Sand Preparation in Foundries
Sand preparation is a crucial step in the foundry industry, playing a vital role in ensuring the quality and efficiency of metal casting processes. The quality of sand directly affects the mold's integrity, surface finish, and overall dimensional accuracy of the cast product. Therefore, understanding the intricacies of sand preparation is essential for foundry professionals aiming to optimize production.
The primary function of sand in foundry applications is to form molds that can withstand the high temperatures of molten metal while providing the necessary shape and details for the final product. To achieve this, foundries typically use silica sand, which is favored due to its abundance, thermal stability, and excellent mold-making properties. However, the sand must go through a thorough preparation process to ensure it meets the required specifications.
Sand Preparation in Foundries
Once reclaimed, the sand must be mixed with various additives to enhance its properties. Binder systems, such as clay or chemical binders, are often introduced to improve the sand's cohesiveness and binding ability. Additionally, other materials may be added to control the sand's permeability and strength. The precise formulation varies depending on the casting process being employed, whether it’s sand casting, shell molding, or another technique.
sand preparation in foundry
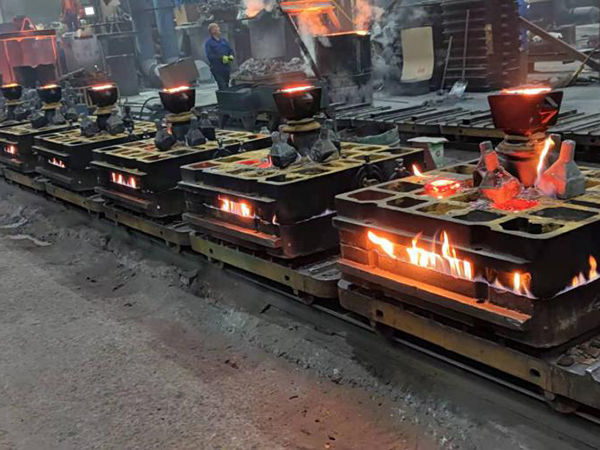
After mixing, the sand must be conditioned. This step involves adjusting the moisture content to achieve an optimal balance for molding. Proper moisture levels are crucial as they affect the sand's flowability and compaction, which are essential for creating a robust mold. Ensuring that the sand has the right moisture content can significantly reduce defects in casting, such as cracks or incomplete molds.
Another critical aspect of sand preparation is quality control. Foundries employ various testing methods to evaluate sand properties, such as grain size distribution, strength, and thermal stability. These tests help in identifying any variations in sand quality that could adversely affect the casting process. Techniques such as sieve analysis, permeability tests, and strength tests are commonly used to ensure that the prepared sand meets the required standards.
Furthermore, innovations in sand preparation technology continue to emerge. Automated sand handling systems and advanced mixing equipment have streamlined the preparation process, enhancing consistency and efficiency. The use of computer-controlled systems for monitoring sand properties has also gained popularity, allowing for real-time adjustments and ensuring optimal conditions throughout the production cycle.
In conclusion, sand preparation is an integral part of the foundry process that directly impacts the quality of the final products. Through careful reclamation, mixing, conditioning, and quality control, foundries can significantly improve their casting outcomes. As technology advances, the processes of sand preparation will continue to evolve, leading to greater efficiency and sustainability in the foundry industry. Understanding these processes enables foundry professionals to deliver high-quality castings that meet the demands of an ever-evolving market.
Post time:නොවැ. . 24, 2024 05:05
Next:Exploring the Techniques and Benefits of Open Sand Casting in Metalworking