Sand Casting 101 An Overview of the Foundry Process
Sand casting, a time-honored manufacturing process, has been employed for centuries in the production of metal components. As a versatile and cost-effective method, it is widely used across various industries, including automotive, aerospace, and general manufacturing. This article provides an overview of sand casting, detailing the process, advantages, applications, and considerations for successful operation.
What is Sand Casting?
Sand casting is a process in which molten metal is poured into a mold made of sand to create a desired shape. The sand used in this method is typically mixed with clay and water to enhance its binding properties. The resultant mold is capable of withstanding the high temperatures of molten metal, which can exceed 1,500 degrees Fahrenheit (815 degrees Celsius) depending on the alloy being used.
The Sand Casting Process
The sand casting process can be broken down into several key steps
1. Pattern Creation A pattern, usually made of metal, wood, or plastic, is created to replicate the final product. The pattern must account for shrinkage that occurs during cooling.
2. Mold Formation Sand is packed around the pattern to form the mold. This step may be done manually or using a machine. The mold consists of two halves, the cope (top) and the drag (bottom), which are joined together.
3. Core Placement If the part requires internal features or cavities, cores made of sand or other materials are inserted into the mold.
4. Pouring the Metal Once the mold is ready, molten metal is poured into it. The metal flows into the cavity, filling the shape defined by the pattern.
5. Cooling The metal must be allowed to cool and solidify, which can take anywhere from a few minutes to several hours, depending on the size and material.
6. Mold Removal After cooling, the sand mold is broken away to reveal the cast part. This step often involves shaking or knocking the mold to dislodge the casting.
7. Finishing Operations The finished casting may require additional processes such as sanding, machining, or coating to achieve the desired surface finish and dimensions.
Advantages of Sand Casting
Sand casting offers several benefits, making it a popular choice in manufacturing
sand casting 101
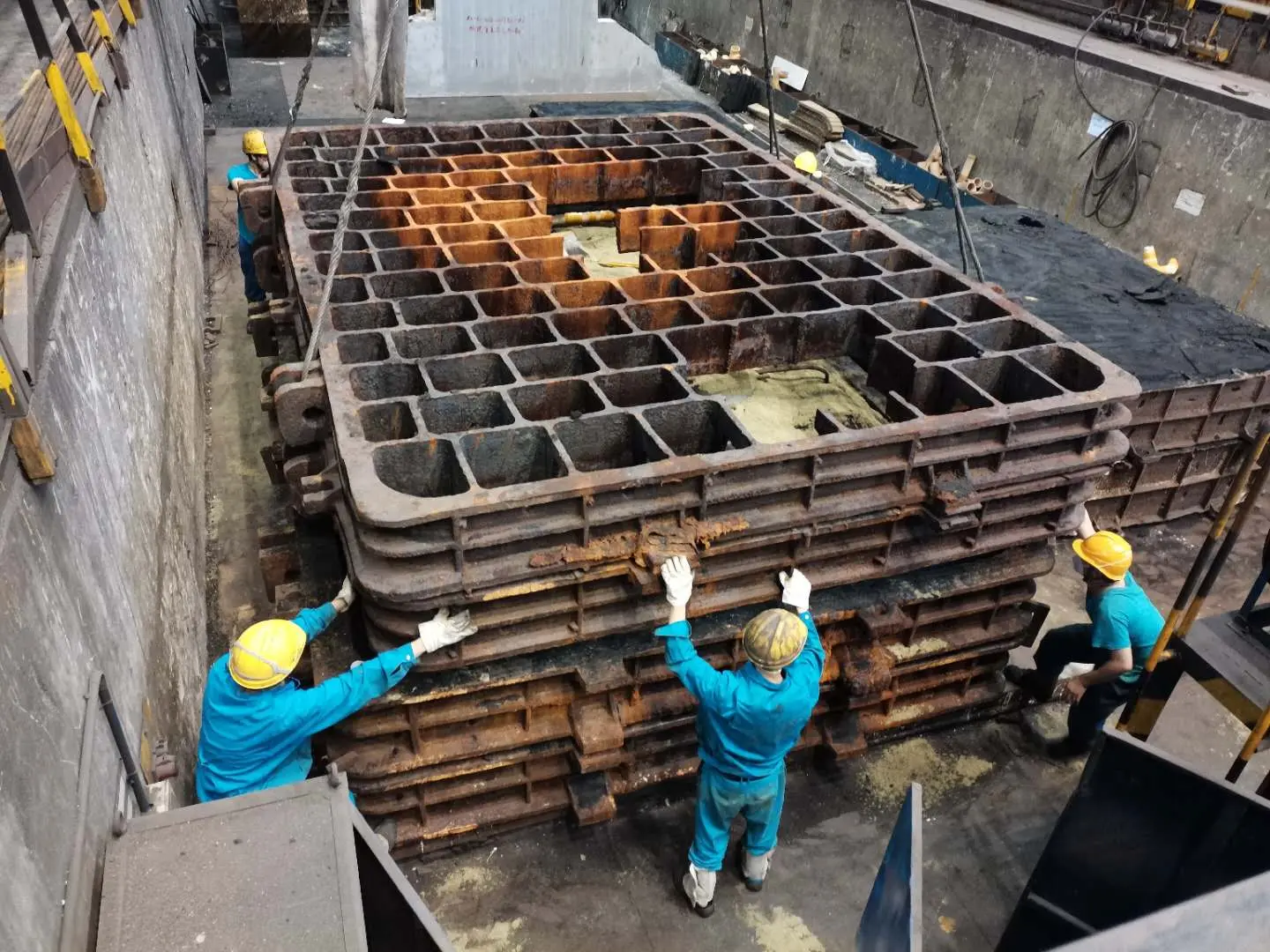
- Cost-Effectiveness The materials used in sand casting, primarily sand and metal, are relatively inexpensive. This process is economical for both short runs and large-scale production.
- Versatility Sand casting can accommodate a wide range of metals (ferrous and non-ferrous) and allows for the production of complex shapes and sizes.
- Large Part Production The method is capable of producing large components that other casting processes may struggle with.
- Rapid Prototyping Sand casting allows for quick turnaround times, enabling manufacturers to produce prototypes and test designs efficiently.
Applications of Sand Casting
Sand casting is utilized in various industries for creating a myriad of components. Common applications include
- Automotive Components Engine blocks, crankshafts, and transmission cases are often produced using sand casting due to the need for durability and strength.
- Aerospace Parts Critical components such as turbine housings and brackets that require high-performance materials are frequently manufactured through this method.
- Industrial Machinery Many machine parts, including gears and housings, benefit from the flexibility and robustness of sand castings.
Considerations for Successful Sand Casting
While sand casting is highly effective, several considerations must be made to ensure quality outcomes
- Pattern Design Attention to pattern details is crucial to avoid casting defects. Proper design and allowances for shrinkage need to be incorporated.
- Mold Quality The quality of the sand used and the mold formation process directly impact the final product's integrity.
- Temperature Control Maintaining appropriate pouring temperatures is essential to avoid issues like porosity and incomplete filling.
In conclusion, sand casting remains a foundational technique in the manufacturing world, providing efficiency and versatility in producing both simple and complex metal components. With careful attention to detail and modernization of practices, it continues to play a vital role in various industries. Whether for prototyping or large-scale production, understanding the nuances of sand casting can lead to significant advantages in manufacturing processes.
Post time:නොවැ. . 10, 2024 14:28
Next:Exploring the Richness of Golden Sands and Its Environmental Impact