Why Is Sand Casting Used?
Sand casting is one of the most versatile and widely used metal casting processes in the manufacturing industry. This method has been utilized for centuries due to its many distinctive advantages that make it an attractive option for both large-scale and small-scale production. From automotive components to intricate artistic sculptures, sand casting plays a crucial role in transforming raw materials into complex metal shapes. This article delves into the reasons behind the popularity of sand casting and explores its numerous benefits.
1. Cost-Effectiveness
One of the primary reasons for the extensive use of sand casting is its cost-effectiveness. The materials required for sand casting, primarily sand and a binder, are relatively inexpensive and readily available. Unlike other casting methods that may require expensive molds or specialized equipment, sand casting can utilize silica sand mixed with clay or resin and can be produced in various shapes without breaking the bank. The overall low investment in materials makes it an ideal choice for both high-volume and low-volume production.
2. Versatility in Design
Sand casting offers remarkable versatility when it comes to design and complexity. The process allows for the casting of geometrically intricate shapes that would be difficult, if not impossible, to achieve with other methods. This is particularly useful in industries that demand precise and complex components, such as aerospace, automotive, and machinery manufacturing. Furthermore, sand molds can accommodate large and hefty parts, making them suitable for a broad spectrum of applications.
3. Adaptability to Various Metals
Another significant advantage of sand casting is its ability to work with a wide range of metal alloys. Unlike certain casting processes that may be limited to specific materials, sand casting can accommodate ferrous and non-ferrous metals, including aluminum, bronze, and iron. This adaptability allows manufacturers to choose the most suitable material for their requirements, whether for strength, weight, or corrosion resistance.
4. Ease of Production
why is sand casting used
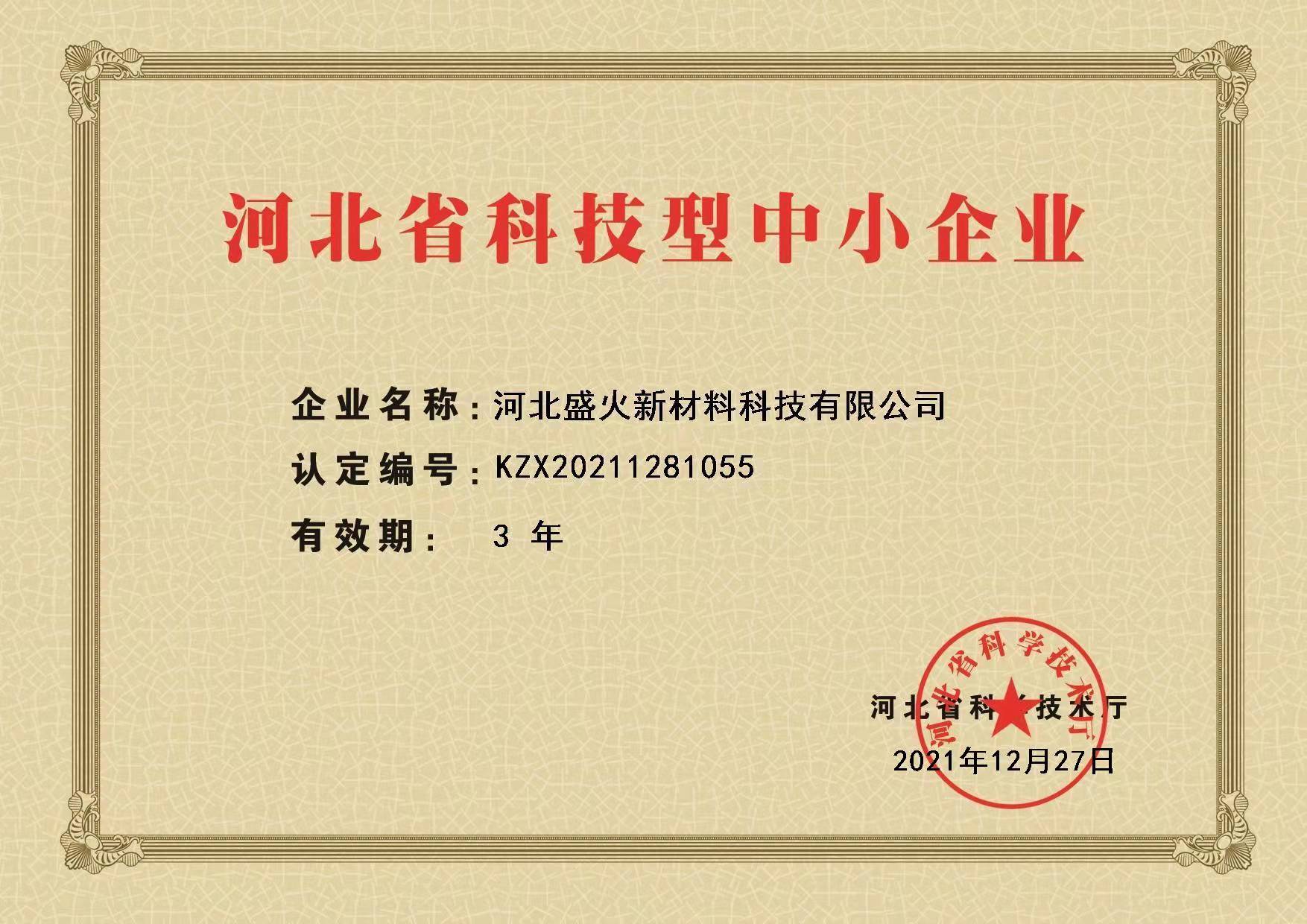
The sand casting process is relatively simple and does not require a high level of technical knowledge to operate. The basic steps include creating a mold, pouring molten metal, and allowing it to cool and solidify. This straightforward approach reduces the chances of production errors and allows for quicker turnaround times. Additionally, since sand molds can be reused, the production cycle becomes even more efficient, minimizing downtime and maximizing output.
5. Scalability
Sand casting is easily scalable, making it an excellent choice for both low and high production volumes. For small-scale projects, the setup costs are minimal, and the process can be carried out manually with minimal machinery. In contrast, for large-scale manufacturing needs, sand casting can be automated and optimized to create thousands of identical parts efficiently. This flexibility in scaling production is a major advantage for various industries looking to adapt to changing demands.
6. Good Surface Finish and Dimensional Accuracy
Despite the perception that sand castings may have rough surfaces, advancements in technology have improved the overall finish and dimensional accuracy achievable with sand casting. By using finer sand and modern binding agents, manufacturers can obtain smoother surface finishes and tighter tolerances, which reduce the need for additional machining or finishing processes. This results in a more efficient workflow and cost savings.
7. Environmental Considerations
Finally, sand casting has a lower environmental impact compared to other metal casting methods. The sand used can be recycled and reused multiple times, significantly reducing waste. The process typically consumes less energy, especially in comparison to more energy-intensive casting methods. Additionally, many foundries are now adopting more sustainable practices and materials in their sand casting processes, further enhancing their eco-friendliness.
In conclusion, sand casting remains a fundamental technique in the manufacturing world due to its economic, versatile, and efficient nature. With the ability to produce complex designs using various metals and the capability for both small-scale and large-scale production, it is clear why sand casting continues to be a go-to method for many industries. Its adaptability and cost-effectiveness not only make it a practical choice but also ensure its relevance in the future of manufacturing. As advancements in materials and technologies progress, sand casting will undoubtedly continue to evolve and thrive in an increasingly competitive market.
Post time:නොවැ. . 24, 2024 17:02
Next:Innovative Techniques in Lost Foam Casting Coating for Enhanced Precision and Efficiency