Understanding Foundry Sand Properties Essential Factors for Quality Casting
Foundry sand plays a crucial role in the metal casting process, serving as a mold material that shapes molten metal into a desired form. The properties of foundry sand significantly influence the quality and performance of the finished cast products. Consequently, an understanding of these properties is essential for foundry engineers and manufacturers to optimize casting processes and enhance product quality.
Types of Foundry Sand
The most commonly used foundry sand is silica sand, due to its excellent thermal stability and low expansion properties. Other types include clay-based sand, resin-coated sand, and synthetic sands. Each type has unique characteristics that cater to specific casting requirements. For instance, resin-coated sands offer superior strength and surface finish, making them ideal for intricate designs, while clay-based sands are preferred for their high plasticity and bonding capabilities.
Key Properties of Foundry Sand
1. Grain Size and Distribution The grain size of foundry sand affects its flowability and packing density. Fine sands can produce excellent surface finishes, but they may retain more moisture, leading to defects. Coarse sands provide good drainage and strength but may compromise detail in the final cast. An optimal grain size distribution combines both fine and coarse particles, ensuring a balanced performance.
foundry sand properties
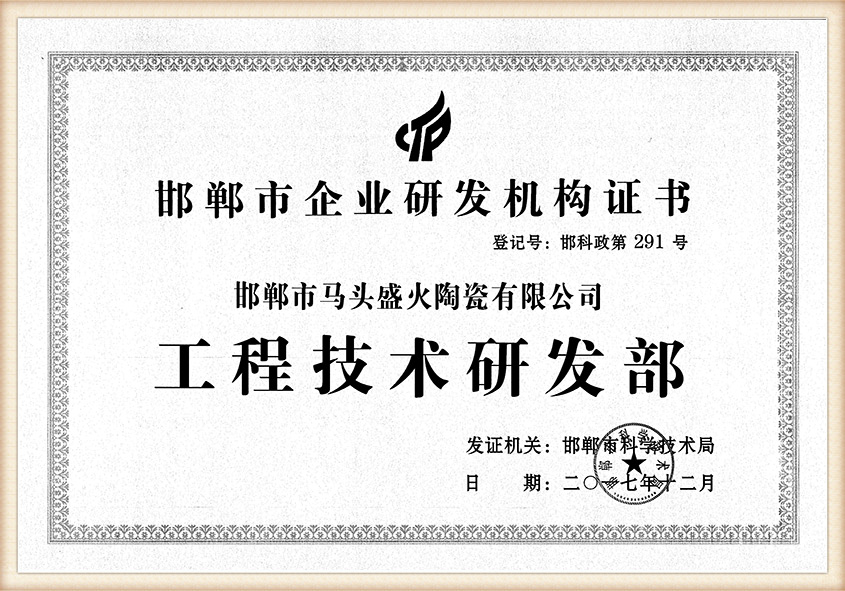
2. Shape and Roundness The shape of sand grains influences the bonding characteristics and stability of the mold. Rounded grains tend to provide better flow and reduce friction, leading to improved mold filling and overall casting quality. Irregular or angular grains, while providing better mechanical interlocking, can create issues with mold release and surface finish.
3. Moisture Content The moisture content of the sand mixture is critical in controlling mold hardness and strength. A carefully controlled moisture level can enhance the cohesiveness of the sand, helping to minimize defects such as blow holes or cracks during casting. Typically, the optimal moisture content ranges from 2% to 5%, depending on the specific application and sand type.
4. Thermal Properties Foundry sand must withstand high temperatures during the casting process without breaking down. The thermal conductivity of the sand affects how quickly it can absorb heat from the molten metal, influencing the cooling rate of the cast. High-quality foundry sand should have good thermal stability to prevent warping or deformation.
5. Reusability and Environmental Impact As sustainability becomes more vital in manufacturing processes, the recyclability of foundry sand is an essential property. Sands that retain their characteristics after reuse can significantly reduce costs and environmental impacts. Additionally, the ability to treat and reuse spent foundry sand helps in minimizing waste.
Conclusion
The properties of foundry sand are pivotal for achieving high-quality castings. By understanding and optimizing factors such as grain size, shape, moisture content, thermal stability, and reusability, foundry operators can enhance their casting processes for improved product performance. As the industry moves towards more sustainable practices, a thorough knowledge of foundry sand properties not only helps in producing superior castings but also supports environmental stewardship. By investing in research and development in this area, the foundry industry can continue to innovate and adapt to the evolving demands of modern manufacturing.
Post time:sep . 25, 2024 00:13
Next:Innovative Techniques in Rapid Sand Casting for Efficient Metal Production