Understanding the Role of Sand in Sand Casting
Sand casting is one of the oldest and most versatile manufacturing processes used in metalworking today. This technique involves pouring molten metal into a mold that has been formed from a sand mixture, and it primarily relies on the properties of sand. The type and quality of sand used in sand casting play a crucial role in determining the final properties and quality of the cast product.
The primary component of sand casting is silica sand, which is abundant and cost-effective. Silica sand is composed mainly of silicon dioxide (SiO2) and is favored for its high melting point, availability, and excellent thermal stability. One of the defining characteristics of sand used in casting is its grain size, which can significantly affect the mold's permeability, surface finish, and overall casting quality.
The sand mold is created by packing damp sand around a pattern, which is a replica of the final product. The damp sand holds its shape due to the presence of moisture and additives that improve its binding properties. The most commonly used additives are clay and water. Clay enhances the cohesion of sand particles, allowing for better mold strength and durability, while the moisture helps prevent cracking during the casting process.
sand used in sand casting
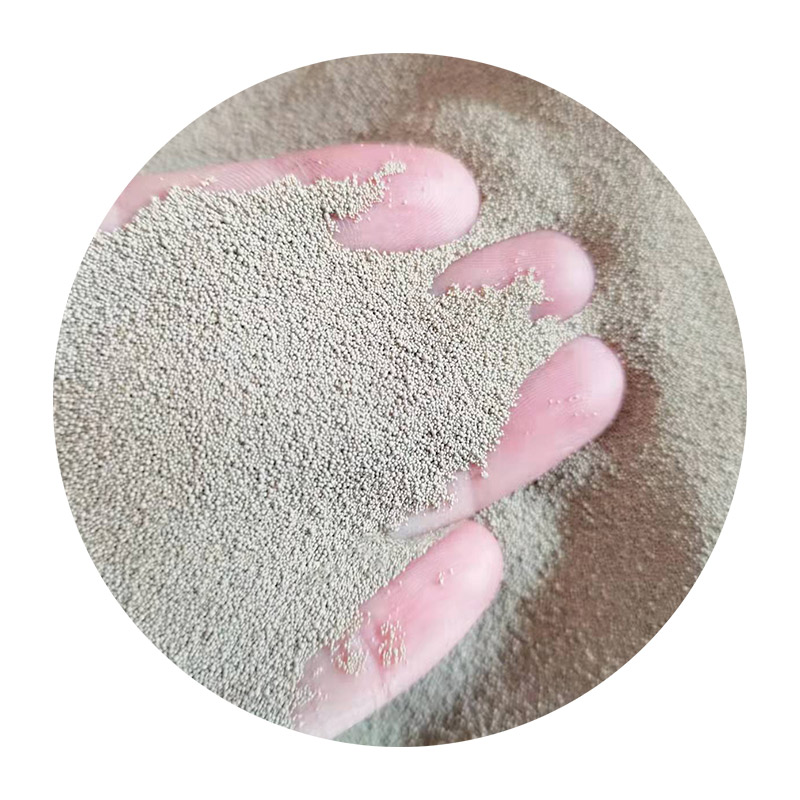
The ratio of sand to clay is critical for achieving the desired mold properties. Generally, a mixture containing about 10% clay and a sufficient amount of water yields optimal results. However, different types of sand, such as green sand, dry sand, or no-bake sand, require varying proportions of clay and moisture. Green sand, which contains about 15-30% clay, is popular for its ease of use and ability to create molds with good surface finishes. In contrast, dry sand molds, which are baked to solidify the sand, offer enhanced strength and rigidity.
Another essential property of sand used in casting is its refractory nature. A refractory material can withstand high temperatures without breaking down. The ability of sand to retain its shape and not distort under the heat of molten metal is vital in ensuring that the final product remains true to the original design. Furthermore, the sand should have minimal thermal expansion to prevent defects like warping or cracking of the mold.
Recycling sand is another important aspect of the sand casting process. After a casting is completed, the sand can often be reclaimed and reused for future molds. This not only reduces waste but also lowers production costs. However, it is essential to ensure that the recycled sand maintains its quality. This is achieved through methods such as screening to remove impurities and blending with fresh sand to restore the optimal properties.
In conclusion, the type and quality of sand used in sand casting are essential for the successful production of metal parts. The proper selection of sand, along with careful control of the molding process, can lead to high-quality castings with excellent mechanical properties and surface finishes. As technology advances, new materials and methods for sand casting continue to emerge, promising even greater efficiencies and capabilities in the foundry industry. With its cost-effectiveness and versatility, sand casting remains a cornerstone of manufacturing across various sectors.
Post time:සැප්. . 16, 2024 00:11
Next:Difference Between Sand Casting and Permanent Mold Casting