3D Printed Sand Casting Patterns Revolutionizing Manufacturing
In recent years, the manufacturing industry has witnessed a paradigm shift with the adoption of additive manufacturing technologies, particularly in the realm of casting. Among various innovative methods, 3D printed sand casting patterns have emerged as a game-changer, offering unprecedented benefits in terms of efficiency, design flexibility, and cost-effectiveness. This article explores the significance, process, advantages, and future prospects of 3D printed sand casting patterns in modern manufacturing.
Understanding Sand Casting and Its Traditional Limitations
Sand casting is a widely used manufacturing process that involves creating a mold from sand to produce metal castings. Traditionally, creating patterns for these molds has been a time-consuming and labor-intensive process. Manufacturers often relied on subtractive techniques, such as machining or manual carving, to create patterns from materials like wood or metal. This process not only required substantial time and labor but also limited design capabilities due to tool access and geometric complexities.
The Advent of 3D Printing Technology
The introduction of 3D printing technologies has revolutionized how patterns are produced for sand casting. By utilizing computer-aided design (CAD), manufacturers can create intricate patterns with a level of detail and complexity impossible to achieve with traditional methods. 3D printing allows for the direct construction of sand molds from digital files, streamlining the production process and reducing lead times significantly.
The Process of 3D Printing Sand Casting Patterns
The process begins with the design phase, where engineers create detailed CAD models of the desired casting. These models are then converted into a format suitable for 3D printing. Once the design is finalized, it is printed using a specialized 3D printer capable of working with sand. The printer layers fine grains of sand with a binder material, consolidating them into a rigid mold. Depending on the complexity of the pattern, the process may involve both a pattern and core printing for more elaborate shapes.
After printing, the mold is cleaned and prepared for the casting process. The mold is then filled with molten metal, which solidifies to form the final product. This approach eliminates the need for additional tooling, drastically reducing both production times and costs.
Advantages of 3D Printed Sand Casting Patterns
3d printed sand casting patterns
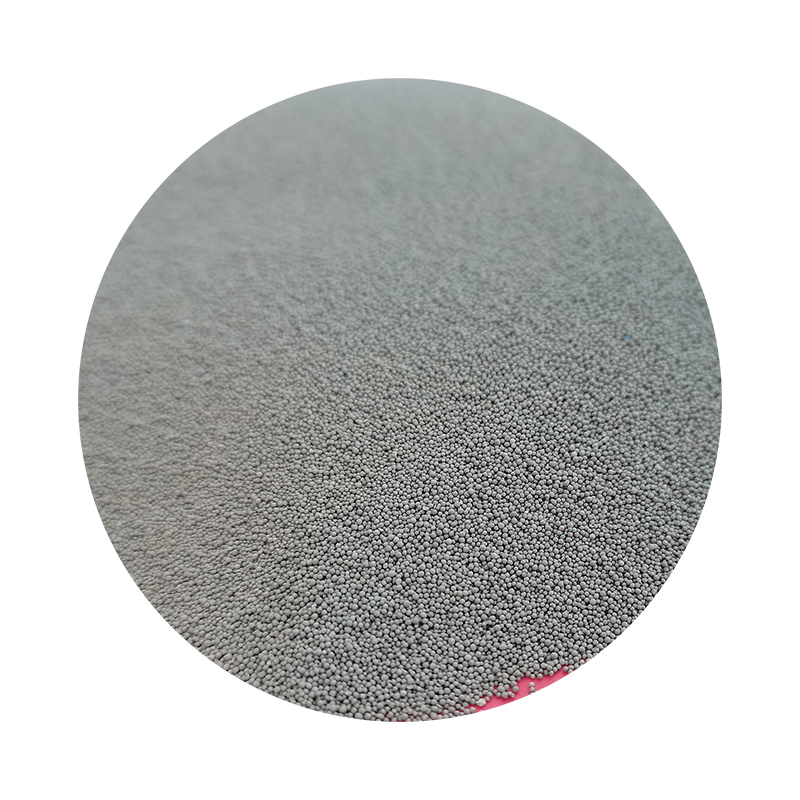
The benefits of employing 3D printed sand casting patterns are manifold
1. Design Flexibility 3D printing allows for the creation of complex geometries and intricate designs that were previously unattainable with traditional methods. This versatility enables manufacturers to innovate and produce lightweight, optimized components.
2. Rapid Prototyping With the ability to quickly print patterns, manufacturers can iterate designs rapidly, facilitating faster product development cycles. This leads to more efficient feedback loops and ultimately results in better final products.
3. Cost Reduction By minimizing the need for expensive tooling and cutting down on labor costs associated with traditional pattern manufacturing, 3D printing can significantly lower overall production costs, making it more accessible for small and medium-sized enterprises.
4. Sustainability Reducing waste is a critical concern in manufacturing. 3D printing utilizes only the material needed to create the mold, minimizing scrap rates and contributing to more sustainable manufacturing practices.
Future Directions
As technology continues to advance, the potential of 3D printed sand casting patterns will likely expand further. Future innovations could include enhanced materials that improve the strength and durability of the molds, as well as advancements in post-processing techniques that enhance the surface finish of cast components.
Moreover, the integration of artificial intelligence and machine learning in the design process could pave the way for optimized patterns that enhance performance while reducing material usage.
Conclusion
3D printed sand casting patterns are not just a fleeting trend; they represent a significant leap forward in manufacturing technology. By combining the speed and flexibility of 3D printing with the traditional casting process, manufacturers can meet the demands of a rapidly evolving marketplace. As industries increasingly embrace this transformative technology, the future of sand casting looks brighter than ever, promising innovation, sustainability, and efficiency.
Post time:Tet . 19, 2024 06:08
Next:sand casting components