Sand Casting Procedure A Comprehensive Guide
Sand casting, one of the oldest metal casting techniques, has stood the test of time due to its versatility, cost-effectiveness, and ability to produce complex shapes. This process utilizes sand as the primary material for the mold, and it is commonly employed in various industries, including automotive, aerospace, and manufacturing. This article will outline the essential steps involved in the sand casting procedure, ensuring clarity and understanding for those new to the process.
Step 1 Pattern Creation
The first step in sand casting involves creating a pattern, which is a replica of the desired final product. Patterns can be made from various materials, including wood, metal, or plastic, depending on the size and complexity of the part. The pattern must be slightly larger than the final product to account for shrinkage during cooling. It’s also important to incorporate features such as draft angles to facilitate easy removal from the sand mold.
Step 2 Mold Preparation
Once the pattern is ready, the next step is to prepare the sand mold. This begins with mixing the sand with a binder, which helps the sand grains stick together. The most commonly used binder is clay, though chemical binders are also popular for certain applications. The sand mixture is then compacted around the pattern, forming the mold cavity. The two halves of the mold, known as cope (top) and drag (bottom), must be properly aligned and secured to prevent leaks during pouring.
Step 3 Creating the Cavity
After compacting the sand around the pattern, the mold is opened and the pattern is removed, leaving behind a negative impression. To enhance the mold’s functionality, additional features such as pouring and venting systems are created. Pouring cups and sprues direct the molten metal into the cavity, while vents allow gas to escape during the pouring process. These features are critical for ensuring a smooth pour and preventing defects in the final casting.
Step 4 Melting the Metal
sand casting procedure
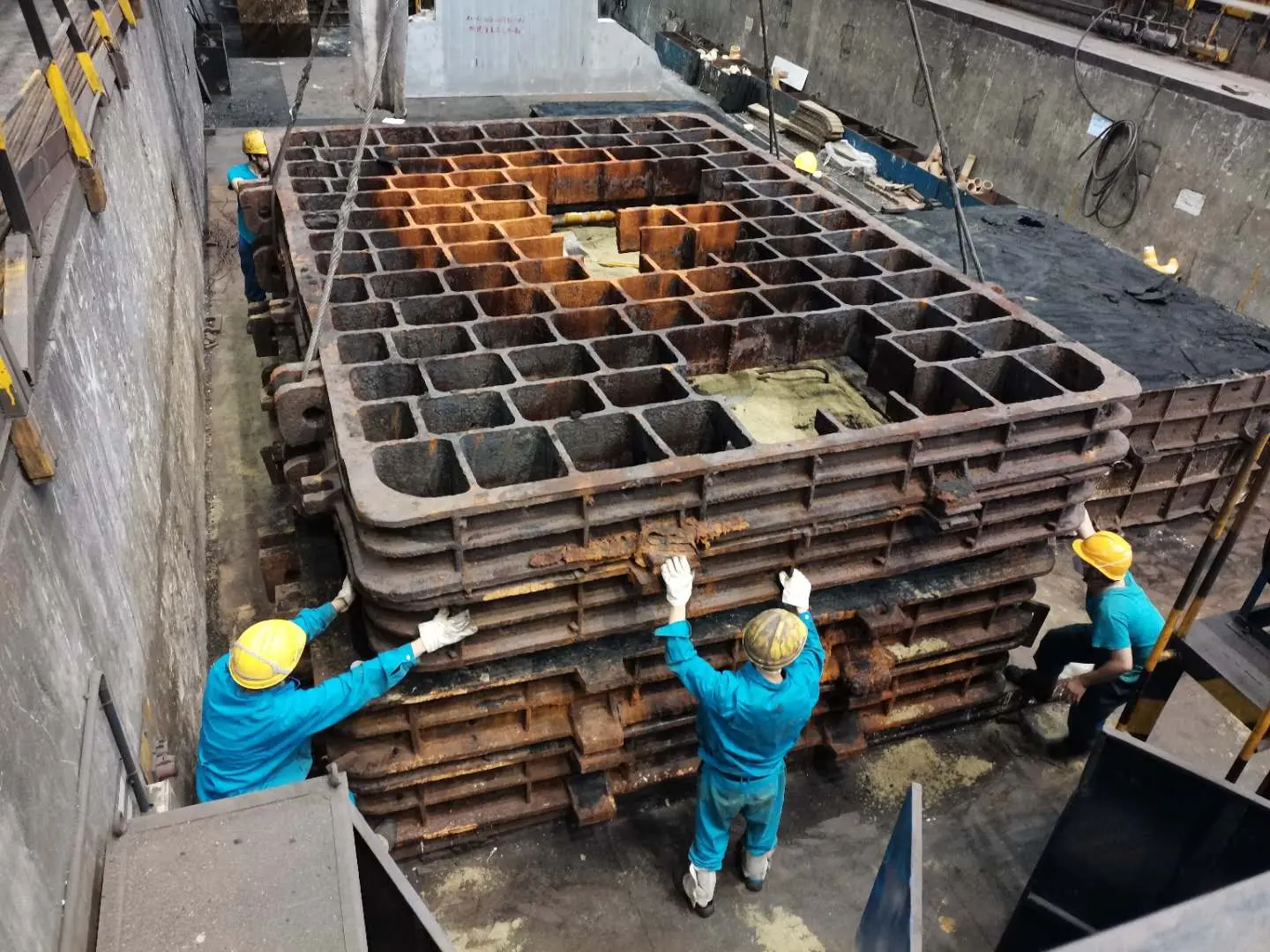
With the mold ready, the metal to be cast must be melted. Various metals can be used, including aluminum, iron, and bronze, each selected based on the specific requirements of the final product. The melting process can be performed using different methods, such as induction, electric arc, or propane furnaces, depending on the scale and type of operation. Once melted, the metal should be poured while at the optimal temperature to avoid solidification before reaching the mold cavity.
Step 5 Pouring the Metal
The next crucial step is the actual pouring of the molten metal into the prepared mold. This process must be executed with precision to minimize turbulence and oxidation. The molten metal must flow smoothly into the cavity, filling all sections and ensuring no air pockets remain. Proper pouring techniques are essential to achieve a high-quality casting and minimize defects.
Step 6 Cooling and Solidification
After pouring, the molten metal begins to cool and solidify within the mold. The cooling rate can significantly influence the mechanical properties and surface finish of the casting. Once the metal has completely solidified, typically after several minutes to hours depending on the material and thickness, the mold is then broken apart, and the casting is removed.
Step 7 Finishing Operations
Finally, the casting undergoes various finishing processes to achieve the desired specifications. These may include grinding, sandblasting, machining, and surface treatment to enhance the mechanical properties and aesthetics of the final product. Quality control is also an essential part of this step, ensuring that the casting meets the required standards.
In conclusion, sand casting is a reliable and efficient method of producing intricate metal parts. By following these key steps, manufacturers can effectively harness this age-old technique to create components that meet modern industrial demands. Whether it’s a small prototype or a large-scale production run, understanding the sand casting procedure is vital for anyone working in the metal casting industry.
Post time:නොවැ. . 19, 2024 06:38
Next:Enhancing Precision in Manufacturing with Fine Casting Sand Techniques and Applications