The Iron Sand Casting Process An Overview
Iron sand casting, also known as iron sand mold casting, is an ancient technique that involves the use of iron-rich sand to create durable and complex metal components. This process has been utilized for centuries in various cultures, particularly in regions where natural iron sand deposits are abundant. Today, it remains an essential method in manufacturing due to its cost-effectiveness and versatility.
Understanding Iron Sand Casting
The iron sand casting process primarily involves three key stages preparation of the mold, pouring of molten metal, and finishing the cast product. This method leverages the unique properties of iron sand, which is predominantly composed of magnetite (Fe3O4) and can withstand high temperatures without breaking down.
1. Mold Preparation The first step in the iron sand casting process is the preparation of the mold. This involves mixing iron sand with a suitable binding agent, often a type of clay, to form a pliable material that can hold its shape when packed. The mixture is then compacted around a pattern, which is a replica of the object that needs to be cast. Once the mold is formed, it is allowed to set and harden, ensuring that it can withstand the pouring of molten iron without deforming or leaking.
2. Pouring Molten Metal After the mold has been prepared, the next step is pouring molten iron into it. The iron is typically melted in a furnace and can be alloyed with other metals to achieve desired properties. Once the molten metal reaches the appropriate temperature, it is carefully poured into the mold cavity. The iron sand's fine granules can easily fill intricate patterns, making it suitable for complex designs. The cooling process begins immediately upon pouring, allowing the iron to solidify and take the shape of the mold.
3. Finishing the Cast Product Once the metal has cooled and solidified, the mold is broken apart to reveal the cast product. This stage often involves various finishing processes such as sandblasting, machining, and polishing to achieve the desired surface finish and dimensional accuracy. Any excess sand and impurities are removed to ensure the final product meets specifications.
Advantages of Iron Sand Casting
iron sand casting process
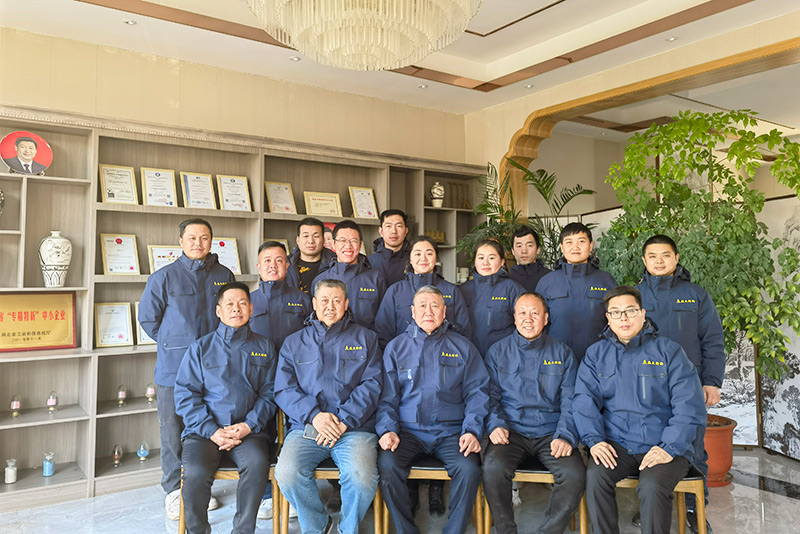
Iron sand casting offers several advantages over other casting methods. One of the primary benefits is its cost-effectiveness. The raw materials required for iron sand casting, namely iron sand and a binding agent, are generally inexpensive and readily available. This makes the process economically feasible for producing large quantities of parts.
Furthermore, the versatility of iron sand allows for the production of a wide range of complex shapes and sizes. The fine texture of the sand ensures that even intricate designs can be replicated faithfully in the casting, making it ideal for applications in various industries, including automotive, aerospace, and construction.
Another significant advantage is the recyclability of materials. The sand used in the casting process can often be reused multiple times, reducing waste and lowering material costs. Additionally, the environmental impact of iron sand casting is typically lower compared to other metalworking processes, as it generates less scrap material.
Applications of Iron Sand Casting
Due to its numerous benefits, iron sand casting is employed in various applications. It is extensively used in the automotive industry for manufacturing engine blocks, components, housings, and brackets. The aerospace sector also adopts this method for producing lightweight and durable parts. Moreover, construction equipment and machinery often utilize cast iron products manufactured through this method, showcasing the versatility and reliability of iron sand casting.
Conclusion
Iron sand casting is a time-honored manufacturing process that continues to thrive in modern industry. Its ability to produce complex, high-quality components at a low cost makes it a valuable technique in various sectors. As technology advances, the methods and materials used in iron sand casting are likely to evolve, further enhancing its efficiency and sustainability in the manufacturing landscape.
Post time:නොවැ. . 15, 2024 00:04
Next:describe sand casting