Lost Foam Casting An Innovative Approach in Foundry Technology
Lost foam casting (LFC) is a modern metal casting process that has gained significant popularity in recent years, particularly within the foundry industry. This innovative technique offers a blend of efficiency, precision, and versatility, making it an attractive option for manufacturers looking to produce complex metal components with minimal waste.
The lost foam casting process is distinguished by its use of a foam pattern made from expanded polystyrene (EPS) or another similar material. Unlike traditional casting methods where patterns are typically made from metal or wood, the foam pattern is designed to be lost in the process. Initially, the foam pattern is created based on the exact specifications of the final metal part. Once formed, the foam piece is coated with a thin layer of a refractory material, which serves as a shell to maintain the shape during casting.
Lost Foam Casting An Innovative Approach in Foundry Technology
One of the most compelling aspects of lost foam casting is its ability to produce near-net shape components. This means that the final product closely resembles the desired shape, minimizing the need for secondary processing steps such as grinding or machining. This not only saves time but also reduces material wastage, making it an environmentally friendly option.
lost foam casting foundry
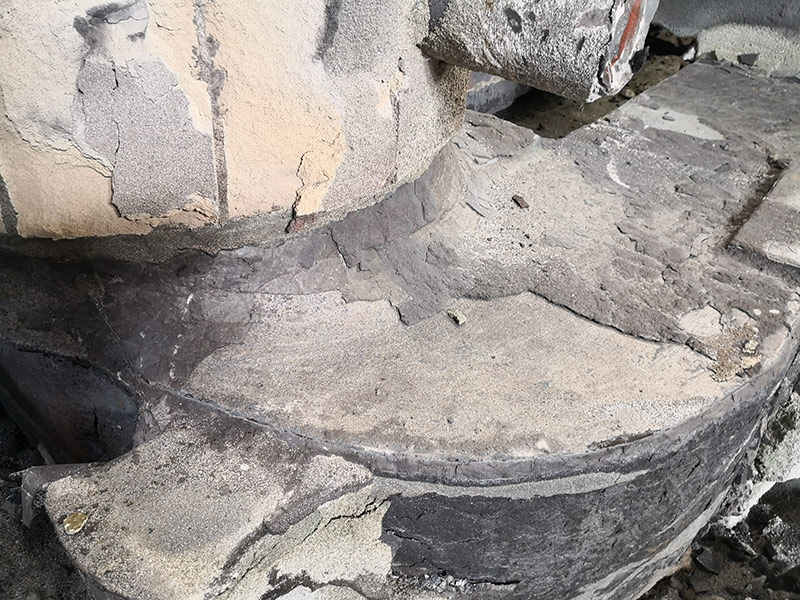
In addition to its efficiency, lost foam casting also allows for the manufacturing of a broad range of materials, including ferrous and non-ferrous metals. This adaptability enables manufacturers to use the process for various applications, from automotive parts and aerospace components to industrial machinery and artistic sculptures. The versatility of LFC extends to the size of the components it can produce, ranging from small intricate parts to large structural pieces.
The lost foam casting process also exhibits superior dimensional accuracy. The foam patterns, being lightweight and highly customizable, can be produced with very tight tolerances. This precision is critical in industries like aerospace and automotive, where components must fit together flawlessly for performance and safety.
However, despite its many advantages, lost foam casting is not without challenges. One of the primary concerns is related to the handling of the foam patterns. Care must be taken during the production and transportation stages to avoid damage, as any imperfection can lead to defects in the final casting. Additionally, controlling the vaporization of the foam during the casting process requires careful temperature and timing management to avoid common issues such as incomplete filling or surface irregularities.
Another challenge lies in the initial investment required for the equipment and setup of a lost foam casting operation. Although the process can lead to significant long-term savings, the upfront costs can be a barrier for some manufacturers, particularly smaller foundries.
In conclusion, lost foam casting represents a significant step forward in foundry technology, offering a combination of efficiency, precision, and environmental sustainability that traditional methods often cannot achieve. As the industry continues to evolve and adapt to new manufacturing challenges, LFC is likely to play a crucial role in shaping the future of metal casting. Its ability to produce complex components with minimal waste and reduced lead times makes it an attractive option for industries seeking innovative solutions to meet modern demands. As research and technology improve, it is expected that lost foam casting will gain even greater traction, further solidifying its place in the foundry landscape.
Post time:Nov . 19, 2024 01:08
Next:Techniques for Achieving a Smooth Finish on Clear Resin Projects