How Sand Casting is Done
Sand casting is one of the oldest and most widely used metal casting processes. It employs sand as the primary molding material and is favored for its compatibility with a variety of metals and for its ability to create complex shapes with intricate details. In this article, we will explore the step-by-step process of sand casting, elucidating its various phases and highlighting its significance in manufacturing.
1. Preparation of the Pattern
The sand casting process begins with the creation of a pattern, which is a replica of the object that is to be cast. Patterns can be made from various materials, including wood, metal, or plastic. The choice of material depends on the production volume and the desired finish of the final product. Patterns must be designed with consideration for shrinkage that occurs during the cooling of the molten metal. Often, patterns have a slight oversized dimension to accommodate this change.
2. Making the Mold
Once the pattern is ready, the next step is to create the mold. This is typically done using a mixture of sand and a bonding agent (usually clay and water). The mixture is packed tightly around the pattern either by hand or using automated machines. The process involves enclosing the pattern and creating a hollow cavity that will define the shape of the final casting.
To ensure ease of removal, the sand mold is constructed in two halves, known as the cope (top half) and the drag (bottom half). Once the sand has been packed and shaped around the pattern, the two halves of the mold are separated, and the pattern is carefully extracted, leaving behind a precise cavity that will hold the molten metal.
3. Adding Pouring System and Venting
After the pattern is removed, a pouring system is incorporated into the mold. This system includes a sprue (the channel through which the molten metal enters the mold) and runners (which distribute the metal to the various parts of the mold). Venting is also necessary to allow gases to escape during the pouring of the metal, preventing any defects in the casting.
4. Melting the Metal
The next phase is melting the metal that will fill the mold. Common metals used in sand casting include aluminum, bronze, and cast iron. The metal is heated in a furnace until it reaches a molten state, usually at temperatures ranging from 650 to 1300 degrees Celsius, depending on the metal type.
how sand casting is done
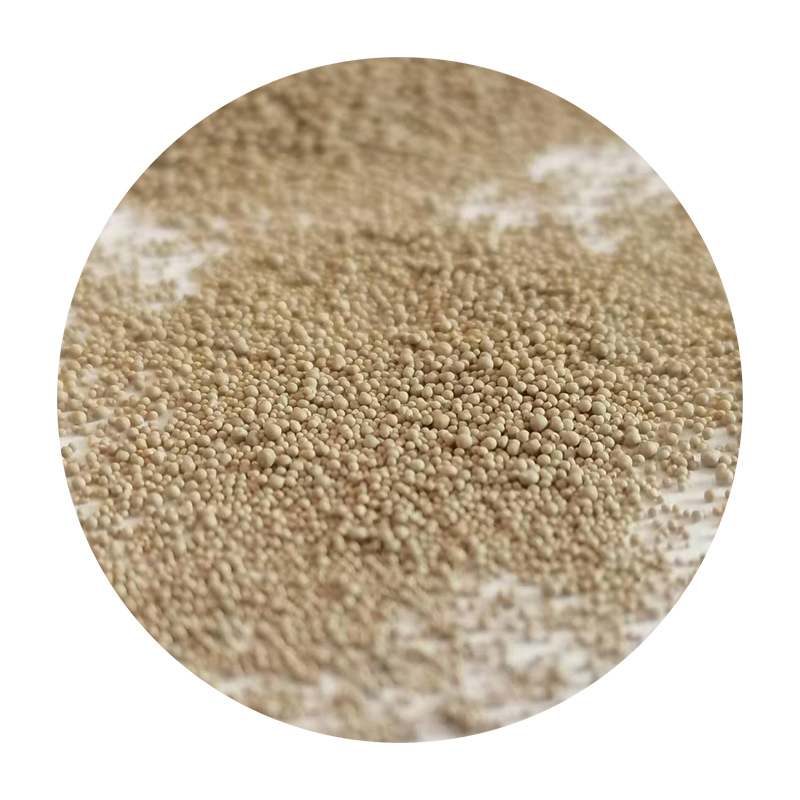
Proper temperature control is critical, as overheating can cause oxidation, which compromises the quality of the metal
.5. Pouring the Molten Metal
Once the metal is melted, it is poured into the mold through the sprue. The pouring must be done carefully to avoid splashing and to ensure that the mold is filled uniformly. Timing and techniques are vital, as the metal begins to cool and solidify upon contact with the sand.
6. Cooling and Solidification
After pouring, the molten metal must cool and solidify, which typically takes a few minutes to several hours, depending on the metal and the thickness of the casting. Cooling rates impact the properties of the metal, including its strength and microstructure, so this stage is crucial for achieving the desired characteristics in the final product.
7. Removing the Casting
Once the metal has cooled adequately, the mold is broken open to reveal the casting. This can be done by knocking off the sand or using vibrations to facilitate separation. The casting is then removed, and any excess metal (known as flash) is trimmed away.
8. Finishing Touches
Finally, the casting undergoes finishing processes, including sandblasting, grinding, or machining, to achieve the desired surface finish and final dimensions. Quality checks and inspections are performed to ensure that the casting meets the required specifications.
Conclusion
In summary, sand casting is a versatile and widely used technique in metalworking that allows for complex shapes and high levels of customization. Its straightforward process, along with the ability to work with various metals, makes it an invaluable method in industries ranging from automotive to aerospace. With the right techniques and quality control, sand casting can produce robust and precise components integral to numerous applications.
Post time:දෙසැ. . 16, 2024 00:58
Next:what is sand casting used to make