The Art and Science of Sand Casting Iron
Sand casting is one of the oldest and most versatile metalworking processes still in use today. It involves creating a mold from a pattern, typically made of metal or plastic, which is then filled with molten metal to create a final product. One of the most commonly cast metals through this process is iron, specifically grey and ductile iron. The enduring relevance of sand casting iron can be attributed to its cost-effectiveness, ease of production, and ability to create complex shapes.
At the heart of sand casting iron is the use of a sand mixture, which serves as the medium for the mold. The primary component of this mixture is silica sand, which is mixed with a bonding agent, typically clay, and water. The bonding agent helps hold the sand grains together to withstand the pressure of the molten metal. The mold is created in two parts the cope (the top half) and the drag (the bottom half). These parts are assembled around the pattern, which is typically slightly larger than the final product due to the shrinkage of the iron as it cools.
One of the primary advantages of sand casting is its adaptability. It can produce both small, intricate items and large, heavy components. The process is particularly suited for producing small to moderately sized batches of castings, making it an ideal choice for job shops and foundries that cater to a variety of clients. Components like engine blocks, agricultural machinery parts, and decorative items can all be made using sand casting techniques with iron.
When molten iron is poured into the mold, it fills the cavity created by the pattern. The cooling process begins immediately, and as the metal cools, it solidifies into the shape of the mold. The cooling rate can affect the properties of the final casting; therefore, controlling the cooling process is crucial. For example, iron that cools slowly may form graphite flakes, resulting in a grey iron casting with good machinability, while quick cooling can lead to the formation of more ductile iron with improved strength and toughness.
sand casting iron
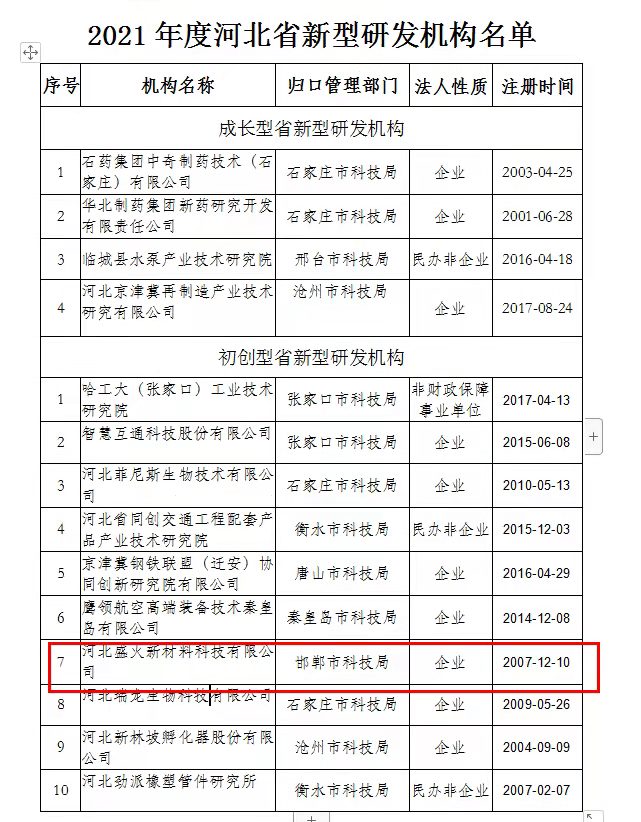
One of the critical factors in the sand casting process is the quality of the sand used in the mold. Reusability is an essential characteristic of sand, and most foundries can recycle the sand multiple times before it needs to be replaced. However, impurities such as moisture and contaminants must be controlled to ensure the production of high-quality castings. The use of additives can also enhance certain characteristics of the sand, including its ability to retain heat and resist deformation under pressure.
Despite its many advantages, sand casting iron is not without its challenges. For instance, defects such as porosity, inclusions, or surface imperfections can occur due to various factors, including gas entrapment or improper molding techniques. Foundries often employ inspection techniques such as X-ray or ultrasonic testing to identify and address these issues before the final products are delivered to clients.
The capabilities of modern technology have further enhanced the sand casting process. Computer-aided design (CAD) and computer-aided manufacturing (CAM) software have revolutionized the way molds and patterns are designed, allowing for greater precision and complexity. The introduction of 3D printing technology in mold making has also expedited the production process, reducing lead times drastically.
In conclusion, sand casting iron stands as a testament to the marriage of art and science in metalworking. Its ability to create diverse and complex shapes has secured its place in various industries, from automotive to aerospace. As technology continues to evolve, so will the techniques and methods associated with sand casting, ensuring that this venerable process remains relevant in an ever-changing manufacturing landscape. The continued innovation in materials and methods will allow for higher efficiency, reduced costs, and improved product quality, further solidifying sand casting iron's role as a cornerstone of modern manufacturing.
Post time:dec . 23, 2024 03:10
Next:Innovative Beads for Enhanced Ceramic Applications and Versatile Material Solutions