The Iron Sand Casting Process A Comprehensive Overview
Iron sand casting is an innovative manufacturing technique that harnesses the unique properties of iron-rich sands to produce a variety of metal components. This process is often favored for its ability to create durable, intricate, and large-scale castings, making it ideal for industries ranging from automotive to aerospace. In this article, we will delve into the fundamental aspects of the iron sand casting process, its advantages, applications, and future perspectives.
Understanding Iron Sand Casting
Iron sand casting, also known as sand casting, involves the creation of metal parts by pouring molten iron into a mold made from a mixture of sand and a binding agent. The primary component, iron sand, consists of tiny particles that are rich in iron, which provides the necessary properties for casting applications. The casting procedure begins with preparing a pattern, typically fashioned from wood or metal, which determines the shape of the final product.
The process can be broken down into several key stages
1. Pattern Making The first step involves creating a pattern that mirrors the design of the final product. This pattern is usually oversized to accommodate shrinkage that occurs during cooling.
2. Mold Preparation A mixture of iron sand and a bonding agent, often clay or resin, is used to form molds. The sand is compacted around the pattern to create a mold cavity. Proper compaction is crucial to ensure dimensional accuracy and surface finish.
3. Pouring After the mold is prepared, it is heated, and molten iron is poured into the cavity. The temperature of the molten iron typically ranges between 1300°C to 1500°C (2372°F to 2732°F), ensuring it flows well and fills the mold completely.
4. Cooling Once the molten iron fills the mold, it is allowed to cool and solidify. The cooling time can vary based on the size and complexity of the casting but is crucial for the formation of the desired mechanical properties.
5. Cleaning and Finishing After the cast has cooled, it is removed from the mold, and any excess material, known as sand, is cleaned off. Further finishing processes, such as machining, grinding, or painting, may be applied to achieve the final specifications.
Advantages of Iron Sand Casting
Iron sand casting offers several advantages that make it a preferred method in various industries
- Cost-Effectiveness The use of readily available materials, such as iron sand, and the simplicity of the process contribute to lower production costs compared to other casting methods
.iron sand casting process
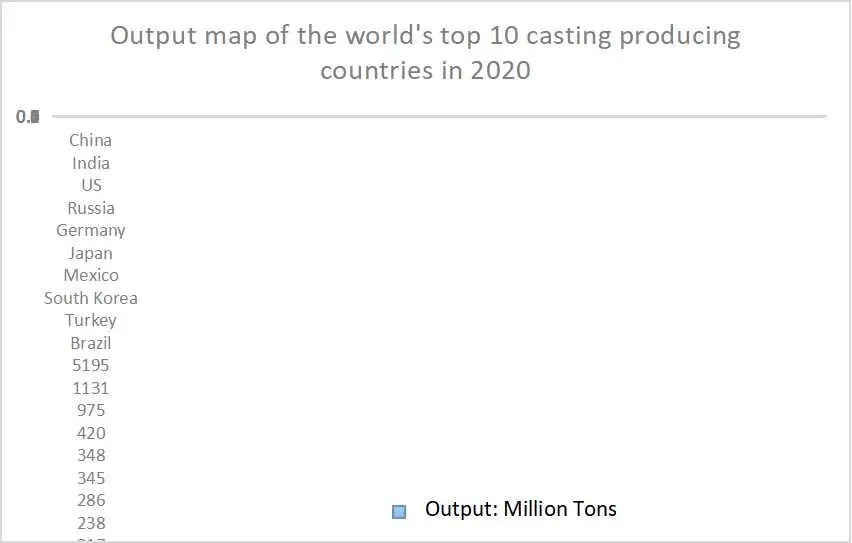
- Versatility This technique can produce a wide range of shapes, sizes, and weights, allowing for significant design flexibility.
- Durable Products Cast iron components exhibit excellent wear resistance and durability, making them suitable for high-stress applications.
- Scalability The process is easily scalable, meaning it can cater to small batch productions as well as large-scale manufacturing, adapting to the needs of the market.
Applications of Iron Sand Casting
Iron sand casting finds applications across various sectors, including
- Automotive Industry Components such as engine blocks, cylinder heads, and transmission cases are commonly produced using this method due to the strength and thermal properties of cast iron.
- Aerospace Cast iron parts are also used in the aerospace industry for various structural components, benefiting from the material’s lightweight yet durable nature.
- Heavy Machinery Equipment and machinery parts, including housings and frames, often utilize iron sand casting for their robustness and reliability under heavy loads.
- Construction Iron sand casting is employed for producing construction materials such as manhole covers, piping, and fixtures, where strength and longevity are paramount.
Future Perspectives
With advancements in technology, the iron sand casting process continues to evolve. The integration of computer-aided design (CAD) and simulation software is enhancing the precision of patterns and molds, reducing waste and improving efficiency. Furthermore, efforts toward sustainability are leading to the exploration of alternative binding agents and recycling methods for sand, thus minimizing the environmental impact of the casting process.
In conclusion, iron sand casting is a vital manufacturing process that combines efficiency, versatility, and cost-effectiveness to produce high-quality metal components. As industries continue to seek innovative solutions, the evolution of iron sand casting will likely play a crucial role in meeting future demands while addressing environmental concerns.
Post time:Sep . 27, 2024 19:40
Next:Techniques for Sanding and Finishing Ceramic Surfaces Effectively and Efficiently