Investment Casting vs. Sand Casting A Comparative Analysis
When it comes to metal casting processes, two prominent methods stand out investment casting and sand casting. Both techniques have their unique applications, advantages, and limitations, which make them suitable for different types of projects. Understanding these differences is crucial for manufacturers and engineers when deciding which casting method to employ based on their specific needs.
Investment Casting Overview
Investment casting, also known as lost-wax casting, is a precision casting process characterized by its ability to produce intricate shapes with high dimensional accuracy. The process begins with creating a wax pattern that is coated with a ceramic shell. Once the shell hardens, the wax is melted and drained away, leaving a detailed cavity. Molten metal is then poured into this cavity to create the final product. This method is ideal for producing complex designs, fine details, and tight tolerances, making it popular in industries such as aerospace, automotive, and medical devices.
One of the primary advantages of investment casting is its versatility in handling a variety of materials, including aluminum, brass, stainless steel, and even titanium. Additionally, the process can yield a smooth surface finish that often eliminates the need for extensive machining. However, investment casting also has its downsides; it tends to be more expensive than other methods due to the cost of the patterns and the intricate setup involved. It is most beneficial for small to medium production runs, where precision is critical.
Sand Casting Overview
investment vs sand casting
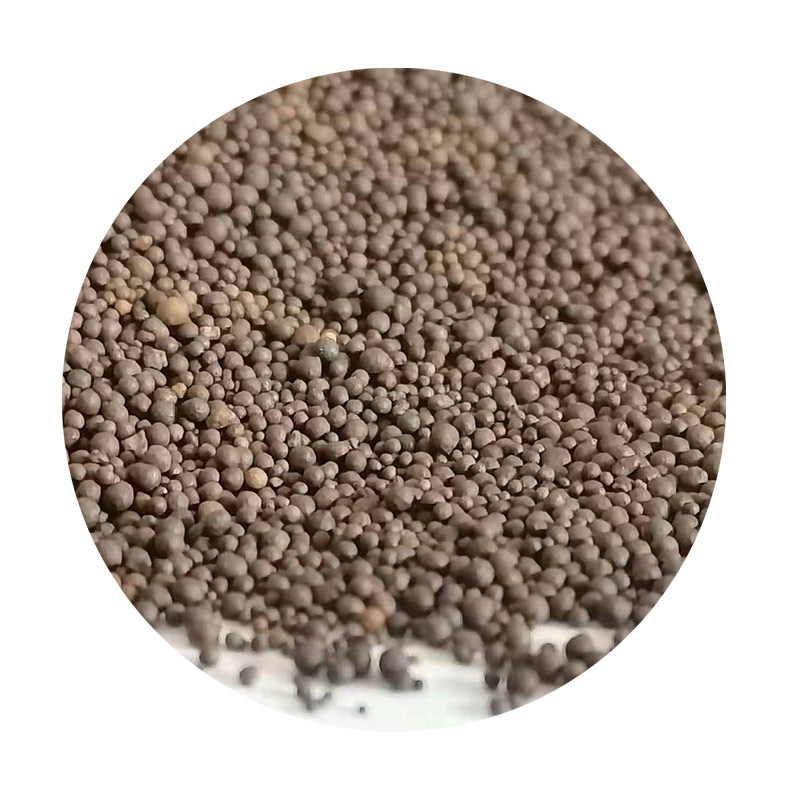
Sand casting is one of the oldest and most widely used casting methods. In this process, molds are created using sand, which is typically bound with clay and water. The desired shape of the object is formed by compacting the sand around a pattern. After forming, the pattern is removed, and molten metal is poured into the cavity to take the shape of the mold. Once the metal solidifies, the sand mold is broken apart to reveal the casting.
The primary advantage of sand casting is its cost-effectiveness and simplicity. It is particularly well-suited for large production runs and can accommodate a wide range of metal types, including ferrous and non-ferrous alloys. Furthermore, the sand mold can be reused, making the process more efficient for larger projects. However, sand casting typically results in a rougher surface finish and less precision compared to investment casting, which may require additional machining for certain applications.
Key Comparisons
In terms of cost, sand casting usually wins due to its lower setup and material costs, making it a favorable option for large-scale production. Conversely, investment casting offers superior precision, which justifies its higher price for smaller, more complex components.
Ultimately, the choice between investment casting and sand casting hinges on the specific requirements of the project, including design complexity, material needs, quantity, and budget constraints. By carefully weighing these factors, manufacturers can select the most appropriate casting method to achieve optimal results and ensure the efficiency of their production processes.
In summary, while both investment and sand casting methods have their distinct advantages and applications, making an informed decision based on project specifications is essential for successful outcomes in the casting industry.
Post time:ඔක්. . 12, 2024 11:56
Next:resin coated sand uses