Materials Used for Sand Casting
Sand casting is one of the most widely used metal casting processes, renowned for its ability to produce complex shapes and sizes with relative ease. The technique involves pouring molten metal into a mold made of sand, and several materials are involved in both the mold creation and the casting process itself.
1. Sand The Primary Material
The primary material for sand casting is, unsurprisingly, sand. Specifically, silica sand is used for most applications due to its high melting point and excellent thermal properties. The sand must be of a particular grain size and shape to ensure that it can pack well and retain its form during the pouring of molten metal. The sand is typically mixed with a binding agent, which helps to hold the grains together and improve the mold's strength.
2. Binders Enhancing Mold Strength
Binders are essential additives that help agglomerate the sand particles, making the mold more durable. Common binders include clay (bentonite is often favored), resin, and water. Each type of binder has unique properties clay retains moisture, allowing the mold to be compact and cohesive, while resin provides a stronger bond at higher temperatures. This combination of sand and binders results in a mold that can withstand the thermal shock of molten metal.
3. Metal The Casting Material
what materials are used for sand casting
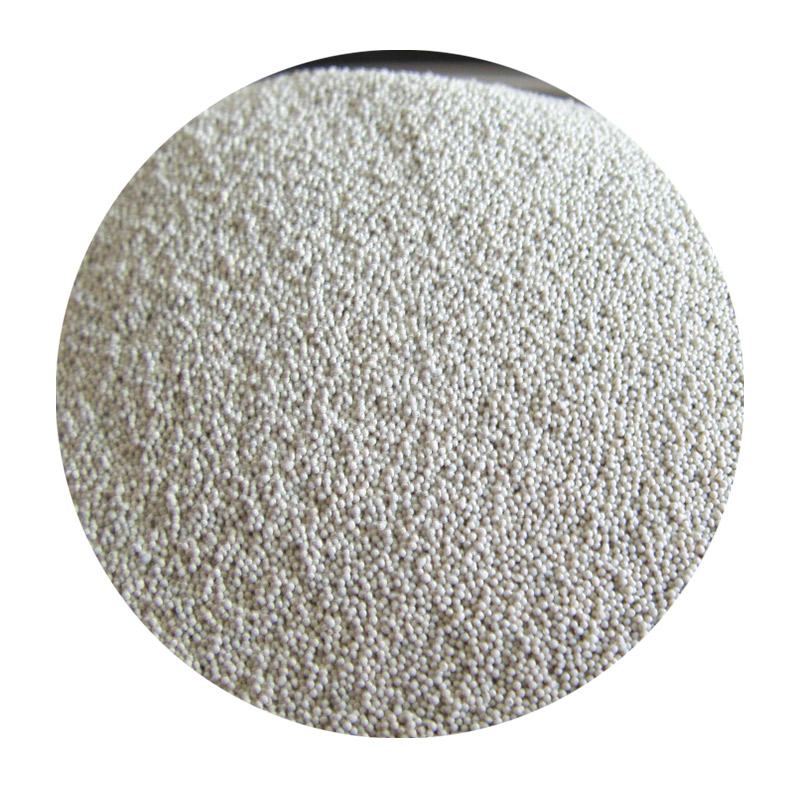
The type of metal used in sand casting can vary widely, depending on the application. Common metals include aluminum, iron, copper, and their alloys. Each metal has distinct melting points and flow characteristics, impacting the casting process and the final product's properties. For instance, aluminum is popular for its lightweight and corrosion-resistant properties, while cast iron is favored for its durability and wear resistance.
4. Coatings and Release Agents
To facilitate the casting process and reduce the risk of the metal adhering to the mold, various coatings and release agents are employed. These can include clay emulsions, oils, or specially formulated chemical agents that help protect the mold surface and ensure a smooth release of the final cast part.
5. Additives for Special Processes
In some advanced applications, additives may be mixed with the sand to enhance specific characteristics. For example, adding graphite can improve the flow of the molten metal and provide better surface finishes. Similarly, flux materials may be used to eliminate impurities and assist in the melting process.
In conclusion, sand casting is a versatile process that relies on a variety of materials, including high-quality silica sand, binders, molten metal, and auxiliary agents. Each component plays a crucial role in ensuring that the final cast product meets the required specifications and quality standards.
Post time:සැප්. . 12, 2024 06:45
Next:Fine Casting Sand - Optimal Solutions for Precision Casting