and Solidification Once poured, the metal is allowed to cool and solidify, taking the shape of the mold.
6. Removing the Casting After cooling, the mold is broken away, revealing the casting, which may require finishing processes such as sanding or machining.
Conclusion
Custom sand casting is an excellent choice for producing highly customized metal components with precision and efficiency. Its advantages in terms of flexibility, cost-effectiveness, and material versatility make it a preferred method in numerous industries. Whether for industrial applications or artistic endeavors, sand casting continues to play a vital role in the manufacturing landscape.
Post time:Nën . 07, 2024 08:45
Next:Techniques for Sanding 3D Resin Prints to Achieve a Smooth Finish