Understanding Materials Used in Sand Casting
Sand casting is one of the oldest and most versatile manufacturing processes used to create metal components. This technique is favored for its simplicity, cost-effectiveness, and ability to produce complex shapes. At the heart of sand casting is the material used, primarily sand, which plays a crucial role in defining the quality and characteristics of the final product. Understanding the materials involved in sand casting is essential for optimizing the casting process and ensuring the successful production of components.
1. Sand
The primary material used in sand casting is silica sand, which is chosen for its excellent properties. Silica sand is made up of small particles of silicon dioxide (SiO2) and is remarkably easy to mold. The grain size of the sand is crucial; fine grains can provide a smoother finish, while coarser grains can aid in quicker molding and demolding.
In addition to silica sand, other types of sand can be mixed to enhance performance. For instance, olivine sand, which is made from magnesium iron silicate, has superior thermal properties and can withstand higher temperatures, making it ideal for special applications. Furthermore, chromite sand, derived from the mineral chromite, is another alternative that offers excellent thermal stability and minimizes metal penetration due to its dense structure.
2. Binders
To hold the sand grains together, binders are essential. The most common binder used is clay, particularly sodium bentonite, which enhances the plasticity of the sand mixture. The clay particles bind the sand grains when mixed with water, allowing for the creation of molds that can withstand the weight and pressure of the molten metal.
In addition to clay, chemical binders like phenolic urethane resins are increasingly popular due to their ability to produce stronger molds with better surface finishes. These chemical binders cure quickly and are particularly advantageous for high-speed production lines, leading to improved productivity and fewer defects in the final casting.
3. Additives
materials used in sand casting
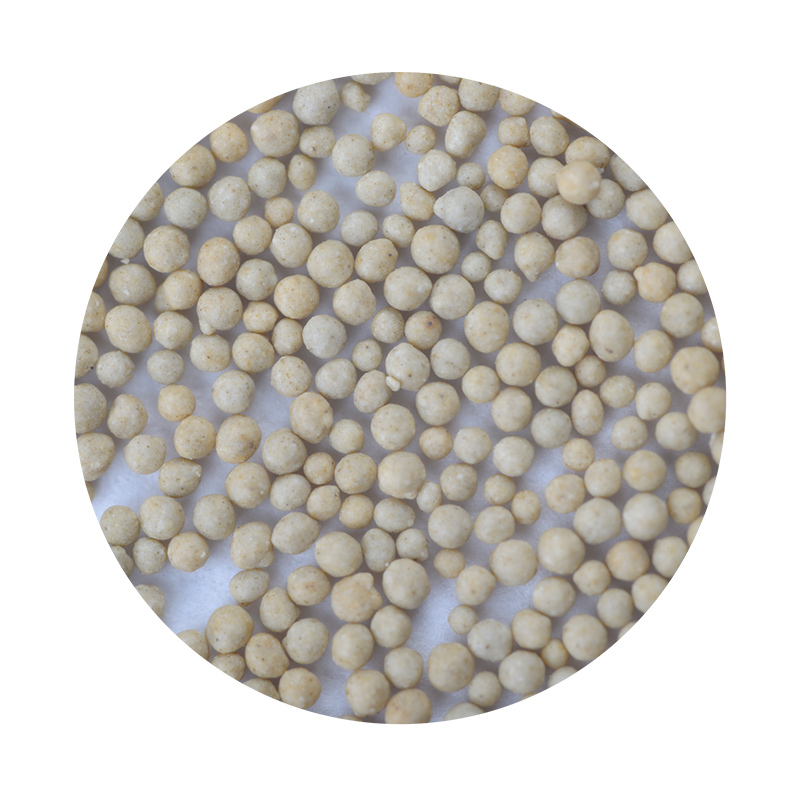
To further improve the properties of the sand mixture, various additives are employed. For example, coal dust or other carbon-containing materials can be added to achieve a smoother finish and reduce the possibility of defects during casting. Additionally, moisture control additives help maintain the right level of humidity in the sand mixture, ensuring good mold integrity.
Another important category of additives includes coloring agents, which are sometimes used for identification purposes or aesthetic reasons, particularly in artistic and decorative castings
.4. Metal Alloys
The choice of metal or metal alloy used in sand casting is paramount to the application it serves. Common choices include aluminum, cast iron, bronze, and brass, each possessing unique properties suited to different applications.
Aluminum is favored for its lightweight and high strength-to-weight ratio, making it ideal for automotive and aerospace components. Cast iron, on the other hand, is known for its excellent castability and wear resistance, making it a popular choice for engine blocks and other heavy-duty applications. Bronze and brass are often chosen for their corrosion resistance and attractive finishes, making them suitable for decorative items and plumbing fittings.
5. Core Materials
In situations where internal cavities are required, cores are introduced into the mold. Cores are typically made from the same sand mixture but may include additional binders to maintain their shape and integrity during casting. Additionally, shell cores, created using a thin layer of sand bonded by resin, can be used for improved dimensional accuracy.
Conclusion
The selection and understanding of materials used in sand casting are crucial for optimizing the casting process and achieving high-quality components. From the choice of sand and binders to the alloys used, each material contributes to the overall performance and reliability of the final product. As technology advances, the materials and techniques in sand casting continue to evolve, leading to more efficient processes and superior outcomes in manufacturing.
Post time:Nov . 17, 2024 11:53
Next:sand cast industries