Understanding Foundry Sand A Crucial Component in Metal Casting
Foundry sand is a key material used in the metal casting industry, playing a vital role in shaping and creating high-quality metal parts. It is specifically processed sand that is utilized in the molds and cores for casting operations. The primary purpose of foundry sand is to provide a stable, uniform, and reusable material that can withstand high temperatures while allowing for intricate designs and detailed features in the final product.
Composition and Types of Foundry Sand
Foundry sand is primarily composed of silica, which is abundant in nature and provides the necessary properties for casting. The most common type of foundry sand is silica sand, known for its high melting point and ability to resist thermal shock. Other types of foundry sand include olivine sand, zircon sand, and chromite sand, each offering distinct advantages depending on the specific casting requirements. For instance, olivine sand boasts superior strength and is often used in high-temperature applications, while zircon sand offers excellent thermal stability and low expansion rates.
Properties of Foundry Sand
The effectiveness of foundry sand in the casting process can be attributed to several key properties. Firstly, its refractory nature allows it to withstand the extreme temperatures generated during metal pouring, which can exceed 1,500 degrees Celsius. Secondly, the shape and grain size of the sand are crucial for creating molds with precise details. Fine grains provide a smooth finish, while coarser grains can enhance permeability, allowing gases to escape during casting.
Another important property is the sand's ability to be reused. Foundry sand can be reclaimed and recycled, which not only reduces waste but also lowers material costs for foundries. Proper cleaning and processing methods enable the reuse of foundry sand multiple times, making it an economically favorable choice in the industry.
what is foundry sand
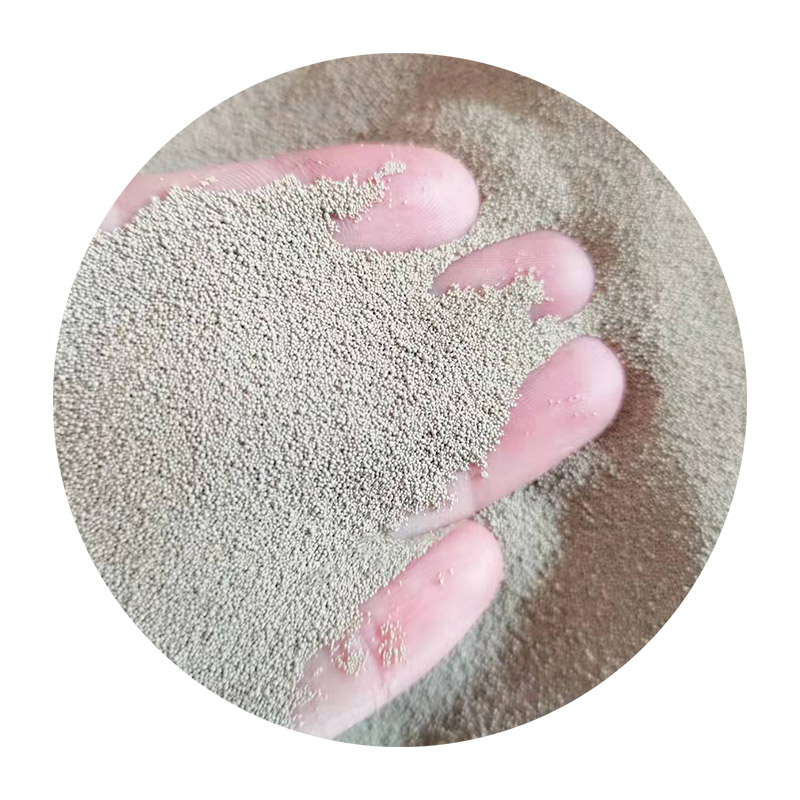
Applications in Metal Casting
Foundry sand is predominantly used in various metal casting processes, including sand casting, investment casting, and shell molding. In sand casting, a pattern is embedded in a mold made from foundry sand, and molten metal is poured to create the final shape. This method is widely favored due to its cost-effectiveness and ability to produce complex geometries.
In addition to traditional applications, foundry sand is gaining traction in 3D printing technologies, where it is used in the production of molds and cores for additive manufacturing processes. This advancement opens up new possibilities for product design and customization, allowing for quicker turnaround times and greater efficiency.
Environmental Impact and Sustainability
The use of foundry sand has raised environmental concerns, particularly regarding its disposal. To address these issues, many foundries are adopting sustainable practices, such as reusing and recycling sand, and even repurposing spent foundry sand in construction projects or as a soil amendment. By implementing these strategies, the foundry industry is making strides toward minimizing its environmental footprint while maintaining operational efficiency.
Conclusion
In summary, foundry sand is an essential material in the metal casting industry, offering unique properties that are critical for the production of high-quality metal parts. Its composition, applications, and recyclability make it a valuable resource in various casting processes. As the industry continues to evolve, embracing sustainability and innovative technologies will be key to unlocking the full potential of foundry sand, ensuring its relevance for years to come. Understanding foundry sand not only highlights its importance in manufacturing but also its role in fostering sustainable practices in the metal casting sector.
Post time:Sep . 23, 2024 20:06
Next:High Efficiency Techniques for Volume Sand Casting in Modern Manufacturing