The Art of Sand Casting A Timeless Manufacturing Technique
Sand casting, a traditional metal casting technique, has been a cornerstone of manufacturing for centuries. This process involves creating a mold from sand, into which molten metal is poured to create a desired object. Despite the advent of advanced technologies and materials, sand casting remains popular due to its versatility, cost-effectiveness, and the ability to produce complex shapes.
The Sand Casting Process
The sand casting process begins with the creation of a pattern, which is essentially a replica of the desired final product. This pattern is typically made from materials such as wood or metal, and it can be designed to accommodate complex geometries. Once the pattern is ready, it is placed in a box made of two halves, known as the mold box.
Next, a mixture of fine sand and a binding agent is packed around the pattern to create the mold. The sand is usually mixed with a clay binder to enhance its cohesiveness and ability to hold fine details. After the sand is compacted, the pattern is removed, leaving a hollow cavity that mirrors the shape of the object to be cast.
The next step involves pouring molten metal into the mold cavity. The metal is heated to a temperature high enough to liquefy its solid form, and it is carefully poured to avoid introducing any impurities or defects. Once the metal fills the cavity, it is allowed to cool and solidify.
After the casting has cooled, the sand mold is broken away to reveal the final product. Finishing processes, such as grinding, machining, and polishing, may be applied to achieve the desired surface finish and dimensional accuracy.
make sand casting
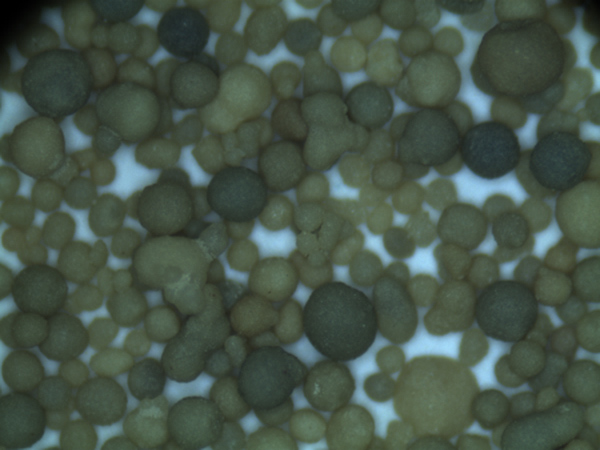
Advantages of Sand Casting
One of the primary advantages of sand casting is its adaptability to a wide range of metals, including aluminum, iron, and copper alloys. This versatility makes it suitable for many different industries, from automotive to aerospace. Additionally, it accommodates both small-scale production runs and large production volumes, making it an ideal choice for manufacturers.
Cost-effectiveness is another significant benefit. The materials used in sand casting are relatively inexpensive, and the process itself requires minimal capital investment compared to other casting methods. Moreover, sand molds can be reused for multiple castings, further reducing costs.
The sand casting process also allows for the production of complex shapes and intricate designs that may be difficult or impossible to achieve with other techniques. This capability has made sand casting a preferred method for creating prototypes and custom parts.
Conclusion
In conclusion, sand casting remains a vital and relevant method in the world of manufacturing. Despite the continuous evolution of technology, its simplicity, adaptability, and cost-effectiveness ensure its place in various industrial applications. As companies strive for innovation while managing costs, the timeless technique of sand casting stands as a testament to the blend of traditional craftsmanship and modern manufacturing needs. Whether creating intricate components for machinery or artistic sculptures, sand casting will likely continue to play a critical role in metalworking for generations to come.
Post time:නොවැ. . 06, 2024 23:26
Next:Výrobci písku s pryskyřičným povrchem pro průmyslové aplikace a stavebnictví