Steps in Sand Casting
Sand casting is a widely used metal casting process that involves pouring molten metal into a mold made from sand. This technique is favored for its simplicity, cost-effectiveness, and ability to produce complex shapes. The process involves several critical steps that ensure the successful creation of high-quality cast parts.
Step 1 Pattern Creation
The first step in sand casting is the creation of a pattern. This pattern is a replica of the final product and is typically made from materials such as wood, metal, or plastic. The design of the pattern includes allowances for expansion, contraction, and machining. The accuracy of the pattern is crucial because it directly influences the final dimensions and surface finish of the cast part.
Step 2 Mold Making
Once the pattern is ready, the next step is to create the mold. This involves placing the pattern in a mold box and packing sand around it. The sand used in this process is typically mixed with a binder to help it maintain its shape. After the packing process, the mold is carefully removed from the pattern, resulting in two halves that will form the casting cavity. The halves are then joined together to create a complete mold.
Step 3 Core Making (if needed)
steps in sand casting
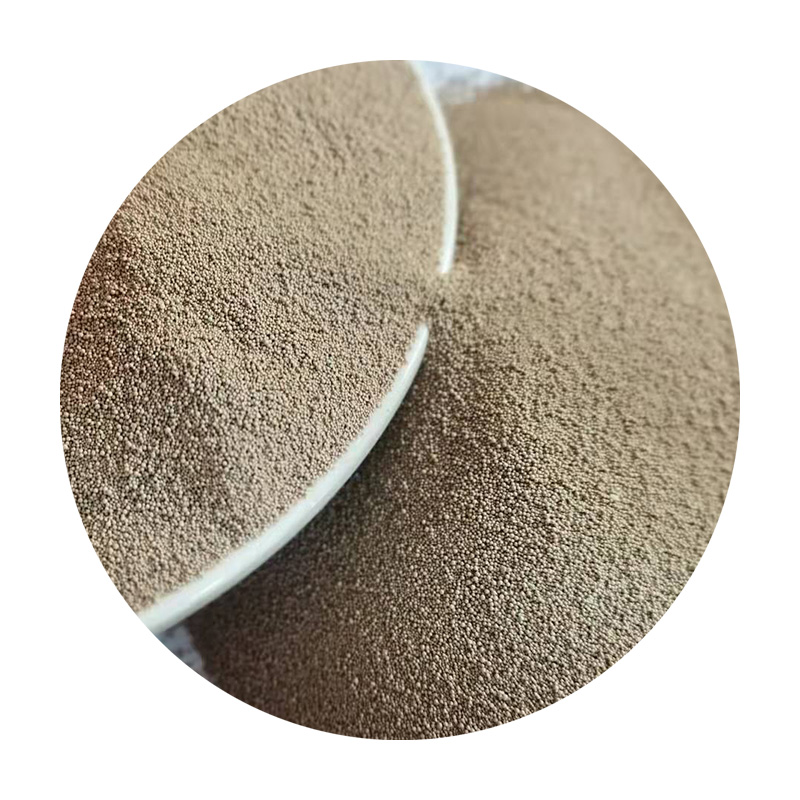
For complex shapes with internal cavities, cores are used. Cores are additional pieces of sand that are placed inside the mold to create these internal features. They are typically made using a similar sand mixture as the mold and are often coated with a thin layer of a binder to reinforce their structure.
Step 4 Pouring
With the mold prepared and cores in place, it's time to pour the molten metal. The metal is heated to its melting point and then carefully poured into the mold through a pouring cup and sprue. This step requires precision to prevent defects such as gas entrapment or cold shuts.
Step 5 Cooling and Finishing
After pouring, the metal must cool and solidify within the mold. The cooling time varies depending on the metal used and the thickness of the casting. Once cooled, the mold is broken away to reveal the cast part. Finishing processes, such as grinding, machining, and cleaning, are often necessary to achieve the desired surface finish and tolerances.
In conclusion, sand casting is a fundamental process in metalworking that combines artistry and engineering. By following these steps—pattern creation, mold making, core making, pouring, and finishing—manufacturers can produce a wide range of components for various industries, making sand casting a vital technique in modern manufacturing.
Post time:ඔක්. . 08, 2024 23:32
Next:sanding glazed ceramics