Sand Casting Foundry Process An Overview
Sand casting, a versatile and widely used manufacturing process, is known for its ability to create intricate metal components with excellent dimensional accuracy. This process involves several steps that transform raw materials into final products, utilizing sand as the primary molding material. In this article, we will explore the sand casting foundry process, shedding light on its stages, advantages, and applications.
The Sand Casting Process
The sand casting process begins with the preparation of a pattern, which is a replica of the object to be cast. Patterns can be made from various materials, including wood, metal, or plastic. The design of the pattern is critical, as it must accommodate shrinkage of the metal during cooling and create any necessary allowances for machining.
1. Molding
Once the pattern is ready, the next step is molding. A mixture of sand, clay, and water is prepared to create the mold. This mixture is known as sand, and it possesses excellent properties for casting. The pattern is placed in a molding box, and sand is packed around it. The sand particles are bound together by the clay, forming a rigid mold once compacted. It is important to ensure that the mold is free from defects, as any imperfections will translate to the final casting.
2. Core Making
For complex designs that require internal cavities, cores are created. Cores are additional sand molds placed inside the main mold to form internal features. They are made in a similar way to the main mold, ensuring the right shape, size, and stability to be able to withstand the molten metal.
3. Melting
With the mold and cores prepared, the next step is metal melting. The metal chosen for casting is typically aluminum, iron, or bronze, depending on the application and desired properties. The metal is placed in a furnace and heated until it reaches a molten state. Temperature control is crucial in this stage, as it affects the quality of the final product and the fluidity of the molten metal.
4. Pouring
sand casting foundry process
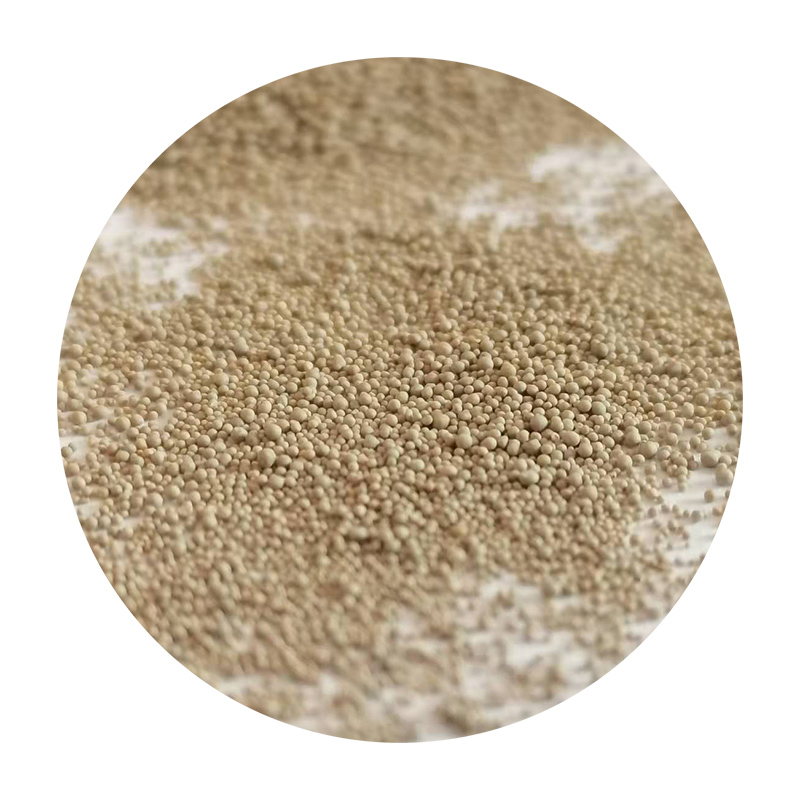
Once the metal is molten, it is poured into the mold using a ladle or automated pouring system. The pouring process must be done carefully to avoid turbulence, which can introduce defects like air entrapment and inclusions. The metal fills the cavity of the mold and around the core, allowing it to take the shape of the pattern.
5. Cooling and Solidification
After pouring, the molten metal must cool and solidify. This process can take several hours, depending on the size and thickness of the casting. Once cooled, the mold is broken away, revealing the casting inside. The quality of the cooling process significantly impacts the metallurgical properties of the casting, influencing factors such as strength, hardness, and surface finish.
6. Finishing
The final step in the sand casting process involves finishing operations. This includes removing any excess material, cleaning the casting from sand, and performing machining processes to achieve the desired dimensions and surface quality. Additional treatments, such as heat treatment or surface coatings, may also be applied to enhance the properties of the casting.
Advantages of Sand Casting
Sand casting offers several advantages, making it a preferred choice for many manufacturing applications. It can produce large and complex shapes with intricate details. The process is also relatively cost-effective, particularly for low to medium production volumes. Furthermore, the tooling costs are lower compared to other methods, as patterns can be reused multiple times.
Applications
Sand casting is used in various industries, including automotive, aerospace, and machinery. Components such as engine blocks, valve bodies, and various brackets are commonly produced using this method. Its versatility and adaptability to different materials and design requirements make sand casting an essential process in modern manufacturing.
Conclusion
In summary, the sand casting foundry process is a crucial technique in metal manufacturing. By understanding its steps, advantages, and applications, one can appreciate its role in creating durable and high-quality products. As industries evolve and technology advances, sand casting will continue to play a vital role in meeting manufacturing challenges.
Post time:Oct . 17, 2024 10:41
Next:make sand casting